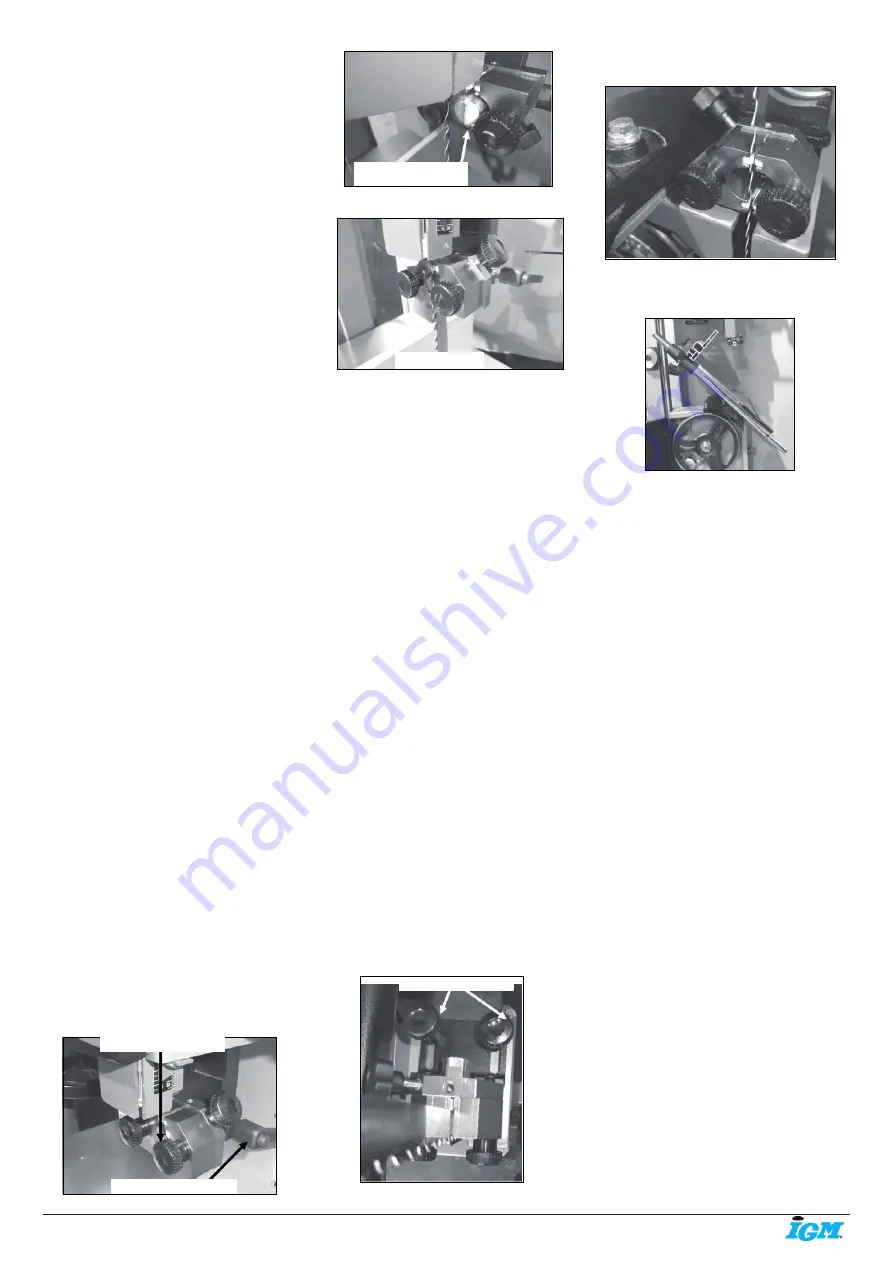
-11-
www.igmtools.com
5. The 14-12 Laguna guide system can be used
with 1/8“ to 3/4“ blades.
6. The Laguna guide system uses ceramic to
support and guide the blade. This has many
advantages (very poor conductor of heat, very
resistant to wear, etc.). The disadvantage is
that it is very brittle, so the guides must never
be dropped, exposed to hard knocks, hit with
hard objects or used with badly welded blades.
Any of the above actions may cause the
ceramic to chip or break and will detract from
the performance of the Laguna guide system.
Any mistreatment of the guide system will
render the warranty void.
7. The side guide blocks must be tightened
before running the machine to avoid jamming
the blade and damaging the machine and/or
guide blocks.
8. When cutting gummy or green wood, the
blade can become covered with resin. You will
find that the surround guide system ceramic
blocks remove the resin as the blade is moved
through the guide blocks and keep that
part of the blade clean. For this reason it is
recommended that the blocks be adjusted as
close to the gullet as possible, but the teeth
must not come in contact with the blocks, as
they will become damaged. Although the guide
blocks clean the blade, some woods will still
gum the blade and the resin will have to be
removed with solvent.
