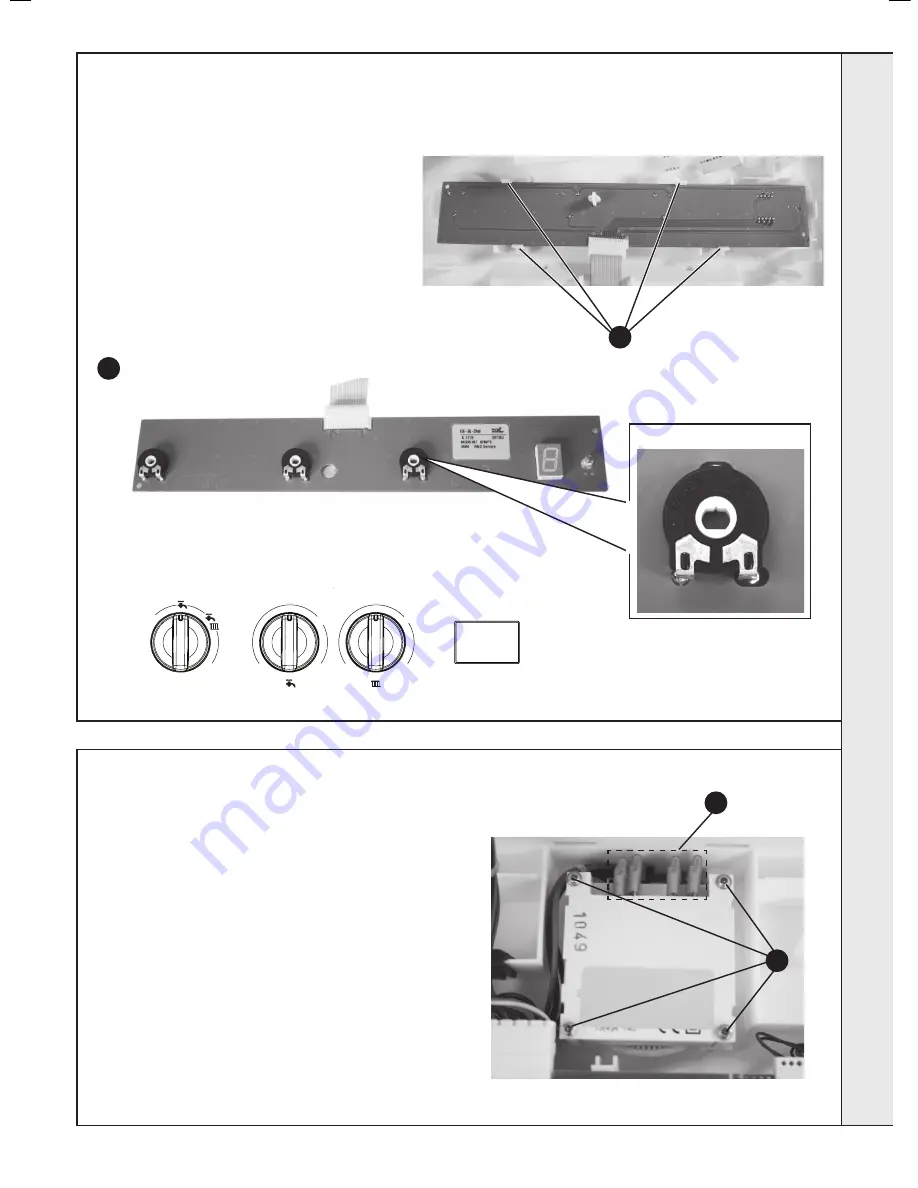
43
SERVICING
i
combi
-
Installation and Servicing
Note. Fit the earth strap provided with the PCB
to your wrist and a suitable earth on the boiler
chassis.
1.
Refer to Frame 40.
2.
Remove the main PCB, refer to Frame 50.
3.
Unclip the PCB and lift to clear the mounting
posts.
4.
Fit the new PCB ensuring the 3 potentiometer
spindles line up with the control knobs which
must be in a vertical position.
5.
Reassemble in reverse order.
6.
Check operation of the boiler. Refer to Frames
29 & 30.
51 UsER CONTROL pCb REpLaCEMENT
3
Potentiometer spindle
Control Knobs (to be in vertical position)
PCB
4
1.
Refer to Frame 40.
2.
Swing the boiler lower front panel into the service
position. Refer to Frame 34.
3.
Remove the 4 fixing screws.
4.
Disconnect the 4 push on connectors.
5.
Remove programmer.
6.
Re-fit 4 push on connectors to new programmer.
7.
Fit programmer and retain with 4 screws previously
removed.
8.
Replace the lower front panel.
9.
Check operation of the boiler. Refer to Frames 29 &
30.
note.
To program refer to user guide at rear of this
book.
52 REpLaCINg ThE MEChaNICaL TIMER
19
20
21
22
23
24
1
2
3
4
5
6
7
8
9
10
11
12
13
14
15
16
17
18
00
I
PREHEAT
STATUS
BURNER
E
24
i
MODE
OFF
MIN
MIN
MAX
RESET
PRE
HEAT
MAX
2
4
s
ER
VICIN
g
Содержание i 35
Страница 2: ...2 i combi Installation and Servicing...
Страница 58: ...58 SPARE parts i combi Installation and Servicing...