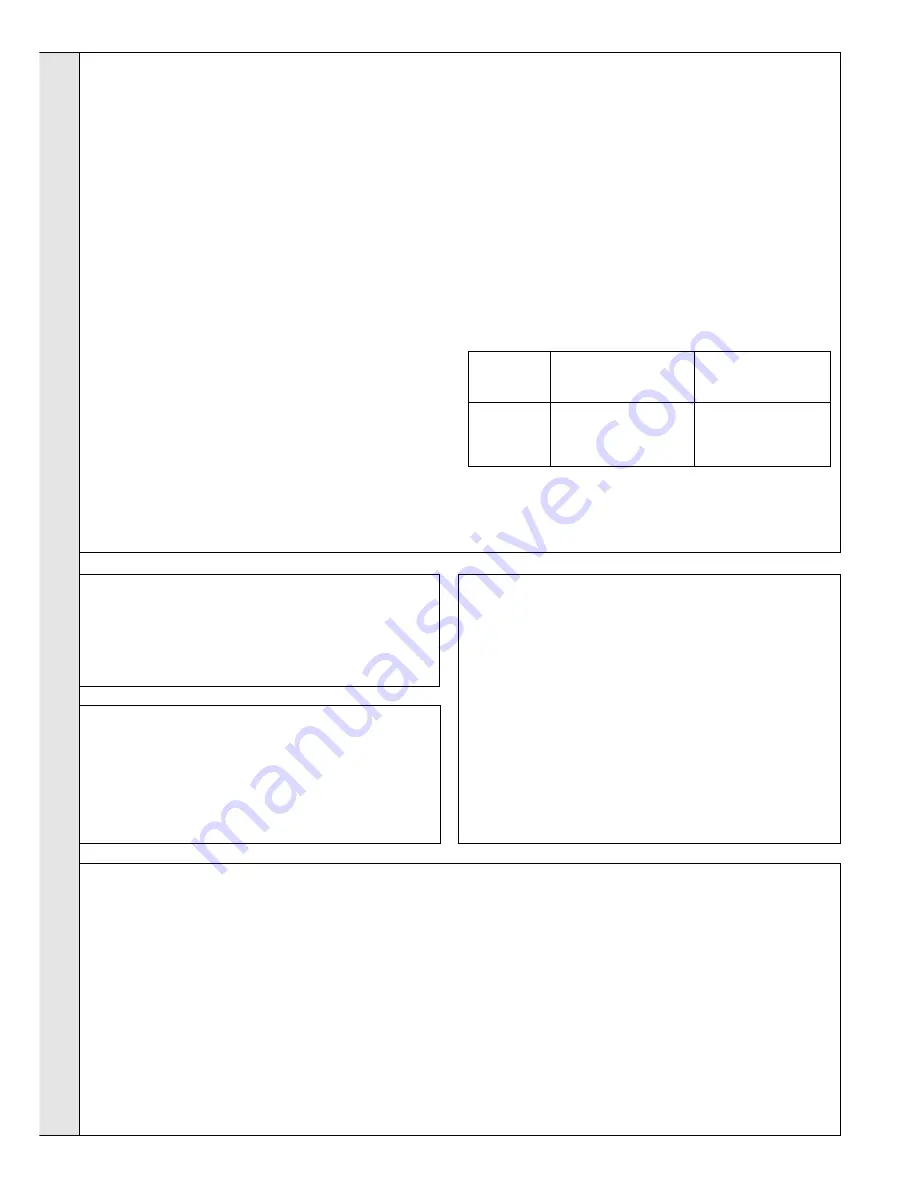
18
Concord CXA/H
- Installation and Servicing
INSTALLATION
22 GAS PRESSURE
MANIFOLD PRESSURE
The manifold setting pressure must now be checked and
adjusted as necessary.
Start the adjustment procedure with the system cold, on full
load and with all temperature controls set to maximum to
avoid thermostatic shutdown. Remove the blanking screw in
the manifold setting pressure test point and connect a suitable
gas pressure gauge.
