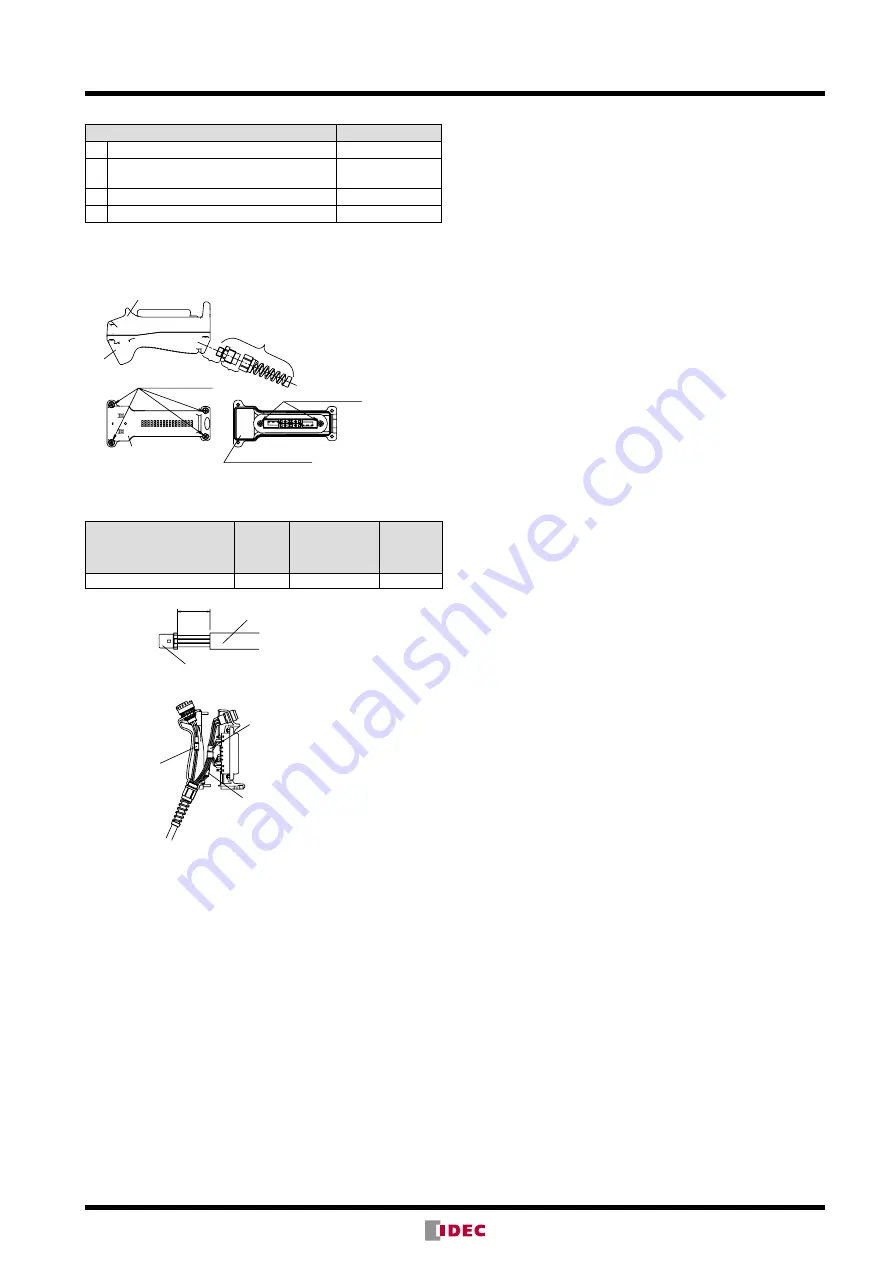
29
Three-position Enabling Switches/Grip Style Three-position Enabling Switches
Recommended Tightening Torque
Parts for tightening
Torque
A Base and rubber kit (M4 screw × 4)
1.1 to 1.3 N·m
B Cable gland and grip style enabling
switch
2.7 to 3.3 N·m
C Cable gland
2.7 to 3.3 N·m
D HE2B Enabling Switch (M3 screws × 2)
*
0.5 to 0.8 N·m
Note: The recommended tightening torques of B and C are for
the supplied cable gland. When using another cable gland,
refer to the tightening torque of the cable gland used.
*
For replacing HE2B enabling switch or rubber boot only
Rubber Boot Kit
Cable Gland
Base
Base
B
C
D (M3 scew × 2)
A (M4 scew × 4)
Rubber Boot Kit
HE2G (internal connector)
Wire Length inside the Switch
Grip
Style
Enabling
Switch
Momentary
Pushbutton/Key
Selector Switch
Emergency
Stop
Switch
Wire stripping length L1 (mm)
20
60
75
Cable gland for
emergency stop switch
Cable gland for
momentary pushbutton/
key selecetor switch
Cable gland for
grip style enabling switch
L1
Sheath
<Example>
Applicable cable gland
on cable side
• Applicable wire size for the cable gland on cable side
• 0.05 to 0.86mm
2
(AWG18 to 30): Check the compliance with
receptacle and contact.
Tool: 1762846-1 (manual tool)
Note: When using stranded sires, make sure that loose wires do
not cause short circuit. Also, do not older the terminals
to prevent loose wires. Use copper wire of 60°C or 75°C
temperature rating in order to comply with UL508. Observe
the requirements of GS-ET-22: 2003, 4.2.6 for wiring.
Operating Instructions
HE2B/HE3B/HE5B/HE6B/HE1G/HE1G-L/HE2G
• To achieve a high level of safety, connect the two contacts of the
3-position switch to a disparity detection circuit (e.g., safety relay
module) (ISO 13849-1, EN 954-1).
• Because two contacts are designed to operate independently,
pressing the edge of a button turns on one contact earlier than
the other contact, causing a delay in operation. To avoid this,
always press the center of the button.
HE1B/HE2B/HE3B/HE5B/HE6B/HE1G/HE1G-L/HE2G
• 3-position enabling switches output ON signals in position 2.
Sys tems must be designed to enable machine operation when
the 3-position enabling switch is in position 2 only.
• Perform a risk assessment in actual applications as strong force
may be applied to the switch when depressed to position 3.
• Perform a risk assessment for the shape and structure of the
part where the enabling switch is installed, to prevent unintended
operation of the enabling switch. For example, an enabling
switch protruding from the teach pendant may result in an unin-
tended operation of the enabling switch.
• Strong force may be applied to a 3-position enabling switch
when pressed to position 3. Provide sufficient strength to the
part where 3-position enabling switches will be installed.