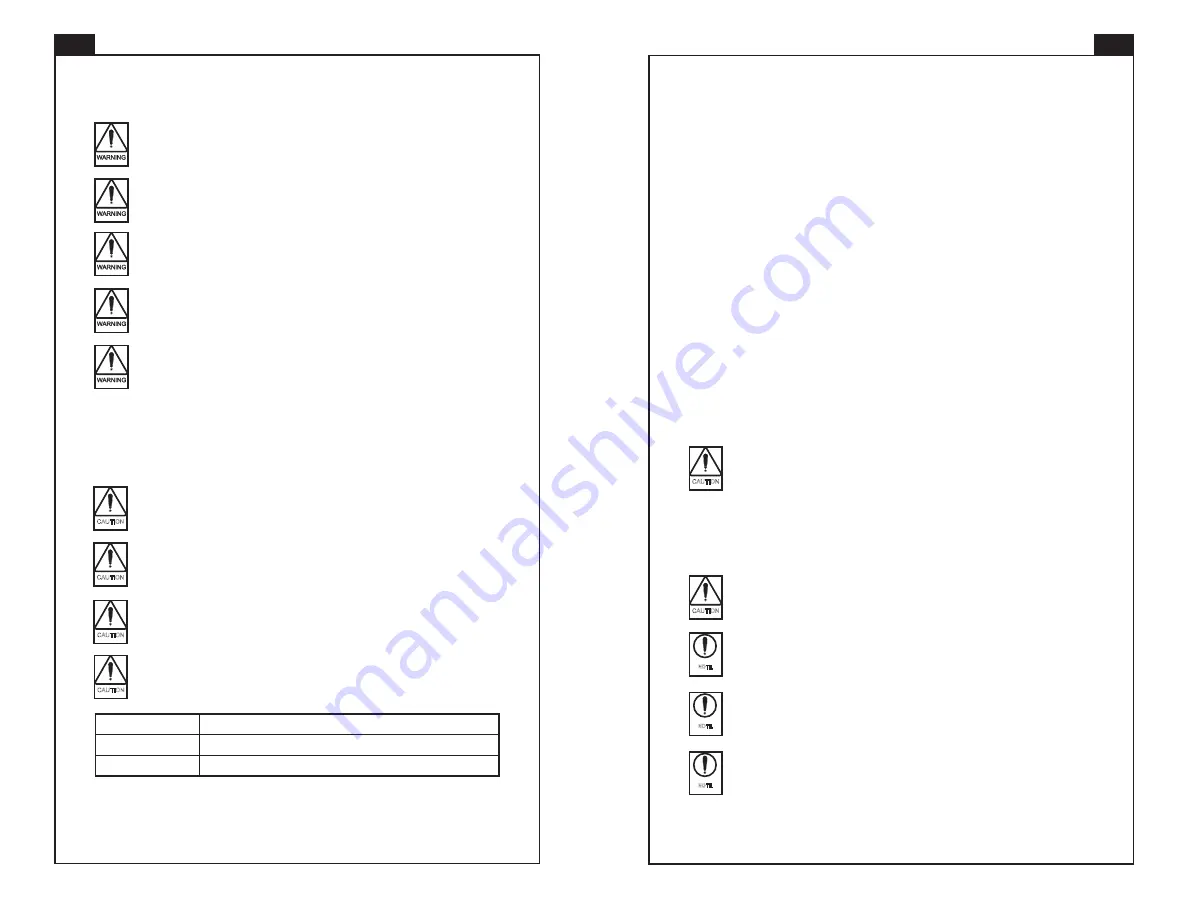
10
DOC No: 8540 REV E
11
DOC No: 8540 REV E
Pumping
fl
ammable
fl
uids without a proper earthing connection may
cause spontaneous ignition.
EagleDrive Electrical Connection
Ensure that the pump motor is earthed. The pump may be electrically
isolated from the motor depending on the mounting con
fi
guration. Some
installations may need an earthing connection on the pump head.
Before starting any electrical installation work ensure that the main
electrical supply is adequately isolated.
Electrical installation must be carried out by quali
fi
ed personnel who are
conversant with local electricity installation regulations.
Ensure that the voltage of the supply is correct for the motor being
connected, and that the source is Class 2 or a Limited Power Source.
CAUTION
Ensure that all electrical connections use a common earth ground to
avoid hazardous ground loops.
Ensure that only power supplies having SELV speci
fi
cation are
connected to the EagleDrive.
CAUTION
Ensure that all associated equipment has a form of overcurrent
protection. If a fuse is used see table below for recommendations.
CAUTION
EagleDrive Electrical Connection (Continued)
Control Signal In
0 to 5 VDC speed control, when the lead is connected to a supply within the range the
motor speed is proportional to the input. The applied voltage must be within -0.3 to +5.1
VDC or the motor will be irreparably damaged.
PWM (Pulse Width Modulation) Speed Control
When duty cycle is within 3% to 97% at 20-100Hz frequency, the motor speed is
proportional to the input. The applied voltage must be within -0.3 to 1.5v (Lo) and +3.5
to 5.1V (Hi) or the motor will be irreparably damaged.
Common Ground
The input voltage, the 0 to 5 VDC control input, and the tachometer output all use a
common ground. It is possible that ground potential differences between the power
supply, control voltage source and the frequency counter (if used) will be forced to the
same ground reference when connected to the EagleDrive. Ensure only one earth
ground is used to avoid ground loops.
Using The Tachometer Output
The tachometer output can be monitored using a frequency counter. The tachometer
output is 0-5V square wave pulse that occurs twice per pump drive revolution. To convert
the tachometer output to rpm, multiply the output frequency (Hz) by 30.
Inadvertent connection of the tachometer output (green) wire to ground
or the supply voltage can cause damage to the drive. If the tachometer is
not used, trim and insulate the green lead.
CAUTION
DO NOT reverse the direction of rotation of the drive until the drive has
come to a complete stop. Reversing the direction while the drive is still
turning may damage the motor.
CAUTION
NOTE
NOTE
NOTE
Inadvertent grounding of the forward/reverse (orange) wire will cause the drive
to operate in reverse. If reverse operation is not required, trim and insulate the
orange lead.
Motor/Pump performance will be different between FWD and REV operating
modes.
0-5V control signal is assumed by the EagleDrive. If PWM signal edges are
detected (Lo
≤
1.5V - Hi
≥
3.5V) then PWM is assumed and 0-5V input is
disregarded. If 0-5V control is desired, connect PWM input (Pin 6 - Violet) to
ground to prevent noise from interferring with 0-5V control.
Forward/Reverse Operation
The direction of
fl
uid
fl
ow can be changed by connecting the orange wire to ground.
For FORWARD
fl
ow, make NO CONNECTION to the orange wire. For REVERSE
fl
ow,
connect the orange wire to GROUND.
Power In
The main input power is 12 to 36 VDC from a Class 2 (SELV) source applied across the
power in and common ground leads. This voltage must be maintained within the speci
fi
ed
limits as the motor is loaded to its maximum current of 2A (Model - DEMSE) or 3A
(Model - DEELE.)
Ensure that the power supply voltage ripple is maintained below 5% peak
to peak.
CAUTION
E
AGLE
D
RIVE
M
ODEL
R
ECOMMENDED
FUSE
DEMSE
L
ITTLEFUSE
0313002 HXP
DEELE
L
ITTLEFUSE
0313003 HXP