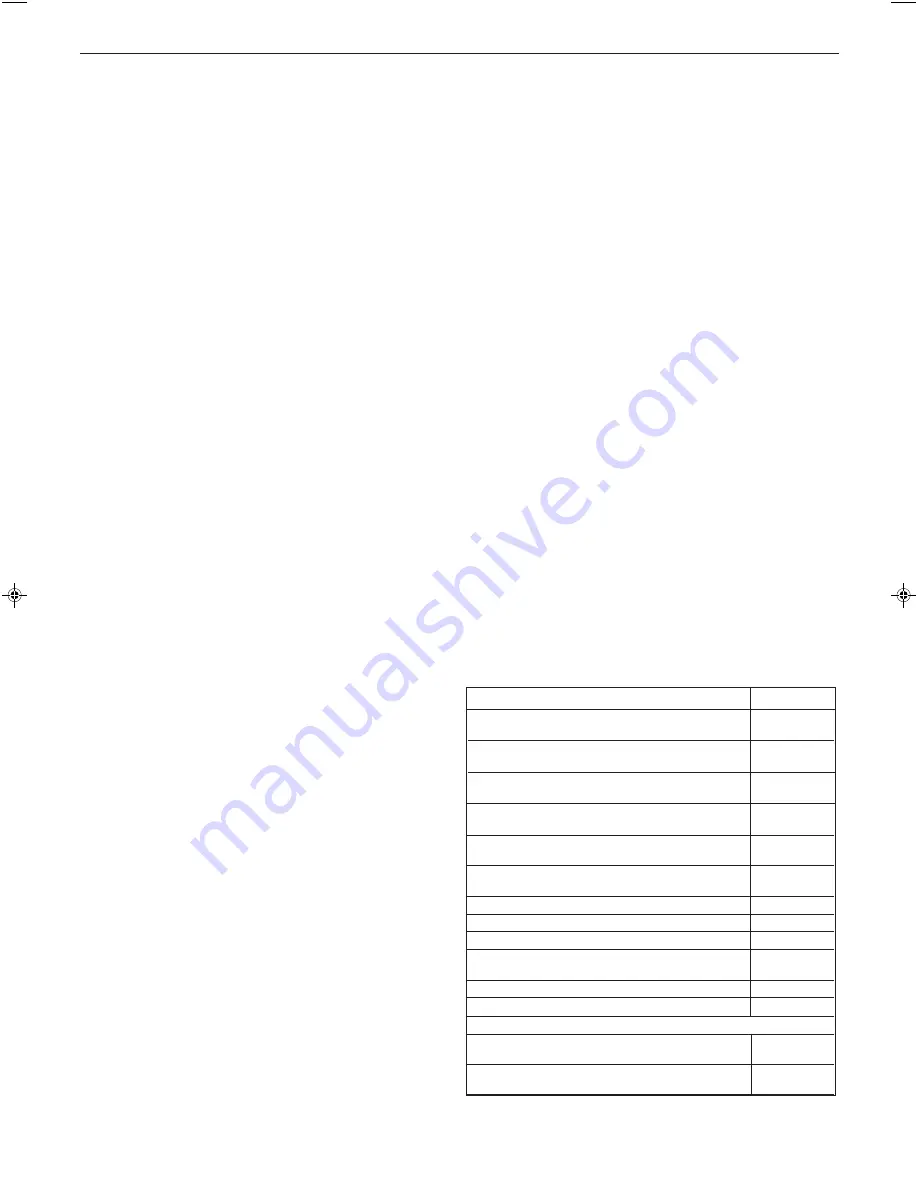
8
icos
-
Installation & Servicing
GENERAL
SAFE HANDLING OF SUBSTANCES
Care should be taken when handling the boiler insulation
panels, which can cause irritation to the skin. No asbestos,
mercury or CFCs are included in any part of the boiler or its
manufacture.
LOCATION OF BOILER
The boiler must be installed on a flat and vertical wall, capable
of adequately supporting the weight of the boiler and any
ancillary equipment.
The boiler may be fitted on a combustible wall and insulation
between the wall and the boiler is not necessary, unless
required by the local authority.
For electrical safety reasons there must be no access from the
back of the boiler.
The boiler must not be fitted outside.
Timber Framed Buildings
If the boiler is to be fitted in a timber framed building it should
be fitted in accordance with the Institute of Gas Engineering
document IGE/UP/7:1998.
Bathroom Installations
This appliance is rated
IP20.
The boiler may be installed in any room or internal space,
although particular attention is drawn to the requirements of the
current IEE (BS.7671) Wiring Regulations and, in Scotland, the
electrical provisions of the building regulations applicable in
Scotland, with respect to the installation of the boiler in a room
or internal space containing a bath or shower. For Ireland
reference should be made to the current ETCI rules for
electrical installations and I.S.813:2002.
