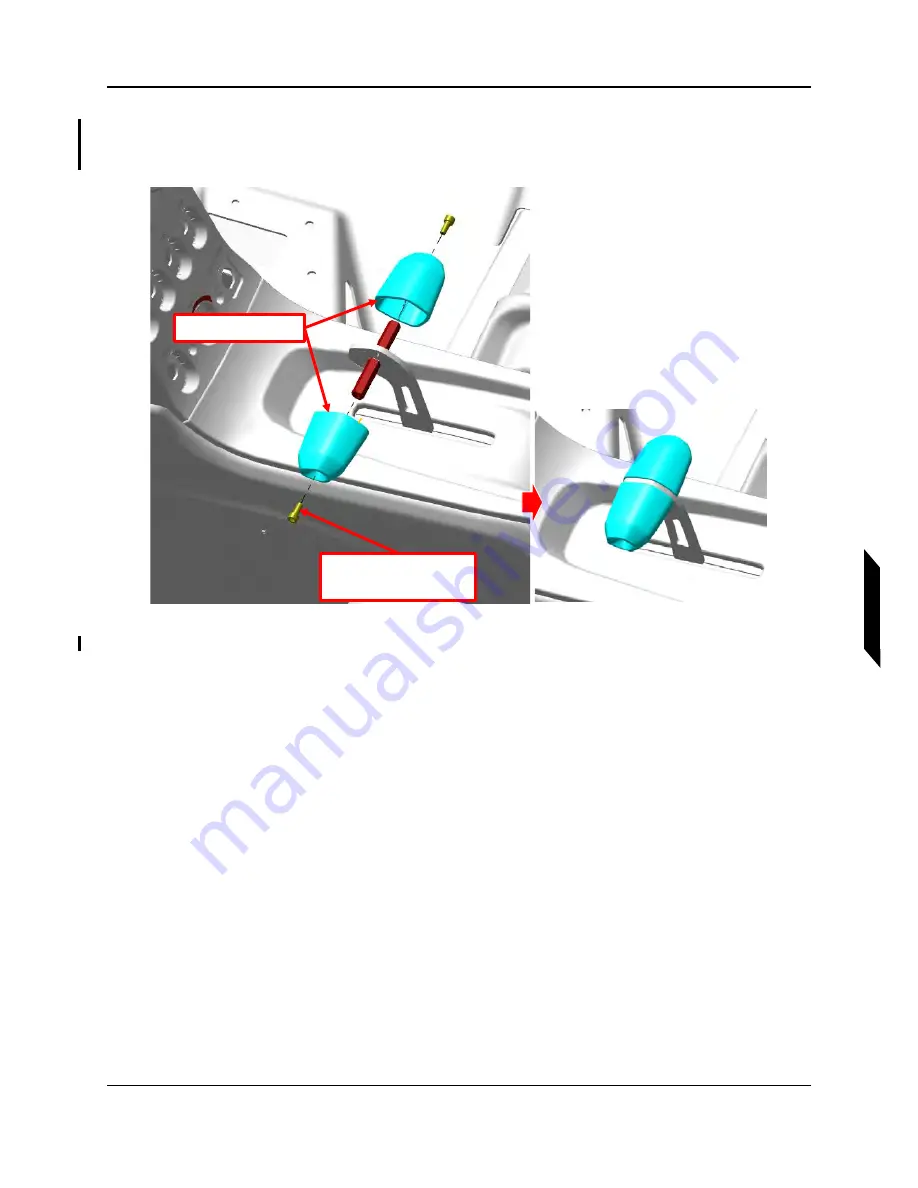
EQUIPMENT AND FURNISHINGS / EQUIPMENT AND FURNISHINGS GENERAL MAINTENANCE
8-11
CHANGE C1
ICON A5 / MAINTENANCE MANUAL
CHA
P
TER
8
2.
Remove 2X Screws which secure the handle grips using a 9/64 hex wrench. Separate the two
halves of the handle to remove it from the throttle lever. Retain all fastening hardware and handle
components. See Figure 8-7.
FIGURE 8-7
THROTTLE HANDLE SCREWS
3.
Remove the standoff that is inserted into the throttle lever. Retain hardware. See Figure 8-8.
2x
Screw
Apply Thread Locker
Throttle Handles
Содержание A5
Страница 4: ...IV TABLE OF CONTENTS ICON A5 MAINTENANCE MANUAL ISSUE C3...
Страница 112: ...3 60 INSPECTIONS SYSTEM SPECIFIC INSPECTIONS ICON A5 MAINTENANCE MANUAL CHANGE C2 CHAPTER 3...
