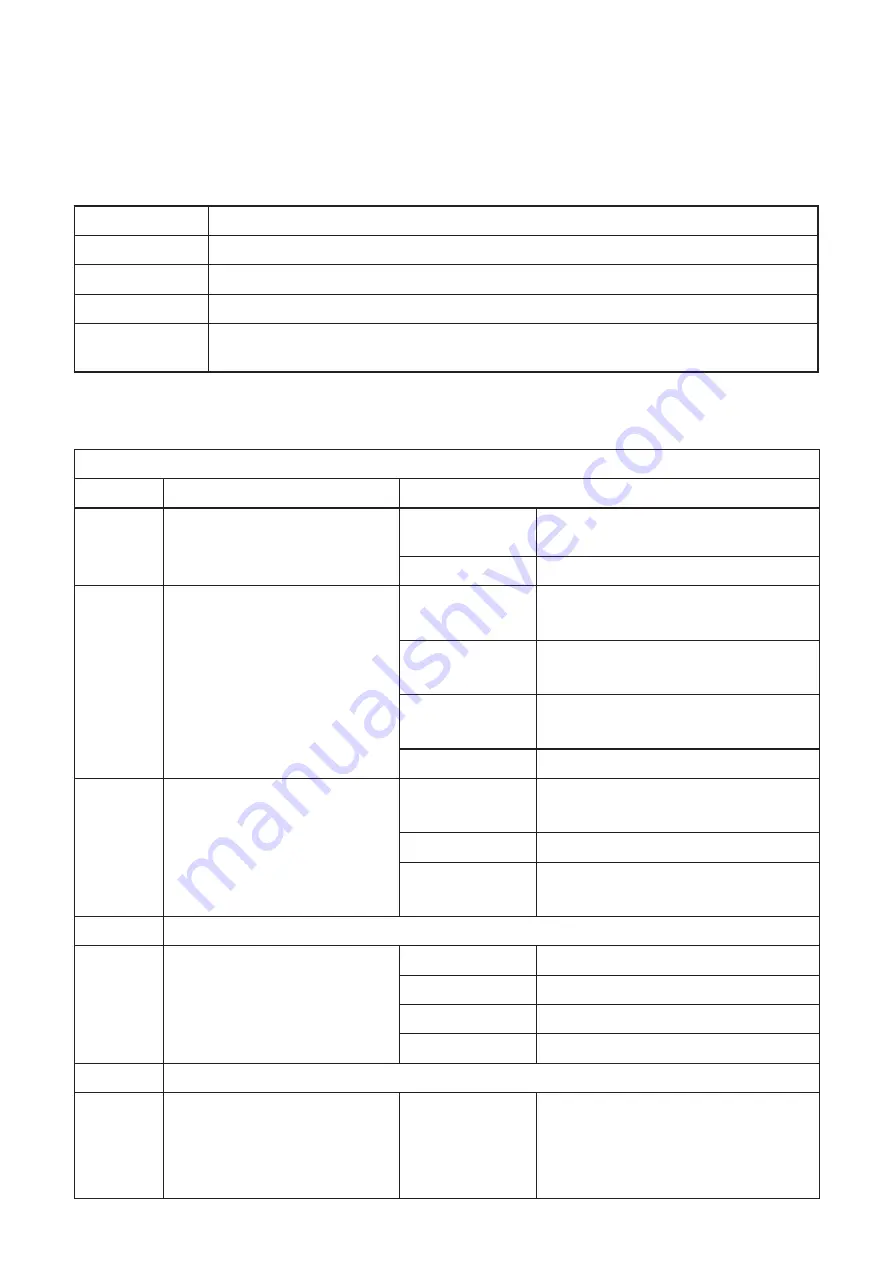
IO-Link master
34
18.3 Parameter telegram
This section provides a detailed description of the format of the device parameters�
This may be useful when setting parameters using acyclic services or if there is no
user interface for the simple selection of parameters�
Byte
Meaning
1 … 7
DP standard
8 … 10
DP/V1 standard
11 ��� 28
Module parameter of the status/control module
29 … 237
Module parameters of the IO-Link ports
The set-up depends on the type and sequence of the submodules inserted�
Module parameter
Module parameter "status/control"
Byte
Meaning
Contents
11
Port synchronisation
Bit 0
Free (ongoing)
0 = deactivated; 1 = activated
Other
Reserved
12
General diagnostic settings
Bit 0
Channel-related diagnostics
0 = deactivated 1 = activated
Bit 1
Status messages
0 = deactivated 1 = activated
Bit 2
IO-Link master status diagnostics
0 = deactivated 1 = activated
Other
Reserved
13
Port specific diagnostic settings
Bit 0
IO-Link device diagnostics port 1
0 = deactivated 1 = activated
���
���
Bit 7
IO-Link device diagnostics port 8
0 = deactivated 1 = activated
14
Reserved
15
Substitute value behaviour for
the IO-Link ports in DO mode
(pin 4)
00
hex
Clear all
01
hex
Set all
02
hex
Hold last value
03
hex
Switch replacement value
16���17
Reserved
18
Specification of a replacement
value sample for the
IO-Link ports in the DO
operating mode (pin 4)
00
hex
���FF
hex
In order to use this parameter, the
value "Replacement values" must be
set beforehand in the "Behavior in
the event of error for status/control
module" parameter�
Содержание Ecomat 300 AL1010
Страница 1: ...Device manual IO Link Profibus master AL1010 7391036 00 10 2016 UK ...
Страница 48: ...IO Link master 48 ...
Страница 50: ...IO Link master 50 ...