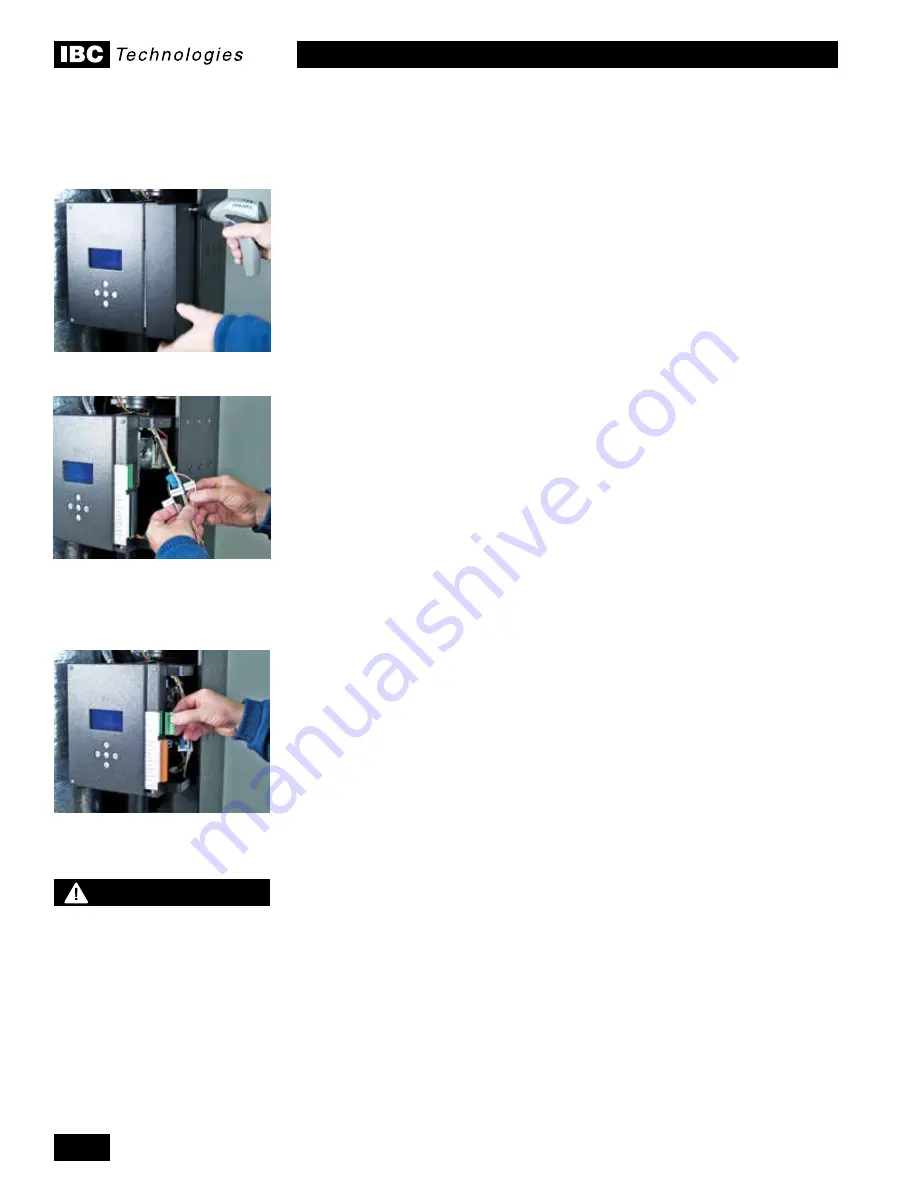
INSTALLATION AND OPERATION INSTRUCTIONS
1-26
VFC 15-150 - VFC 45-225 MODULATING GAS BOILERS
Removing wiring box cover
Line voltage leads for power supply,
primary pump and variable speed
output
Line voltage load pump terminal
strip
eleCtriCal ConneCtions
all electrical wiring to the boiler (including grounding) must conform to local
electrical codes and/or national electrical Code, ans/nFPa no. 70 – latest
edition, or the Canadian electrical Code, C22.1 - Part 1.
1.8.1 120VAC Line Voltage Hook-up
Line-voltage wiring is done within the field-wiring box.
(Refer to Section 6.2.Wiring
Diagram on page 6-4).
Connect the boiler to the grid power using a separate, fused
circuit and on/off switch within sight of the boiler. use 14-gauge wire in BX cable or
conduit properly anchored to the boiler case for mains supply and pump circuits.
Connect a 120 VaC / 15 amp supply to the
“AC IN”
tagged leads in the wiring box.
the max. actual draw (with 4 typical residential size pumps) is less than 4 amps.
if primary / secondary piping is used, with pumps to manage multiple loads, add
a 12” pigtail to bring 120v to the bottom pair of contacts on the Pump/ Zone Valve
terminal Block located on the upper right-hand edge of the controller. the upper
3 pairs of contacts on this green connector strip are then powered to manage up
to 3 load pumps – the top pair for load 1, the second pair for #2 etc. once the
controller is programmed for the respective loads, the boiler will manage all the
loads without need of further relays (oK for loads up to 1/3 HP; for more – use a
protective relay).
The green Pump/Valve terminal strip is not pre-wired because
some installations will use it to manage 24 v zone valves.
the primary pump is connected to the White/Yellow pair labeled
Primary Pump.
this lead is factory wired to the controller (and its 120 VaC supply) at the upper
right backside of the controller board – do not attempt to connect the primary
pump to the Pump/Zone Valve terminal Block along the controller’s right edge
- this is for the secondary pumps and/or zone valves only. Connect the pump’s
Black wire to the Yellow of this pair (switched Hot). the White/ Yellow pair should
be individually capped if the primary pump does not obtain its power from this
pair (e.g. if a variable speed primary pump is connected to the mains power).
If a parallel pump piping configuration is used rather than primary/secondary,
loop the White/Yellow
Primary Pump
pair up to connect this to the lowest pair
of contacts on the green Pump/Valve terminal strip, then connect the two load
pumps in the normal way – this will bring power to the pump control block.
Pumps can be switched on/off using the keypad, so there is no need for
temporary pump wiring during system filling / air purging. If pumps are
hard-wired to the panel during the system fill/purge phase, re-wire the
boiler pump to the Primary Pump leads inside the wiring box, to enable the
water flow proving routine to run.
in a new construction application-
use a construction thermostat – or jumper
with in-line on/off switch – for on/off management of the boiler. Do not
just pull power from the unit, or its moisture management routine will be
interrupted
(fan turns at ultra low rpm for 90 minutes after burner shutdown).
treat it like a computer, where you do not just pull the plug when done. if an
“Insufficient airflow / check vent” error signal shows, check for (and remove) any
water in the clear vinyl air reference tubes. this has been seen occasionally at
construction sites where the boiler has been repeatedly de-powered wet.
the combined current of all pumps connected through the on-board pump relays
should not exceed 10 amps.
1.8
CAUTION
The internal pump relays
in the IBC control have a
maximum rating of 5 Amps or
1/3 H.P. each, with a maximum
total allowable draw of 10
amps.
Isolation contactors MUST be
used if electrical loads exceed
these maximums.
Содержание VFC 15-150
Страница 77: ...6 9 DIAGRAMS VFC 15 150 VFC 45 225 MODULATING GAS BOILERS Diagram 6 2 3 Internal wiring diagram...
Страница 81: ...NOTES...
Страница 82: ...NOTES...