7.6 Adjusting the blade guides
The blade should run through the center of
the rear blade guide, and the side guides
should be parallel with the blade. If they have
been moved out of adjustment, adjust as
follows:
Top Upper Side Guides Parallel
Adjustment.
Loosen the side guides and move out as far as
possible. Loosen the guide assembly and
move back away from the blade.
Move the back blade guide forward so it just
touches the back of the blade and lock in
position.
Loosen the guide clamp screw that allows the
side guides to move forward and back. Adjust
so that the ceramic blocks are just behind the
gullet of the teeth and are parallel to the blade.
Retighten the clamp screws.
Gently push one side guide so that it touches
the blade and lock it in position. Bring the other
guide toward the blade so that there is minimal
clearance between the blade and the guide.
You can put a thin piece of paper to put
between the blade and the guide to obtain the
correct clearance until you gain experience.
Tighten the clamp screws and remove the
paper. Rotate the blade by hand, ensuring that
the weld of the blade does not hit the ceramic
blocks, as this will cause damage. If the blade
has a bad weld, dress the blade or return it to
your supplier. Rotate the blade by hand and
check that the back of the blade does not hit
the blade guide with a bad weld. If the back of
the blade hits the back blade guide at the weld,
then dress the blade or, in excessive cases,
return the blade to the supplier.
Pic. 45
Pic. 46
Pic. 47
Lower blade guide
The lower blade guides have two locking
screws that, when released, allow the guide
assembly to be moved forward and back.
Rotate the blade by hand and ensure that it
is tracking consistently in the correct position.
Loosen the side guides and move out from the
blade. Loosen the two clamp screws that allow
the guide assembly to move forward and back.
Adjust it so that the ceramic blocks are just
behind the gullet of the blade and retighten the
clamp screws.
Place a dollar bill or piece of paper of similar
thickness between the guide blocks and the
blade. Gently bring both side guides toward the
blade so that slight pressure is exerted on the
blade. Tighten the clamp screws and remove
the paper. Rotate the blade by hand, ensuring
that the weld of the blade does not hit the
ceramic blocks, as this will cause damage. If
the blade has a bad weld, dress the blade or
return it to your supplier.
Loosen the rear guide clamp screw and push
the guide forward so that it just touches the
back of the blade.
Tighten the guide in position. Rotate the blade
by hand and check to see that the back of
the blade does not hit the blade guide with a
bad weld. If the back of the blade hits the rear
blade guide at the weld, then dress the blade
or, in excessive cases, return the blade to the
supplier.
Note
: You will probably find that the guides can
be adjusted more easily by tilting the table to 45
degrees.
Note
: Rotate the back guide by approximately
15 degrees after every 8 hours of use. This will
greatly extend the life of the back blade guide,
as it will even out the wear.
Before you cut any wood, read the safety
rules at the front of this manual.
Pic. 48
Lower blade guide shown with the table
removed for clarity
Pic. 49
Side guides adjusted with ceramic just
behind the gullet
Pic. 50
8. Using the bandsaw
8.1 Adjusting the fence
Although the bandsaw is usually associated
with cutting curves, a variety of straight cuts
are easily made with the saw. In fact, it is often
used to rip wood because it is much safer than
a radial arm saw and also has a smaller saw
cut, so it wastes less wood. This becomes very
important when using expensive wood where
waste must be kept to a minimum. The cut is
safer because the force of the cut is straight
down on the table; the work cannot be pulled
back or kicked back, which sometimes happens
with table or radial arm saws. The bandsaw
can also cut very thick stock, which the radial
arm, or table saw cannot do. The disadvantage
of cutting with the bandsaw is that the surface
finish of the cut is not as good as with the
table or radial arm saw. This can be overcome
to a great degree by using the Resaw king
blade from Laguna. The blade has many of
advantages such as superior surface finish to
the cut, thin kerf (low wood waste), it can be
re-sharpened, will cut hard woods and has a
long life.
Ripping
Ripping is a cut made with the grain of the
wood. The four most common cuts made with
the grain of the wood are rip, bevel, taper
and resaw cuts. There are two frequently
used techniques for making straight bandsaw
cuts. One technique is to use a single point
to guide the work. The rationale for using a
single point is that the saw may tend to cut at
a slight angle. This is called drift or lead. The
single point allows the operator to compensate
for the drift and cut the wood straight. With
a little practice, you will obtain satisfactory
results using this method. However, you now
own a real bandsaw, so this method is not
recommended. Another method is to use the rip
fence as a guide. Once set up, this takes the
guesswork out of cutting, reduces the stress
on the operator and is a must for volume work.
Once you have mastered the setup procedure,
you will tend to use the single point method less
and less.
Side guide clamp screw
Back guide clamp screw
Back guide touching
the back of the blade
Adjusted guide
Guide locking screws