If the appliance is to be installed in a room containing a bath or
shower then, providing water jets are not going to be used for
cleaning purposes (as in communal baths/showers), the
appliance must be installed in Zone 2, as detailed in BS.7671.
Compartment Installations
A compartment used to enclose the boiler should be designed
and constructed specially for this purpose.
An existing cupboard or compartment may be used, provided
that it is modified for the purpose.
In both cases details of essential features of cupboard /
compartment design, including airing cupboard installation,
are to conform to the following:
z
BS. 6798. (No cupboard ventilation is required - see “Air
Supply” for details).
z
The position selected for installation MUST allow adequate
space for servicing in front of the boiler.
z
For the minimum clearances required for safety and
subsequent service see the wall mounting template and
Frame 2. In addition, sufficient space may be required to
allow lifting access to the wall mounting plate.
GAS SUPPLY
The local gas supplier should be consulted, at the installation
planning stage, in order to establish the availability of an
adequate supply of gas. An existing service pipe must NOT be
used without prior consultation with the local gas supplier.
The boiler MUST be installed on a gas supply with a governed
meter only.
A gas meter can only be connected by the local gas supplier or
by a Gas Safe Registered Engineer. In IE by a Registered Gas
Installer (RGII).
An existing meter should be checked, preferably by the gas
supplier, to ensure that the meter is adequate to deal with the
rate of gas supply required.
It is the responsibility of the Gas Installer to size the gas
installation pipework in accordance with BS6891:2005. Whilst
the principle of the 1:1 gas valve ensures the icos HE range is
able to deliver it’s full output at inlet pressures as low as 14mb,
other gas appliances in the property may not be as tolerant.
When operating pressures are found to be below the minimum
meter outlet of 19mb these should be checked to ensure this is
adequate for correct and safe operation.
Allowing for the acceptable pressure loss of 1mb across the
installation pipework, it can be assumed that a minimum
permitted operating pressure of 18mb will be delivered to the
inlet of the appliance. (Reference BS 6400-1 Clause 6.2
Pressure Absorption).
The integral appliance isolation valve and boiler pipework could
further reduce the operating pressure by up to 1.5mb when
measured at the inlet test point on the appliance gas valve.
Therefore it has been identified that an operating pressure as
low as 16.5mbar could be measured at the appliance inlet
pressure test point on the gas valve.
IMPORTANT.
Installation pipes MUST be fitted in accordance with BS. 6891.
In IE refer to I.S.813:2002. Pipework from the meter to the boiler
MUST be of an adequate size.
The complete installation MUST be tested for gas tightness and
purged as described in the above code.
FLUE INSTALLATION
Pluming will occur at the terminal so terminal positions which
would cause a nuisance should be avoided.
The flue must be installed in accordance with the
recommendations of BS.5440-1:2000. In IE refer to I.S.813:2002.
The following notes are intended for general guidance.
1.
The boiler MUST be installed so that the terminal is exposed
to external air.
2.
It is important that the position of the terminal allows the free
passage of air across it at all times.
Flue Terminal Positions
Min. Spacing*
1.
Directly below, above or alongside an opening
window, air vent or other ventilation opening.
300mm (12")
2.
Below guttering, drain pipes or soil pipes.
25mm ( 1")*
BS5440-1 2000
75mm (3")
3.
Below eaves.
25mm (1")*
BS5440-1 2000
200mm (8")
4.
Below balconies or a car port roof.
25mm (1")*
BS5440-1 2000
200mm (8")
5.
From vertical drain pipes or soil pipes.
25mm (1")*
BS5440-1 2000
150mm (6")
6.
From an internal or external corner or to a
25mm (1")*
boundary along side the terminal.
BS5440-1 2000
300mm (12")
7.
Above adjacent ground, roof or balcony level.
300mm (12")
8.
From a surface or a boundary facing the terminal.
600mm (24")
9.
From a terminal facing a terminal.
1,200mm (48")
10.
From an opening in a car port
(e.g. door or window) into dwelling.
1,200mm (48")
11.
Vertically from a terminal on the same wall.
1,500mm (60")
12.
Horizontally from a terminal on the wall.
300mm (12")
Vertical Terminals
13.
Above the roof pitch with roof slope of all angles. 300mm (12")
Above flat roof.
300mm (12")
14.
From a single wall face.
300mm (12")
From corner walls.
300mm (12")
Table 3 - Balanced Flue Terminal Position
* Only one reduction down to 25mm is allowable per installation
otherwise BS5440-1 2000 dimensions must be followed.
Содержание HE12
Страница 2: ...2 icos Installation Servicing...
Страница 54: ...54 icos Installation Servicing NOTES...
Страница 55: ...55 icos Installation Servicing NOTES...
Страница 56: ......
Страница 58: ...Gas Safe Register ID Number...