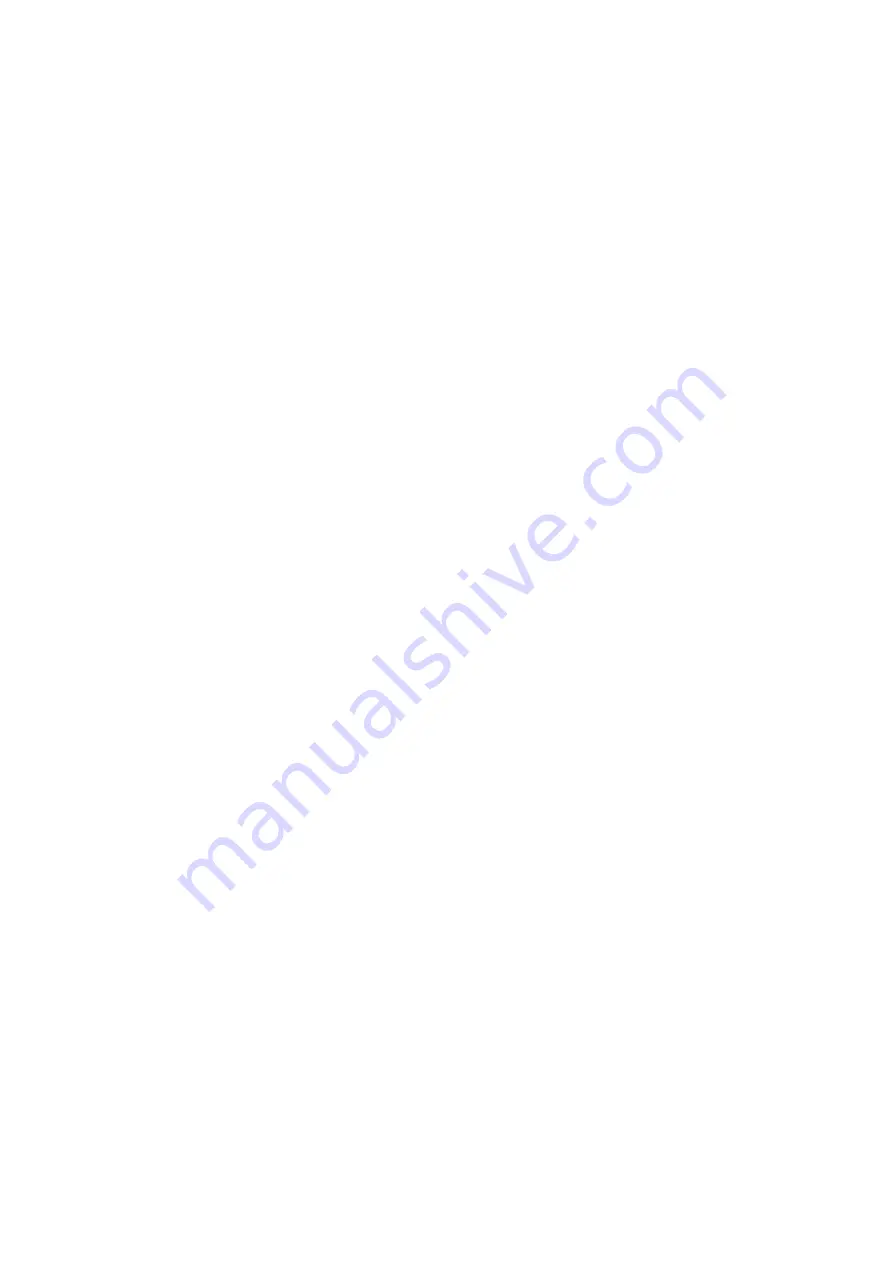
Maintenance
38
METHODS FOR CHECKING THE SAFETY DEVICES
CHECK OF THE SAFETY PRESSURE SWITCH
The safety pressure switch calibration must be at least 0.5 bar below the calibration of the safety valves.
To check the correct intervention of the safety pressure switch, it is necessary to increase the calibration of the adjustment pressure
switch(es) and ensure the switch-off of the burner and activation of the block on the boiler electrical panel by visually following
the indication given by the pressure gauge.
EXTRAORDINARY MAINTENANCE
The generator must be stopped periodically for a thorough inspection and maintenance: the time interval between downtime is
established through experience, by operating conditions, by the quality of the feed water, and by the type of fuel used.
Before accessing the boiler body for inspection or cleaning, thoroughly check that no water or steam can reach the boiler through
the connecting ducts. Each valve will have to be locked and, if necessary, isolated by removing a section of the connection pipe
to the system or by placing a blind flange in-between.
The pressurised parts must be carefully examined internally to look for any build-up, corrosion and other potential sources of
danger pertaining to the feed water.
It is necessary to remove the deposits through mechanical or chemical action and use suitable tools to ensure that the actual
thickness of the internal parts is not affected by corrosion. Any pockmark or other type of corrosion must be scraped and cleaned
with an iron brush until the metal is exposed. The space between every fire tube and tube plates must be checked for leaks: any
welding operation must always be performed in compliance with law requirements, remembering that the boiler is a pressure
equipment posing a danger of bursting and subject to inspection by the designated Body.
During inspection, check all safety accessories.
Cooke Industries - Phone: +64 9 579 2185 Email: [email protected] Web: www.cookeindustries.co.nz