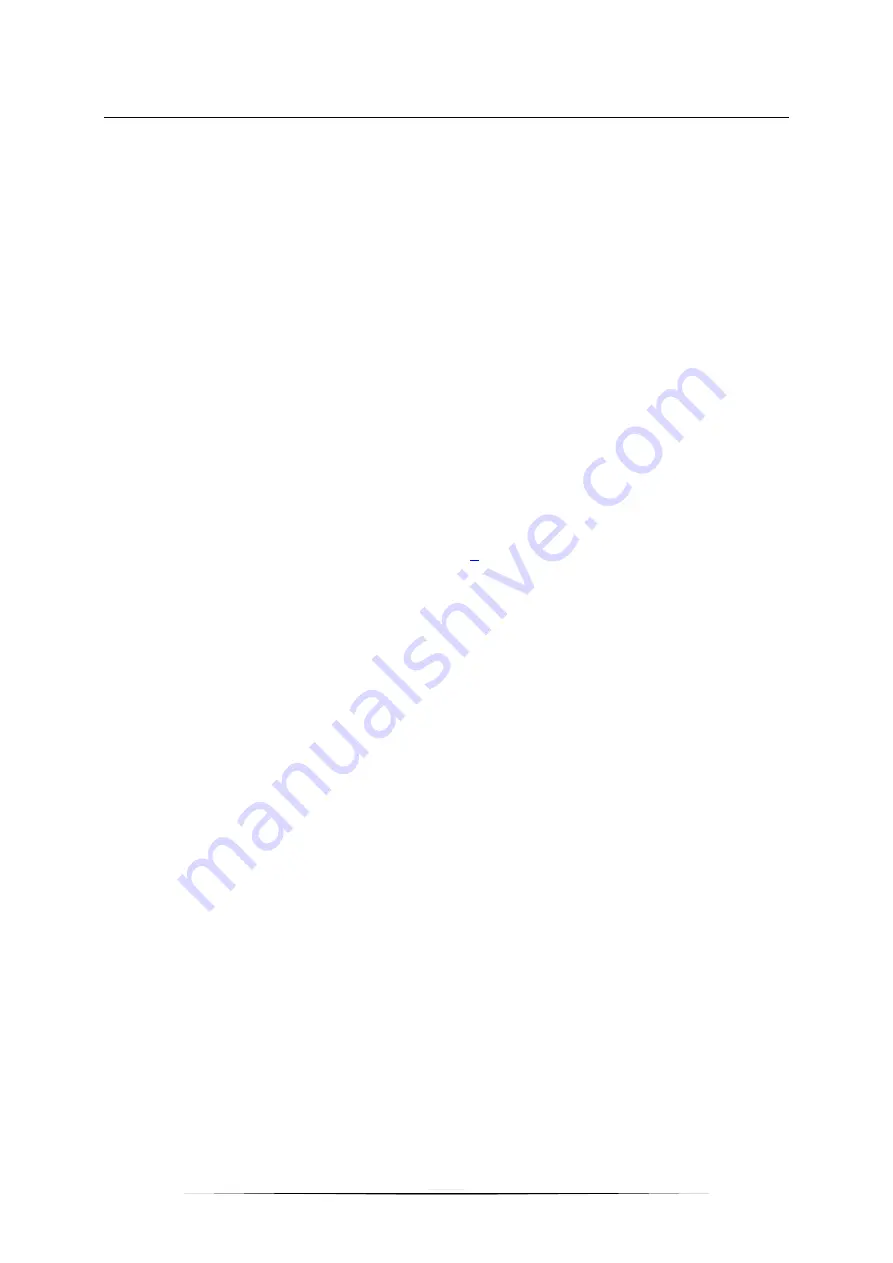
46
ifm
Programming Manual (supplement) CAN module RTC CR3020
2017-10-26
Glossary of Terms
>
PDU
PDU =
P
rotocol
D
ata
U
nit = protocol data unit.
The PDU is a term from the
→CAN protocol →SAE J1939. It refers to a component of the target
address (PDU format 1, connection-oriented) or the group extension (PDU format 2, message-
oriented).
>
PES
P
rogrammable
E
lectronic
S
ystem ...
• for control, protection or monitoring,
• dependent for its operation on one or more programmable electronic devices,
• including all elements of the system such as input and output devices.
>
PGN
PGN =
P
arameter
G
roup
N
umber
PGN = 6 zero bits + 1 bit re 1 bit data page + 8 bit PDU Format (PF) + 8 PDU Specific (PS)
The parameter group number is a term from the
→CAN protocol →SAE J1939.
>
Pictogram
Pictograms are figurative symbols which convey information by a simplified graphic representation.
(
→ chapter
What do the symbols and formats mean?
(
>
PID controller
The PID controller (proportional
–integral–derivative controller) consists of the following parts:
• P = proportional part
• I = integral part
• D = differential part (but not for the controller CR04nn, CR253n).
>
PLC configuration
Part of the CODESYS user interface.
► The programmer tells the programming system which hardware is to be programmed.
>
CODESYS loads the corresponding libraries.
>
Reading and writing the periphery states (inputs/outputs) is possible.
>
Pre-Op
Pre-Op = PRE-OPERATIONAL mode.
Operating status of a CANopen participant. After application of the supply voltage each participant
automatically passes into this state. In the CANopen network only
→SDOs and →NMT commands
can be transferred in this mode but no process data.
>
Process image
Process image is the status of the inputs and outputs the PLC operates with within one
→cycle.
At the beginning of the cycle the PLC reads the conditions of all inputs into the process image.
During the cycle the PLC cannot detect changes to the inputs.
During the cycle the outputs are only changed virtually (in the process image).
At the end of the cycle the PLC writes the virtual output states to the real outputs.