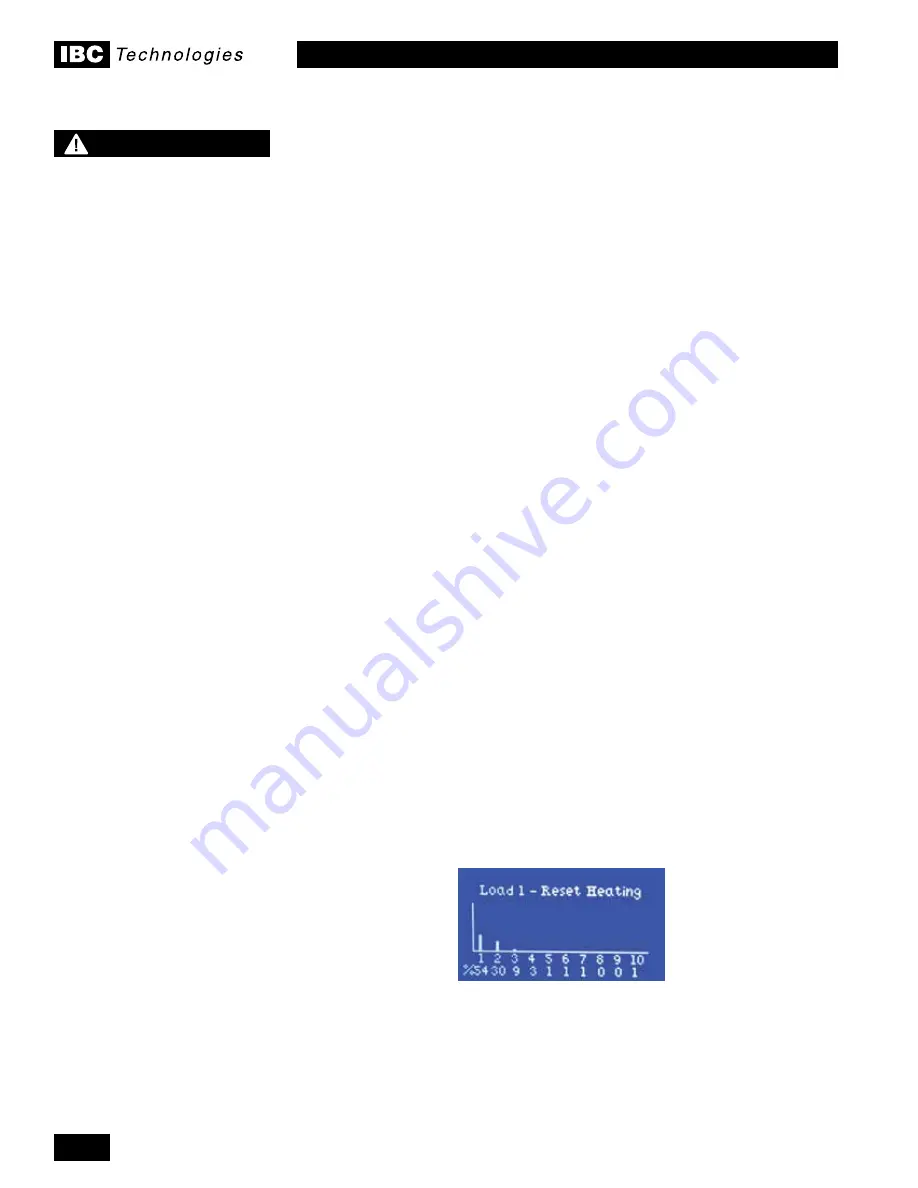
INSTALLATION AND OPERATION INSTRUCTIONS
4-2
VFC 15-150 - VFC 45-225 MODULATING GAS BOILERS
4.1.6 Heat Exchanger
during burner inspection (with the burner removed), examine the heat exchanger
tubes adjacent to the burner’s normal position. in areas of poor gas quality, there
may be a buildup of black plaque (typically sulfur). other fouling agents: airborne
dust, debris and volatiles.
The VFC heat exchanger has a larger surface area and significantly larger
flue-paths than other condensing boilers; consequently it has more resilience to
fouling. Clean when the gaps between the tubes become blocked with plaque,
in accordance with technical notes “Heat eXCHanger Cleaning Version
1.2”. anticipate action every 2 – 5 years for typical residential use, or annually for
boilers in commercial applications. Hard working boilers may need more frequent
inspection and cleaning. newer models are equipped with an internal “hours of
use” timer, which will alert users when cleaning is required.
4.1.7 Pump
Check that the pump is on in normal operation and that the water Δ°T is
reasonable for a given firing rate (e.g. 10°F between supply and return when
firing at 75,000 Btu/hr. for a VFC 15-150 unit).
4.1.8 Gas Piping
Check for damage or leaks and repair as needed.
4.1.9 Control Module
•
Check that boiler operation is consistent with the steps in
Section 2.5
Sequence of Operation
.
•
Check that water temperature targets and setpoint is satisfactory and have
not been adversely amended.
•
Check the operating history using the screen: - use
Installer Setup // Logs
, to
scan for hours of service, cycles per hour, and any logged errors. one method
is to use the graphical presentation of the duty cycle by load – go to logs,
move the cursor to a load and push “Enter” to access. This gives a profile of
the boiler’s duty cycle by throttle level – see below.
•
The first screen (below) shows that this boiler (a 15-150) has operated for
54% of total load 1 on-time at the bottom 10% of the throttle range (e.g.
between 15,000 to 27,500 Btu/hr.).
•
Where a load is heavily weighted to the lowest firing rate and the cycles/
day count is in excess of 96/day, there may be insufficient loading of the
boiler. Consider increasing the temperature target for such load and/or the
respective Minimum temperature setting.
•
if a problem exists with the control, consult troubleshooting guide.
CAUTION
The IBC heat exchanger has a
small amount of combustion
chamber insulation (refractory),
which contains ceramic fibers.
When exposed to extremely high
temperatures, the ceramic fibers,
which contain crystalline silica,
can be converted into cristo-
balite - which is classified as a
possible human carcinogen.
Care should be taken to avoid
disturbing or damaging the re-
fractory. If damage occurs, con-
tact the factory for directions.
Avoid breathing and contact with
skin and eyes and follow these
precautions:
1. For conditions of frequent
use or heavy exposure, respira-
tor protection is required. Refer
to the “NIOSH Guide to the
Selection and Use of Particulate
Respirators Certified under 42
CFR 84” for selection and use of
respirators certified by NIOSH.
For the most current informa-
tion, NIOSH can be contacted at
1-800-356-4676 or on the web at
www.cdc.gov/niosh.
2. Wear long sleeved, loose fit-
ting clothing, gloves and eyes
protection.
3. Assure adequate ventilation.
4. Wash with soap and water
after contact.
5. Wash potentially contami-
nated clothes separately from
other laundry and rinse washing
machine thoroughly.
6. Discard used insulation in an
air tight plastic bag.
NIOSH stated first aid:
Eye contact - Irrigate and wash
immediately.
Breathing - Provide fresh air.
Содержание VFC 15-150
Страница 77: ...6 9 DIAGRAMS VFC 15 150 VFC 45 225 MODULATING GAS BOILERS Diagram 6 2 3 Internal wiring diagram...
Страница 81: ...NOTES...
Страница 82: ...NOTES...