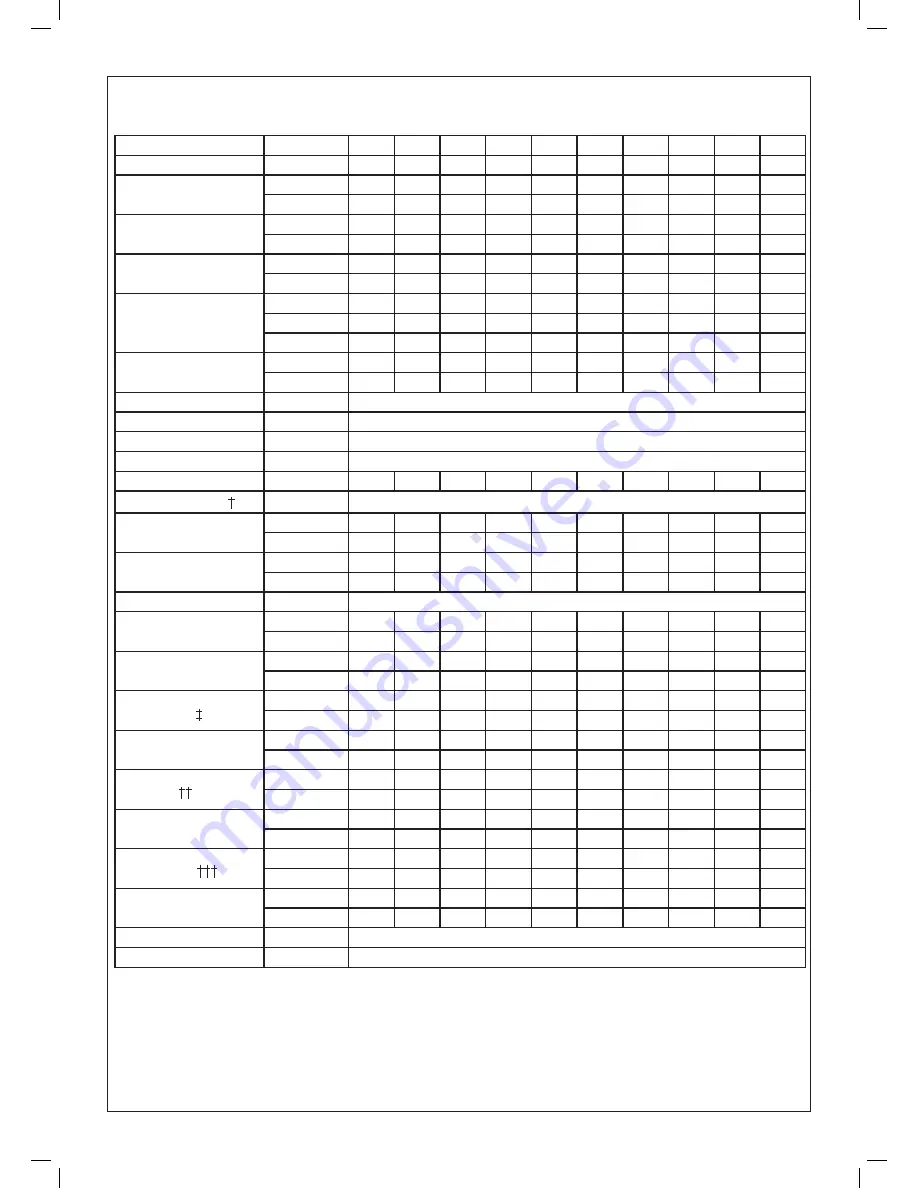
5
Concord Super Series 4 -
Installation & Servicing
TECHNICAL DATA
Table 2
Boiler
350 V 400 V 450 V 500 V 550 V 600 V 450 H 500 H 550 H 600 H
No. of modules
7
8
9
10
11
12
9
10
11
12
Heat output
kW
350
400
450
500
550
600
450
500
550
600
Btu/h x 10
3
1194
1365
1535
1706
1877
2047
1535
1706
1877
2047
Heat input
kW
411.6
470.4
592.2
588.0
646.8
705.6
529.2
588.0
646.8
705.6
Btu/h x 10
3
1404
1605
1806
2006
2207
2407
1806
2006
2207
2407
Gas rate
m
3
/h
38.6
44.1
49.7
55.2
60.7
66.2
49.7
55.2
60.7
66.2
ft.
3
/h
1363
1557
1752
1947
2143
2336
1752
1947
2143
2336
Flue gas mass
volume *
at 120ºC (248ºF)
g/s
175
200
225
250
275
300
225
250
275
300
l/s
191
219
246
273
301
328
246
273
301
328
ft.
3
/min
406
464
522
580
638
696
522
580
638
696
Required water
flow rate ± 10%
l/s
7.49
8.56
9.63
10.70
11.77
12.84
9.63
10.70
11.77
12.84
gal./min.
98.7
112.8
126.9
141.0
155.1
169.2
126.9
141.0
155.1
169.2
Hydraulic resistance
12.5 kN/m
2
(50 in w.g.)
Maximum static head**
2 m (6.5 ft.)
Maximum static head
60.0 m (197 ft.) 6.0 bar (85 lb/in
2
)
Electricity supply
230 V ~ 50Hz,
Power consumption
W
630
720
810
900
990
1080
810
900
990
1080
Gas supply pressure
20.0 mbar (8 in. w.g.)
Boiler height
(overall)
mm
1618
1618
2144
2144
2144
2144
1467
1467
1467
1467
in.
63.7
63.7
84.4
84.4
84.4
84.4
57.8
57.8
57.8
57.8
Boiler width
(overall)
m m
1822
1822
1833
1833
1833
1833
2393
2393
2393
2393
in.
71.7
71.7
72.2
72.2
72.2
72.2
94.2
94.2
94.2
94.2
Boiler depth (overall)
1350 mm (53.1 in.)
Weight of casing
and insulation
kg.
134
126
197
190
182
175
197
190
182
175
lb.
295
278
435
418
402
386
435
418
402
386
Weight of
modules
kg.
371
424
477
530
583
636
477
530
583
636
lb.
818
935
1052
1168
1282
1402
1052
1168
1282
1402
Weight of gas &
water headers
kg.
260
263
311
313
315
318
298
300
302
304
lb.
573
580
686
690
694
701
657
661
665
670
Water content
boiler
l.
63.3
68.1
97.6
102.4
107.2
112
92.6
97.4
102.2
107
gal.
14.1
15.1
21.6
22.7
23.9
24.9
20.5
21.6
22.7
23.7
Flow and return
connection
mm
100
100
125
125
125
125
125
125
125
125
in.
4.0
4.0
5.0
5.0
5.0
5.0
5.0
5.0
5.0
5.0
Gas connection
Rc
2
2
2
2
2
2
2
2
2
2
in. BSP
2
2
2
2
2
2
2
2
2
2
Flue pipe size
(nominal bore)
mm
350
350
400
400
450
450
400
400
450
450
in.
14
14
16
16
18
18
16
16
18
18
Flue socket size
mm
400
400
450
450
501
501
450
450
501
501
in.
15
3
/
4
15
3
/
4
17
1
/
4
17
1
/
4
19
3
/
4
19
3
/
4
17
3
/
4
17
3
/
4
19
3
/
4
19
3
/
4
Injector size
7.3 mm (0.28 in.)
Type of gas
Natural gas (G20 only)
GENERAL
Содержание Concord Super Series 4 100 V
Страница 2: ......
Страница 39: ...37 Concord Super Series 4 Installation Servicing ...