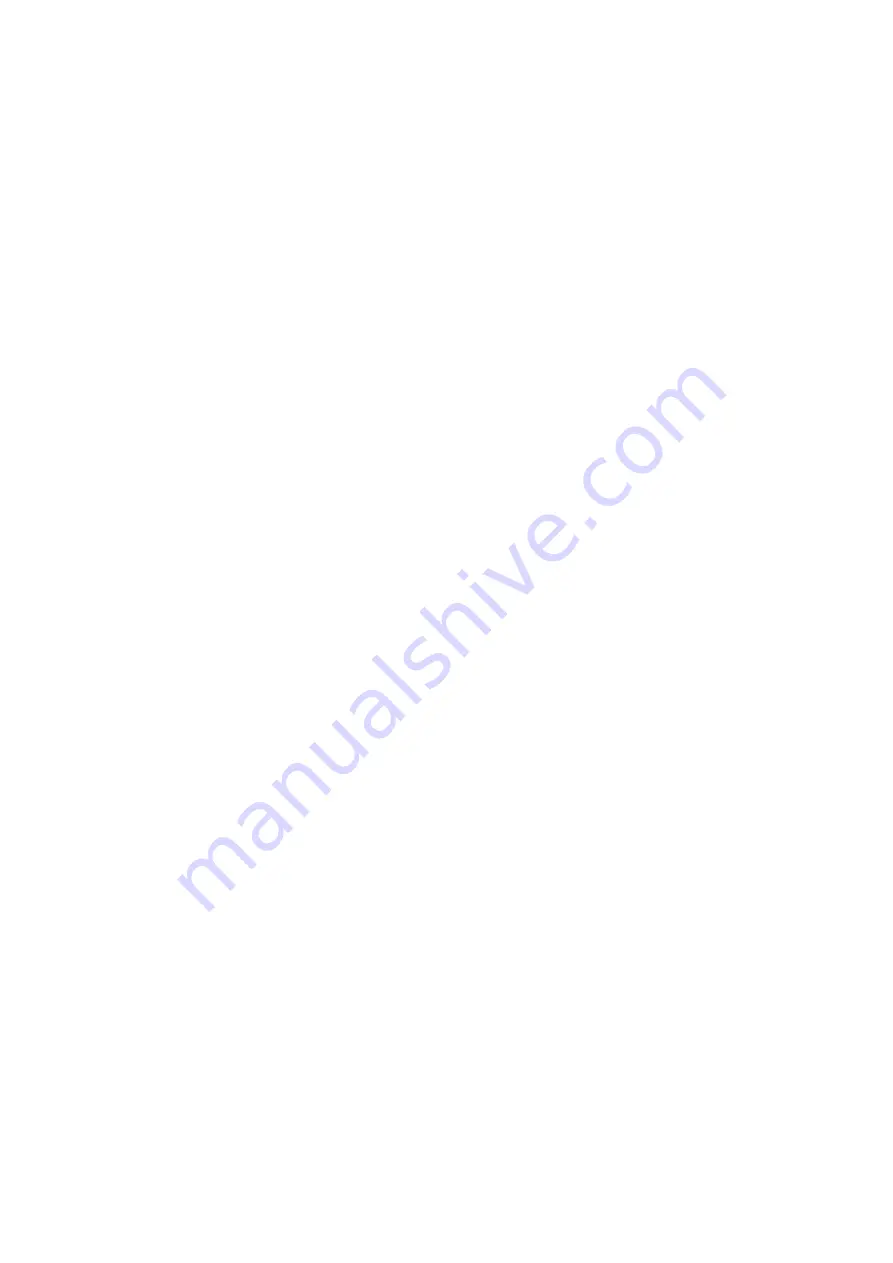
4.
Preparing the device to work
-
Before use please make sure that electric network you are going to use is corresponding to
technical specification of the device. Power supply voltage and frequency is provided in the
technical specification section of this manual.
-
Please check if the power supply connection is grounded. Check if the fuse is sufficient and
not less than 20A.
-
In case of changing the plug follow the instructions to connect the green/yellow wire to the
ground line in your socket.
5. Connecting welding cables and torch
-
Before connecting welding cables make sure the device in not connected to power supply.
-
Check if the ground cable is connected with ground clamp
-
Ground plug should be connected to negative polarization socket (pic. 3.1.9). Insert plug and
turn it to tighten. Loosely connected plug may cause sparks and damage to socket.
In MIG/MAG process ground plug should be connected to negative socket ( - ) however when
using flux core wire it is connected to positive socket ( + ). The other empty socket must
connected with polarization selector (pic. 3.1.10)
Please remember that you
can’t leave empty sockets as the circuit won’t be closed
and welding won’t be possible.
-
Make sure the contact tip and torch liner are compatible with the wire you are about to use.
In the set there is torch compatible with 0.8mm steel wire. For a different wire diameter or
type you will need to supply compatible parts.
6. Mounting wire spool into the feeder
-
Please make sure that all the rollers installed in the drive assembly are corresponding to
the type and diameter of the wire. Factory installed rollers are intended for steel wire from
0.6 to 0.8mm. For steel wires use V-shaped groove rollers
-
Place wire spool on the spool mount, taking care to ensure that the wire unwinding
direction was in line with the direction of the wire entering the drive unit.
-
Lock the reel by tightening the plastic nut.
-
Release roll locking mechanism on wire feeder to allow wire to enter the feeder.
-
Insert the end of the wire into the guide located in the back of the feeder and carry it out
over the drive rollers into the welding torch. Make sure the wire is straight and has no
imperfections that may cause it to jam inside torch liner.
-
By adjusting pressure on the locking mechanism you can either tighten or loosen wire
against roller grooves. It allows you to correct wire feeding if irregular feed occurs.
-
Prepare torch before inserting welding wire. Torch cable must be put in straight line to
allow the wire to smoothly go through the liner. Remove the gas nozzle the contact tip to
allow the wire to exit the torch.
-
By pressing a red button inside spool compartment activate wire feeder to insert the
welding wire until it leaves tip of the welding torch.
-
Attach appropriate contact tip corresponding to wire diameter. Put the gas nozzle back on
and remove excessive wire.