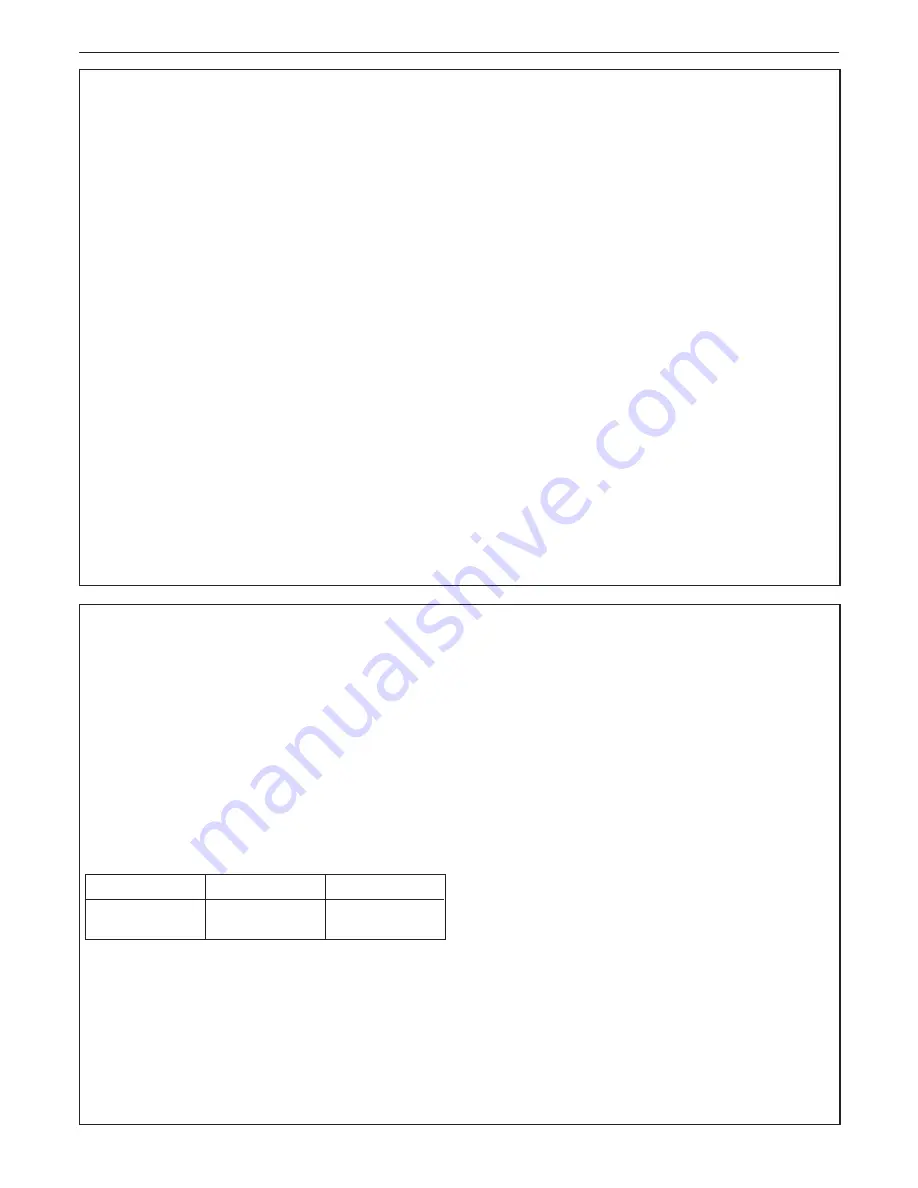
11
Vanguard L -
Installation & Servicing
GENERAL
7 SEALED (PRESSuRISED) SySTEm
Working pressure 6 bar maximum.
Particular reference should be made to BS 6644: Section 6 and
Guidance note PM5 "automatically controlled steam and hot
water boilers" published by the Health and Safety Executive.
The information and guidance given below is not intended to
override any requirements of either of the above publications
or the requirements of the local authority, gas or water
undertakings.
In general commercial closed pressurised systems are
provided with either manual or automatic water make up.
In both instances it will be necessary to fit automatic controls
intended to protect the boiler, circulating system and ancillary
equipment by shutting down the boiler plant if a potentially
hazardous situation should arise.
Examples of such situations are low water level and operating
pressure or excessive pressure within the system.
Depending on circumstances, controls will need to be either
manual or automatic reset.
In the event of a shutdown both visual and audible alarms may
be necessary.
Expansion vessels used must comply with BS. 4814 and must
be sized on the basis of the total system volume and initial
charge pressure.
Initial minimum charge pressure should not be less than 0.5
bar (7.2 psi) and must take account of the static head and
specification of the pressurising equipment. The maximum water
temperatures permissible at the point of minimum pressure in the
system are specified in Guidance Note PM5.
When make up water is not provided automatically it will be
necessary to fit controls which shut down the plant in the event of
the maximum system pressure approaching to within 0.5 bar (5
psi) of the safety valve setting.
Other British Standards applicable to commercial sealed systems
are:
BS6880: Part 2
BS 1212
BS 6281: Part 1
BS 6282: Part 1
BS 6283: Part 4
8 VENTILATIoN
Safe, efficient and trouble-free operation of conventionally
flued gas boilers is vitally dependent on the provision of an
adequate supply of fresh air to the room in which the appliance
is installed.
Ventilation by grilles communicating directly with the outside
air is required at both high and low levels. The minimum free
areas of these grilles must be according to the following scale
in Table 4.
Table 4 - Ventilation Requirements
Required area (cm
2
) per kW of total rated input (net)
Boiler Room
Enclosure
Low level (inlet)
4
10
High level (outlet)
2
5
Note.
Where a boiler installation is to operate in summer months
(e.g. DHW) additional ventilation requirements are stated, if
operating for more than 50% of time. (Refer to BS 6644)
Position ventilation grilles to avoid the risk of accidental
obstruction by blockage or flooding. If further guidance on
ventilation is required then consult BS 6644.
The supply of air by mechanical means to a space housing the
boiler should be by mechanical inlet with natural or mechanical
extraction. Mechanical extract ventilation with natural inlet must
not be used.
Where a mechanical inlet and a mechanical extract system is
applied, the design ventilation flow rates should be as in BS 6644.
Note.
For mechanical ventilation systems an automatic control should
be provided to cause safety shutdown or lockout of the boiler(s) in
the event of failure of air flow in either inlet or extract fans.
ImPoRTANT.
The use of an extractor fan in the same room as
the boiler (or in an adjacent communicating room) can, in certain
conditions, adversely affect the safe operation of the boiler.
Where such a fan is already fitted (or if it is intended to fit an
extractor fan after installation of the appliance) the advice of the
gas supplier should be obtained.