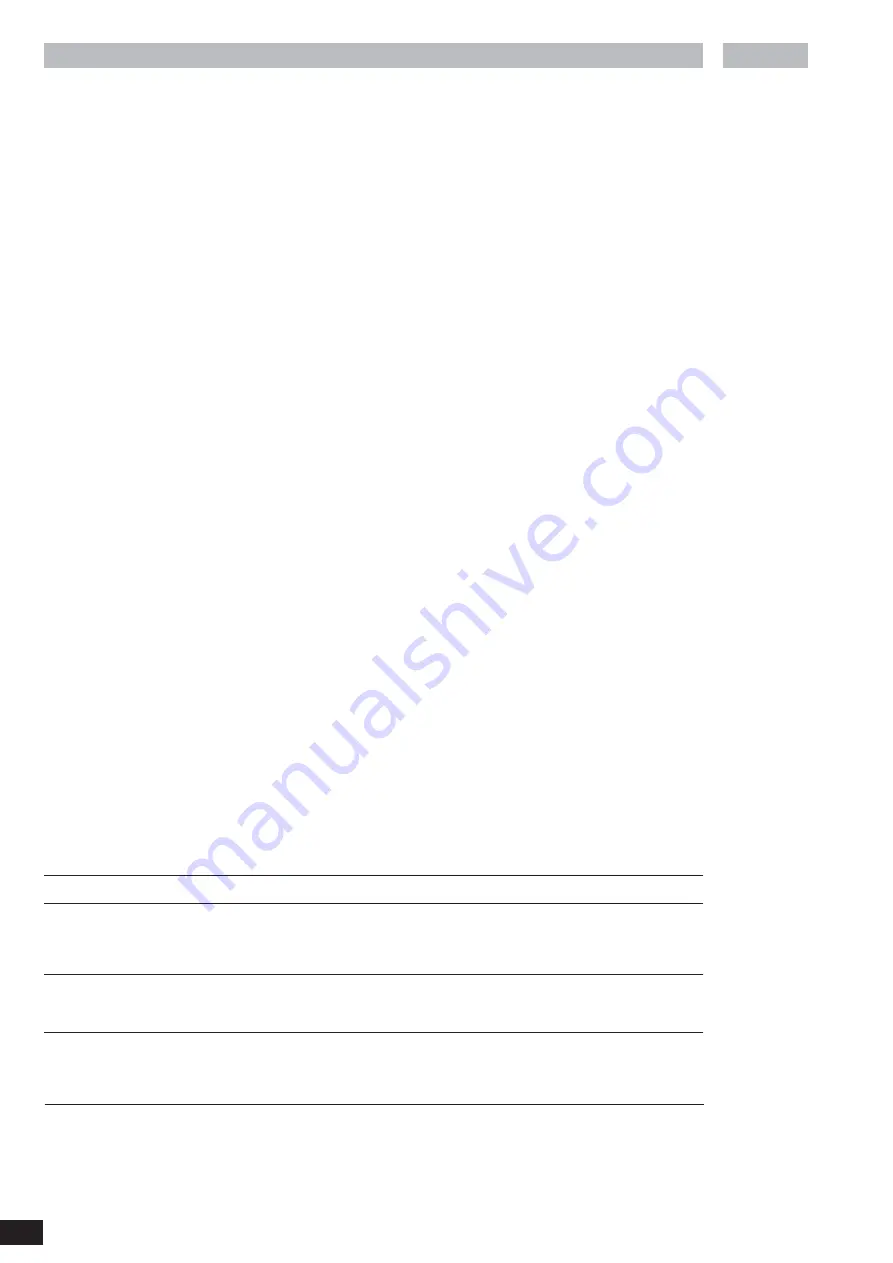
34
042009
Distillation is a thermal separating process for liquid compounds based
on substance-specific, pressure-dependent boiling points through eva-
poration and subsequent condensation.
The boiling point temperature decreases with decreasing external
pressure which means that work is usually done under reduced
pressure. In this way the heating bath can be maintained at a con-
stant temperature (e.g. 60 °C). Using the vacuum, the boiling point
is set with a steam temperature of approx. 40 °C. The cooling water
for the condensation cooler should not be warmer than 20 °C (60-
40-20 rule).
