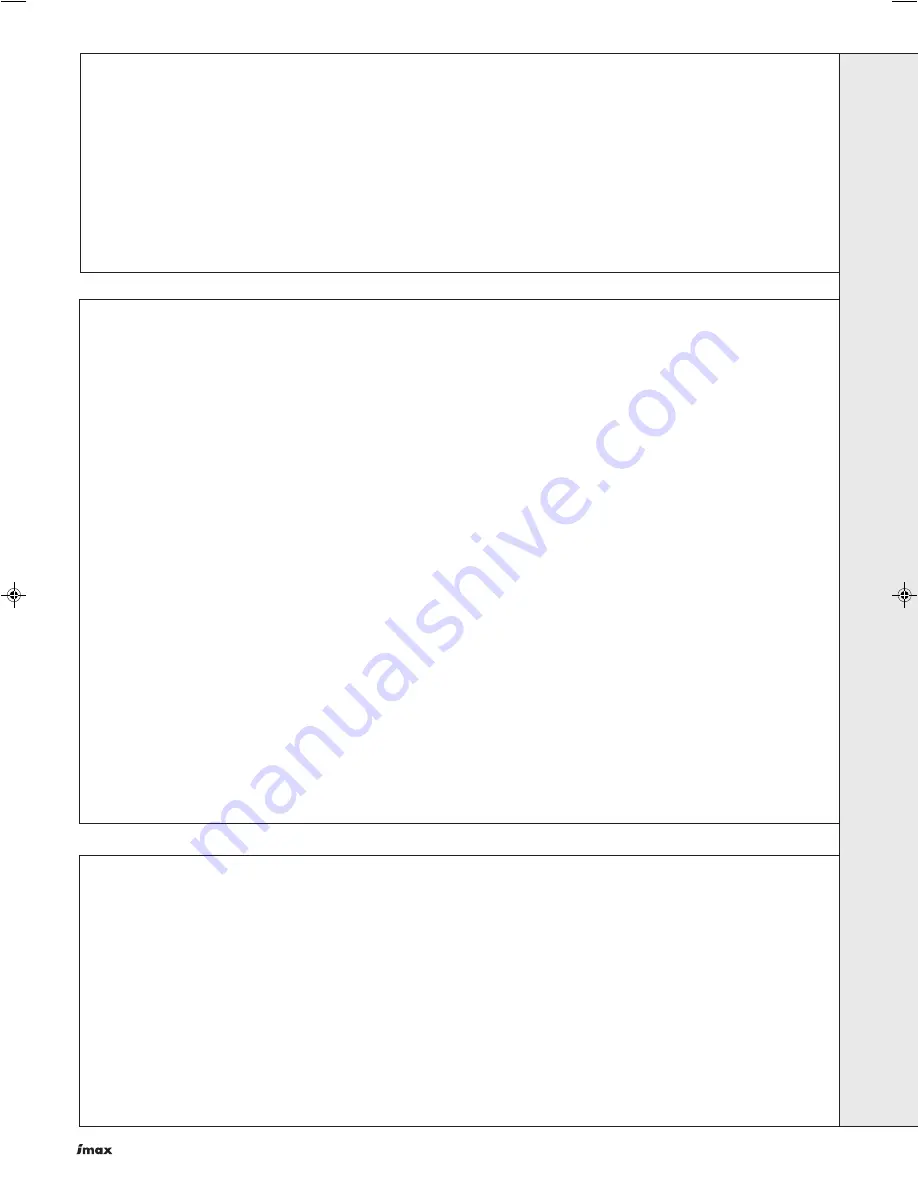
31
xtra
-
Installation & Servicing
INSTALLATION
39 INITIAL LIGHTING
1.
Check that the system has been filled and the boiler is not
air locked - air in the boiler could damage the heat
exchanger. For this reason if an automatic air vent has
been fitted it must never be off.
2.
Check that all the drain cocks are closed and any valves in
the flow and return are open.
3.
Check that the GAS SERVICE COCK IS ON.
4.
Check the indication on the pressure gauge. If the
pressure is less than 0.8 bar the installation should be
filled up first (sealed system only).
5.
Switch the electricity supply ON and check that all the
external controls are calling for heat. Check burner switch
is set to on.
6.
The boiler will commence the ignition sequence. The
circulation pump is energised, whilst operating a DHW
valve if required. The fan is run up to starting speed, and
the air pressure switch actuated. The fan then carries out a
pre-purge before moving to ignition speed. A spark is
started and the gas valve opens. Ignition must occur in 3
seconds, and once detected the boiler starts operating.
The boiler is held at a low stabilisation rate for the first 50
seconds. After the stabilisation period the boiler modulates
to achieve the set flow temperature at a restricted ramp up
rate. As the boiler gets within 10
o
C of the set point it is free
to modulate at normal rate. If after 5 attempts the boiler has
failed to light then it will lock out. Press the reset button to
restart the ignition sequence.
Gas Rate
7.
The gas valves are preset at the factory to nominal values.
Dependant on site installation conditions (e.g. flue length)
the boiler performance can vary slightly. To check the
performance, operate the boiler and measure the flue CO
2
values at maximum and minimum rates, whilst adjusting
the gas valve if necessary. (Refer to Frame 44).
8.
Operate the boiler for 10 minutes and check the gas rate
(Table 1). You should obtain a value at least 90% of the
nominal.
9.
Set all the boiler parameters (refer to Frame 29) to
appropriate settings.
Make the following checks for correct operation.
1.
The correct operation of ANY secondary system controls
should be proved. Operate each control separately and
check that the main burner or circulating pump, as the case
may be, responds.
2.
Water circulation system;
a.
With the system HOT examine all water connections for
soundness.
b.
With the system still HOT, turn off the gas, water and
electricity supplies to the boiler and drain down to
complete the flushing process.
c.
Refill and vent the system, clear all air locks and again
check for water soundness.
d.
Balance the system.
3.
Check the condensate drain for leaks and check it is
discharging correctly.
4.
Finally set the controls to the User's requirements.
Note.
If optional kits are fitted then refer to the instructions
supplied with the kits.
40 GENERAL CHECKS
38 COMMISSIONING AND TESTING
A.
ELECTRICAL INSTALLATION
1.
Checks to ensure electrical safety should be carried out
by a competent person.
2.
ALWAYS carry out the preliminary electrical system
checks, i.e. earth continuity, polarity, resistance to earth
and short circuit, using a suitable meter.
WARNING.
Whilst effecting the required gas soundness test and purging air from the gas
installation, open all windows and doors, extinguish naked lights and DO NOT SMOKE.
B. GAS INSTALLATION
1.
The whole of the gas installation, including the meter,
should be inspected and tested for soundness and
then purged in accordance with the recommendations
of the relevant standards listed on page 4.
In IE refer to I.S.820:2002.
INST
ALLA
TION
Содержание F80
Страница 47: ...47 xtra Installation Servicing NOTES...