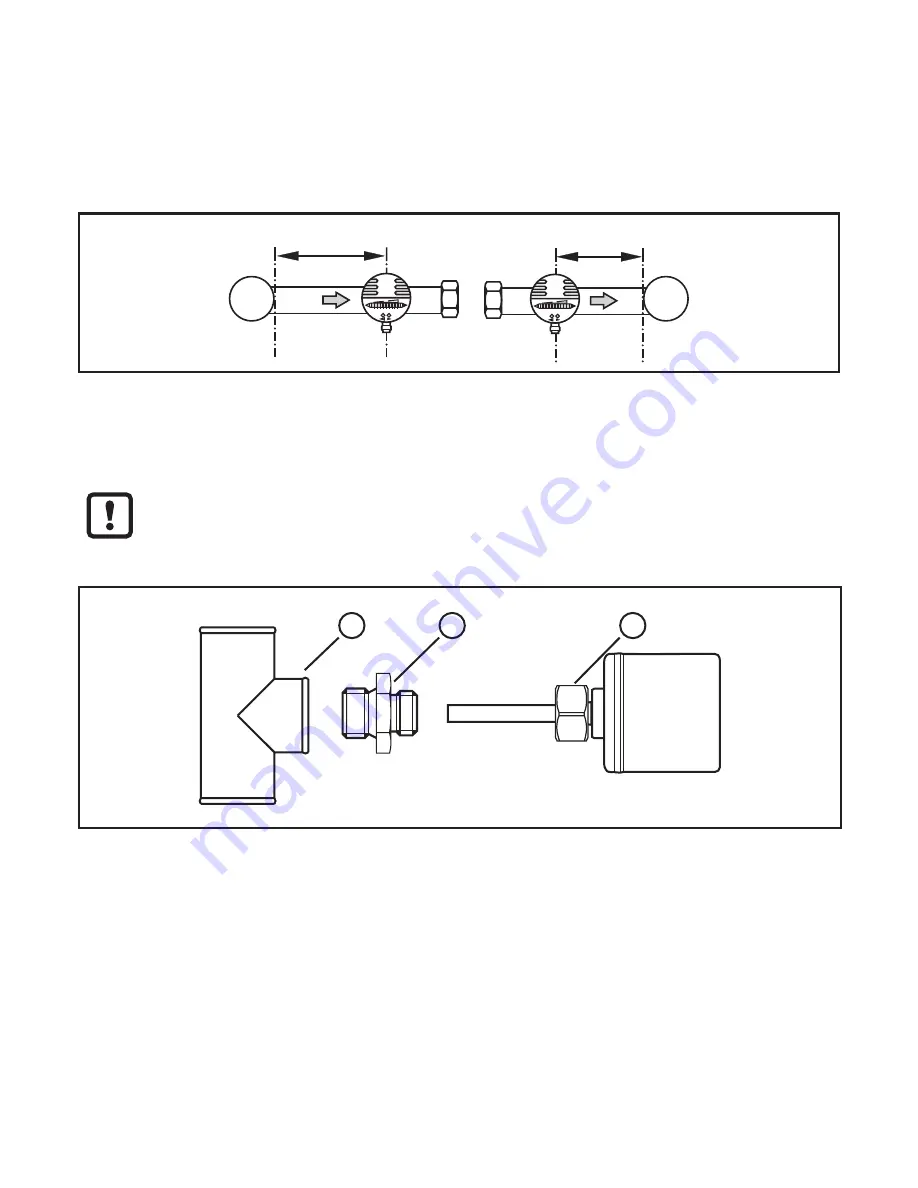
6
4.2 Sources of interference in the pipe system
Components integrated in the pipes, bends, valves, reductions, etc� lead to turbu-
lence of the medium� This affects the function of the unit�
Recommendation: Adhere to the distances between sensor and sources of inter-
ference:
D = pipe diameter; S = sources of interference
4.3 Mounting operation
►
Ensure that the system is free of pressure during installation�
►
Ensure that no media can leak at the mounting location during installa-
tion�
►
Grease the threads of the process connection (1), adapter (2) and nut (3)�
Note: The sensor tip (A) must not be in contact with grease�
►
Screw the suitable adapter into the process connection�
►
Place the flow monitor onto the adapter and tighten the nut� Tightening torque
25 Nm� Ensure that the unit is correctly oriented