Страница 126: ...4 14 STRUCTURES USE OF VHB TAPE FOR INSTALLATIONS AND REPAIRS ICON A5 MAINTENANCE MANUAL CHANGE C2 CHAPTER 4...
Страница 137: ...ELECTRICAL SYSTEM ELECTRICAL SYSTEM WIRING DIAGRAMS 6 9 CHANGE C2 ICON A5 MAINTENANCE MANUAL CHAPTER 6...
Страница 138: ...6 10 ELECTRICAL SYSTEM ELECTRICAL SYSTEM WIRING DIAGRAMS ICON A5 MAINTENANCE MANUAL CHANGE C2 CHAPTER 6...
Страница 139: ...ELECTRICAL SYSTEM ELECTRICAL SYSTEM WIRING DIAGRAMS 6 11 CHANGE C2 ICON A5 MAINTENANCE MANUAL CHAPTER 6...
Страница 141: ...ELECTRICAL SYSTEM ELECTRICAL SYSTEM WIRING DIAGRAMS 6 13 CHANGE C2 ICON A5 MAINTENANCE MANUAL CHAPTER 6...
Страница 151: ...ELECTRICAL SYSTEM ELECTRICAL SYSTEM WIRING DIAGRAMS 6 23 CHANGE C2 ICON A5 MAINTENANCE MANUAL CHAPTER 6...
Страница 152: ...6 24 ELECTRICAL SYSTEM ELECTRICAL SYSTEM WIRING DIAGRAMS ICON A5 MAINTENANCE MANUAL CHANGE C2 CHAPTER 6...
Страница 156: ...6 28 ELECTRICAL SYSTEM ELECTRICAL SYSTEM WIRING DIAGRAMS ICON A5 MAINTENANCE MANUAL CHANGE C2 CHAPTER 6...
Страница 342: ...9 106 FLIGHT CONTROLS YAW CONTROLS ICON A5 MAINTENANCE MANUAL CHANGE C3 CHAPTER 9...
Страница 398: ...11 20 FUSELAGE AND VERTICAL TAIL WATER RUDDER ICON A5 MAINTENANCE MANUAL CHANGE C1 CHAPTER 11...
Страница 420: ...12 22 HORIZONTAL TAIL HORIZONTAL TAIL TIP PIN ICON A5 MAINTENANCE MANUAL CHANGE C1 CHAPTER 12...
Страница 425: ...INSTRUMENTS AND AVIONICS TROUBLESHOOTING 13 5 CHANGE C2 ICON A5 MAINTENANCE MANUAL CHAPTER 13 2 Left Crossbeam...
Страница 508: ...13 88 INSTRUMENTS AND AVIONICS PITOT STATIC ANGLE OF ATTACK AOA SYSTEM ICON A5 MAINTENANCE MANUAL CHANGE C2 CHAPTER 13...
Страница 512: ...14 4 LANDING GEAR DIAGRAM SCHEMATIC ICON A5 MAINTENANCE MANUAL CHANGE C2 CHAPTER 14 14 2 Diagram Schematic...
Страница 608: ...14 100 LANDING GEAR AFT NOSE LANDING GEAR DOOR ICON A5 MAINTENANCE MANUAL CHANGE C2 CHAPTER 14...
Страница 624: ...15 16 PLACARDS AND MARKINGS PLACARDS AND MARKINGS GENERAL MAINTENANCE ICON A5 MAINTENANCE MANUAL CHANGE C1 CHAPTER 15...
Страница 627: ...PROPULSION 16 3 CHANGE C2 ICON A5 MAINTENANCE MANUAL CHAPTER 16 Install Spinner Dome 16 106...
Страница 658: ...16 34 PROPULSION ENGINE ICON A5 MAINTENANCE MANUAL CHANGE C2 CHAPTER 16 FIGURE 16 20...
Страница 659: ...PROPULSION ENGINE 16 35 CHANGE C2 ICON A5 MAINTENANCE MANUAL CHAPTER 16 THROTTLE ASSEMBLY...
Страница 732: ...16 108 PROPULSION PROPELLER ICON A5 MAINTENANCE MANUAL CHANGE C2 CHAPTER 16...
Страница 788: ...19 4 ICON PARACHUTE SYSTEM IPS DIAGRAM SCHEMATIC ICON A5 MAINTENANCE MANUAL CHANGE C1 CHAPTER 19 19 2 Diagram Schematic...
Страница 822: ...19 38 ICON PARACHUTE SYSTEM IPS ACTIVATION SYSTEM ICON A5 MAINTENANCE MANUAL CHANGE C1 CHAPTER 19...