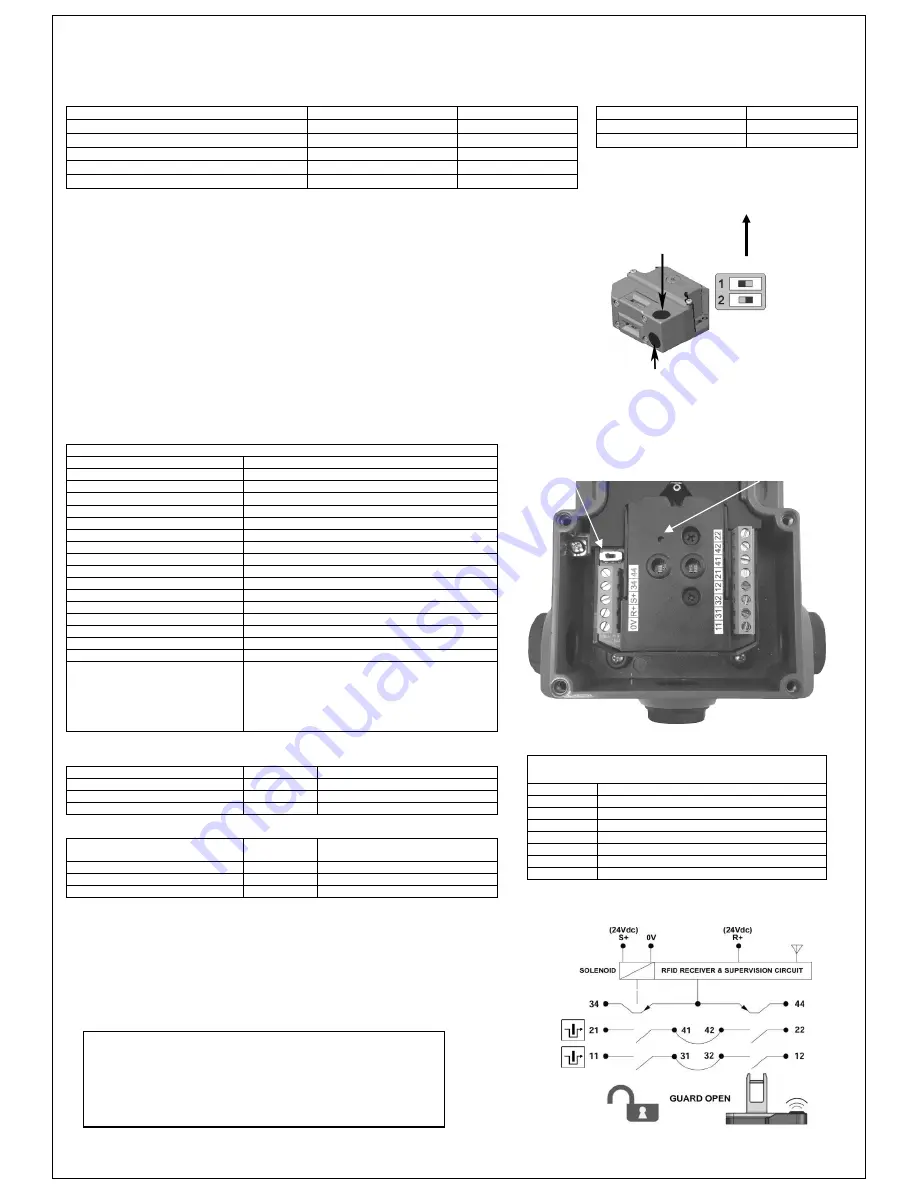
Gate Box with Safety Interlocking & RFID
LED DIAGNOSTICS (Interlock switch)
Switch State
LED 1 (Green/Yellow)
Comment
Solenoid State
LED 2 (Red)
Guard Open
Off
Energised
ON
Guard Locked
Steady Green
Safety outputs ON
De-energised
OFF
Guard Unlocked
Flashing Green
Guard Misalligned / Wrong Actuator
Alternate Flashing Green/Yellow
Fault
Steady Yellow
See reset procedure
SPECIAL INSTRUCTION: RFID actuator – RESET.
In the event that a Fault condition requires reset, follow the reset instructions:
1)
Turn off all power to the switch and open the guard.