Turn on the electrical supply light the boiler and let it operate
for about 10 minutes to stabilise the burners. Check the
pressure and if necessary adjust it as follows:
CXA 40/H-80/H boilers:
The location of the manifold pressure adjuster on the gas
valve is shown in Frame 21. Remove the dust cover and, using
a screwdriver, turn the screw clockwise to increase or anti
clockwise to decrease the pressure, until it is set to the value
in Table 1.
CXA 90/H and 100/H boiler:
The setting procedure must be done in 2 steps. The location
of the of the manifold pressure adjuster on the gas controls is
shown in Frame 21. Unscrew the bottom electrical plug on the
LH gas valve and pull it off. Remove the dust cover and set the
adjuster on the RH gas valve to the value given in Table 7.
Refit the gas valve electrical plug then set the adjuster on the
LH gas valve to give the burner pressure given in Table 7.
Failure to follow this procedure may result in the correct burner
pressure being set but the 2 gas valve governors not working
correctly.
CXA 110/H and 120/H boilers:
The setting procedure must be done in 2 steps. The location
of the of the manifold pressure adjuster on the gas controls is
shown in Frame 21. Remove the dust cover and, using a
screwdriver, screw in the adjuster on the LH valve nearly fully.
Set the adjuster on the RH gas valve until the manifold
pressure is at the value given in Table 7. Unscrew the LH gas
valve adjuster until the manifold pressure falls then screw it in
again until the pressure is set at the value given in Table 7.
Failure to follow this procedure may result in the correct burner
pressure being set but the 2 gas valve governors not working
correctly.
Table 7 - Manifold gas pressure settings
Check there is no spillage of combustion products from the
boiler draught diverter by carrying out a spillage test, as
detailed in BS. 5440:1.
23 SPILLAGE CHECK
24 TESTING
Check that the main burner responds correctly to manual on/
off operations of any controls fitted in the gas control circuit.
Check, in the following manner, the operation of the flame
failure safety device:
1.
Extinguish the main burner and pilot burner by turning off
the main gas inlet cock.
2.
The controls will go to lockout almost immediately and
the lockout light on the control panel will light.
3.
Turn the gas cock again, and press in and release the
lockout reset button on the control box. After a period of
time the controls reset the boiler and it will relight.
4.
Complete the commissioning section of the boiler log book.
25 ADJUSTMENT OF WATER FLOW
RATE THROUGH THE BOILER
26 HANDING OVER
ROUTINE OPERATION
Full instructions covering routine lighting and operation of the
boiler are given on the Lighting and Operation Instruction
Label located on the inside of the casing door.
Draw the attention of the boiler owner or his representative to
the Lighting and Operating Instruction Label on the inside of
the casing door. Give a practical demonstration of the
lighting and shutting down of the boiler.
Describe the function of the boiler and system controls and
show how they are adjusted and used.
Describe the function of the downdraught thermostat if fitted.
Hand these Installation and Servicing Instructions, User's
Instructions and Log book to the customer and request him
to keep them in a safe place for ready reference
IMPORTANT.
Point out to the owner that the boiler must have
regular maintenance and cleaning, at least annually, in order
to ensure reliable and efficient operation. Regular attention
will also prolong the life of the boiler and should preferably
be performed at the end of the heating season.
After servicing complete the service section of the log book
and return to the owner or their representative.
Recommend that a contract for this work should be made
with the regional gas authority or a CORGI registered
heating installer.
At the end of the adjustment procedure replace the dust covers,
disconnect the gas pressure gauge and replace the blanking
screw in the manifold pressure test point.
The gas rate for each size of boiler is given in Table 1 on page 4.
When commissioning the heating/domestic hot water system
the shunt pump must be adjusted to give the minimum flow
rate given in Table 4, when that part of the system intended to
be used for dissipation of residual heat only is in operation.
RH valve adjustment
LH valve (and final)
Boiler
pressure
adjustment pressure
mbar
mbar
CXA 90/H
9.0
9.6
CXA 100/H
10.0
10.7
CXA 110/H
11.6
11.1
CXA 120/H
12.6
12.1
INST
ALLA
TION
Содержание Concord CXA 100/H
Страница 1: ......