A chemical resistant membrane pump with a vacuum controller
should be used to create the vacuum. The pump is protected from
solvent residue by the addition of a Woulff bottle and/or a vacuum
separator.
Working with a jet pump to create a vacuum can only be recom-
mended to a limited extent as the solvents may contaminate the
environment when using these systems.
Speed, temperature, piston size and system pressure all affect the
evaporator air capacity.
The optimum capacity of the flow-through condenser is approx. 60%.
This corresponds to condensation on approx. 2/3 of the cooling coil.
With larger capacities there is the risk that the uncondensed solvent
vapour will be extracted.
In order to prevent this, the condenser loading safety monitoring sy-
stem can be activated. Before activating the safety monitoring, first
carry out several distillations, noting the value given under menu
“Settings”, menu option “Drive”, item “Maximum heat rejection
rate”. Now calculate the heat rejection rate using the following for-
mula:
Heat rejection rate threshold = maximum heat rejection rate * 1.3
Enter this value under menu “Settings”, menu option “Distillation”,
item “Heat rejection rate threshold”. The device will now stop the
measurement and issue an error message if the threshold for the
condenser is exceeded. If the configuration of the condenser equip-
ment or the distillation process is modified, then it may be necessary
to re-evaluate the maximum condenser loading.
The factory setting for this value is 900 W.
The device is equipped with a piston-operated safety mechanism. A
vacuum may form in the glassware assembly if there is a power ou-
tage; this will be vented when the system is switched on again. If
the power cuts out, the evaporator piston is automatically lifted out
of the heating bath by an integrated gas spring.
CAUTION!
The maximum load (evaporator piston and contents) is
1.5 kg for a permissible safety lift with no power for glass apparatus
with diagonal or vertical condenser.
When using other types of condensers such as dry ice or intensive
condensers as well as when using return distillation distributors with
slip-on condensers, it may be necessary to reduce the mass of the
media to compensate for the mass of this additional glassware.
Thus, prior to distillation, check whether the lift goes up without
power when laden with the glass and distillation material.
In addition to offering a full range of manual and semi-automatic
evaporation operating modes, the RV 10 control rotary evaporator
can also be used for fully automatic, quantity-controlled evapora-
tion processes. Standard fittings for fully-automatic operation in-
clude a two-position vacuum controller, a cooling water
differential temperature measurement sensor, and a cooling
water flow rate meter. The device is designed for operation with
a cooling water supply system (e.g. laboratory thermostat), but
can also be run off a water supply line. Please refer to the Tech-
nical Data for information on cooling water pressure, temperature
constancy, and flow rate.
We recommend using the RV10.5001 water regulator valve when
operating directly off a water supply line.
This valve allows the cooling water flow rate to be adjusted and au-
tomatically cuts off the cooling water supply on completion of the di-
stillation process.
The RV10.5002 water filter can be used to prevent particles of dirt
passing from the water supply line into the valve mechanism.
If pressure reduction is required, we recommend fitting the
RV10.5003 pressure regulator valve in the pipe immediately downst-
ream of the pick-off point.
Automatic volume-dependent distillation
: The apparatus must
be brought up to operating temperature. This is achieved by con-
ducting a test distillation.
Please observe the specified values during automatic distillation (see
“Technical specifications”).
Useful information
Vacuum source
Code
Valve
Central vacuum system
Large-scale vacuum source for
RV 10.4001
multiple consumers of different
types across a site;
generally a fixed-pipe installation.
Laboratory vacuum system
Laboratory-based RV vacuum pump
RV 10.4002
with multiple similar consumers,
e.g. 2 rotary evaporators/1 pump.
Single pump system
One rotary evaporator with one pump/
RV 10.4003
desktop operation.
Pump is deactivated when target pressure
reached and reactivated automatically.
Vacuum equipment: The RV 10 control rotary evaporator is fitted as standard with a two-position vacuum controller and a pressure mea-
suring chamber with bleed valve.
The correct vacuum valve must be selected from the following list and installed according to the type of vacuum source used at the
customer site.
Содержание RV 10 control
Страница 1: ...38 594 00 IKA RV 10 control 042009 Betriebsanleitung DE 5 Operating instructions EN 32 Reg No 4343 01...
Страница 2: ......
Страница 59: ......