2)
Remove the switch cover.
3)
Using a 2mm terminal screwdriver hold down the RESET button inside the switch housing and turn on the switch
power (see Fig.2).
4)
Release the RESET button, the yellow LED will flash, close the guard and the yellow LED will turn steady yellow.
(If yellow LED continues to flash check for mechanical fault (e.g. damaged actuator or switch head)).
5)
Turn power off and then on, the green LED will illuminate.
6)
Re-fit the switch cover.
7)
Open and close the guard ensuring all safety functions are correct –refer to any risk assessment for the particular
guard application.
Slide Switch Position 2:
FRONT Entry
Slide Switch Position 1:
END Entry
Technical Data: Standards IEC60947-5-1 ISO14119 ISO13849-1 IEC62061 UL508
Entry Selector Switch
Select Front or End sensing. (See
Fig 1)
RESET button
(If required press and hold using a 2mm
terminal screw driver)
Supply Voltage
24Vdc (+/- 10%)
Power Consumption
R+ 1.2W (50mA Max.)
S+ 12W (500mA Max.)
Safety Circuits (11-31 & 21-41)
240V 3A. A300 Pilot Duty Fuse externally 10A.(FF)
Safety Circuits (32-12 & 42-22)
24V 2.5A (RFID Coding)
Auxiliary Circuits (34 & 44)
24Vdc 0.2A Max.
Rated Insulation Voltage
500VAC
Rated Impulse withstand
1000VAC
Holding Force
F1Max 4000N Fzh 3076N
Operating Frequency
1Hz
Actuator entry minimum radius
175mm
Body Material
Stainless Steel 316
Head Material
Stainless Steel 316
Mechanical Actuator Material
Stainless Steel 316
Enclosure Protection
IP66
Operating Temperature
-25°C to +40°C
Mechanical Life Expectancy (B10d)
2.5 x 10
6
cycles at 100mA load
Vibration
IEC68-2-6, 10-55Hz+1Hz Excursion: 0.35mm, 1 octave/min
Fig. 2. Cover Removed
Characteristic data according to IEC62021 (used as a subsystem)
Interlock Switch Circuit – Terminal connections.
(Use 16-28AWG copper conductors. Terminal Torque 6 lb ins. (0.7Nm)).
0V
Supply 0V.dc
R+ 24V.dc
Supply 24V.dc
S+ 24V.dc
Unlock signal (solenoid) apply +24V.dc
11/12
Safety interlock and lock monitoring circuit
21/22
Safety interlock and lock monitoring circuit
44
Guard open signal +24V.dc out
34
Unlocked signal +24V.dc out
12
Earth bonding connection
Safety Integrity Level
SIL 3
PFH (1/h)
4.77E-10
Corresponds to 4.8% of SIL3
PFD
4.18E-05
Corresponds to 4.2% of SIL3
Proof Test Interval T
1
20a
Characteristic data according to EN ISO13849-1
Performance Level
e
If both channels are used in conjunction with
a SIL3/PLe control device.
Category
Cat 4.
MTTF
d
1100a
Diagnostic Coverage DC
99% (High)
Number of operating days per year:
d
op
= 365d
Number of operating hours per day:
h
op
= 24h
When the product is usage differs from these assumptions (different load, operating frequency, etc.) the values
have to be adjusted accordingly
END
FRONT
Head of the switch
this way.
Fig. 1. Entry Selector Switch
Information with regard to UL 508: Type 1 enclosure.
Maximum temperature 40°C.
Use 16-28AWG copper conductors (rated 90°C). Terminal Torque 6 lb ins. (0.7Nm).
Intended for same polarity use.
A300 Pilot Duty. 240V. 3A. PF 0.38 or greater tested for 6,000 cycles endurance.
Use one polymeric conduit connection. Not suitable for connection to rigid metal conduit.
(Earth bonding terminal inside enclosure if required – use 16-12AWG conductors).
Interlock Schematic - (internal wire links not removed).
Note: Circuits 21/41 and 11/31 are lock monitoring contacts. (Closed when switch is locked).
Circuits 42/22 and 32/12 are interlock monitoring circuits (Closed when guard is closed).
Specification: