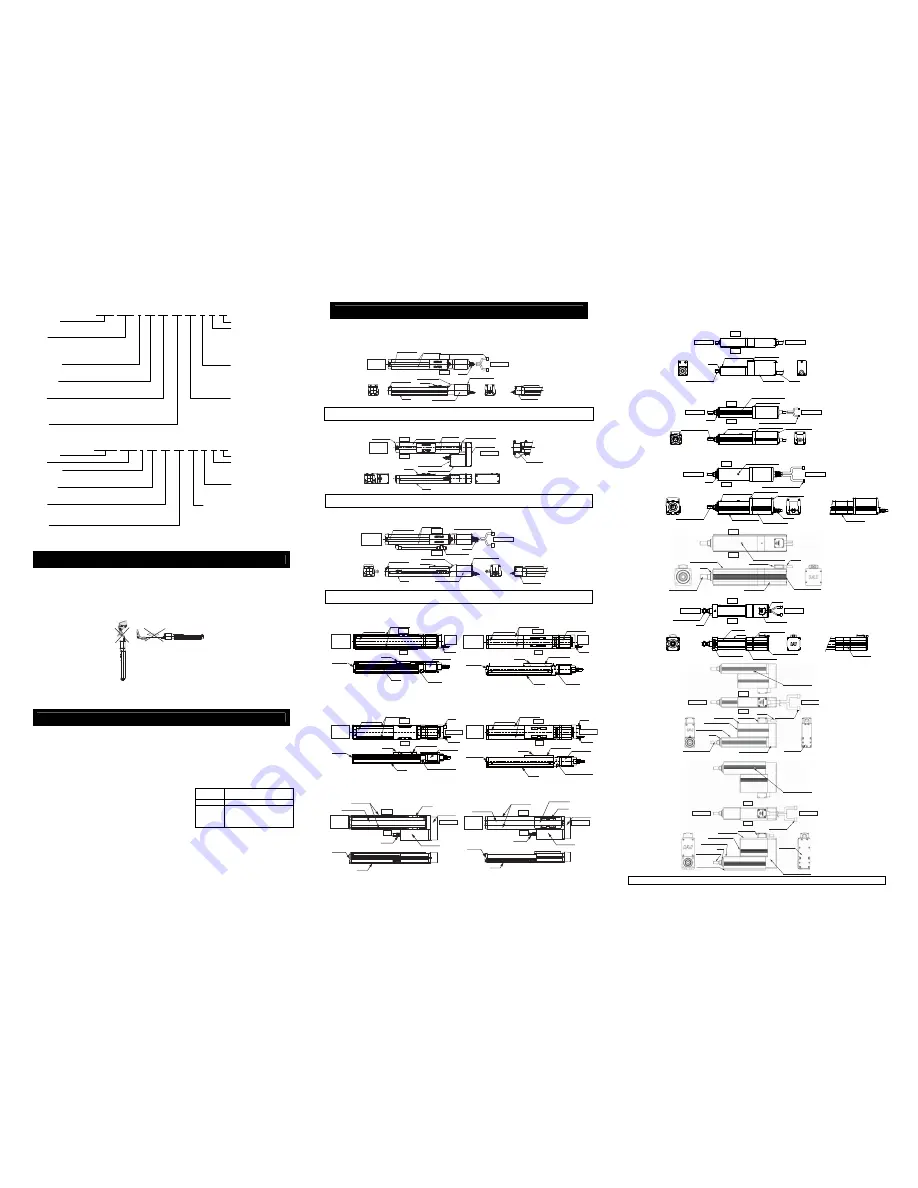
3.3 Arm
Type
[Refer to the catalog or Instruction Manual (DVD) for specification details.]
3.4 Flat
Type
[Refer to the catalog or Instruction Manual (DVD) for specification details.]
*1 This may be displayed for the manufacturing reason.
(This is not to indicate the manufacturing model code.)
Precautions in Handling
1. Handling of the Packed Product
Take the greatest care in transporting the product, not to bump or drop it.
•
An operator should never attempt to carry a heavy package on his own.
•
When setting down the package temporarily, keep it horizontal.
•
Do not step on the package.
•
Do not place on the package a heavy object that may cause the box deformation or apply stress on it.
2. Handling of the Unpacked Product
Do not transport the actuator by holding the cable or move it by pulling the cable.
•
When the actuator is taken out from the package and handled, hold the base section.
•
When the stainless sheet is attached, never hold the stainless sheet section.
•
When transporting the actuator, be careful not to hit it against other objects. In particular, pay attention to the side cover.
•
Do not give any unnatural force to any of the sections in the actuator. In particular, pay attention not to apply any force on
the stainless steel sheet if the actuator is equipped with the stainless steel sheet.
Installation Environment, Storage Environment
1. Installation Environment
An environment that satisfies the following conditions is required during installation.
In general, the actuator for standard and clean-room types should be used in the environment where an
operator can work without equipping any protective gear.
•
There should be no direct sunlight.
•
Any radiant heat from a large heat source such as heat treatment furnace should not be directed at the machine main
body.
•
The ambient temperature should be 0 to 40
°
C.
•
The relative humidity should be 85% or less. There should not be dew condensation. (Standard and clean-room types)
•
If air purge is performed, the actuator will have water resistance of the protective structure shown in the table below.
•
There should not be corrosive gas or flammable gas.
•
There should be no flammable dust or ignitable liquid in the surrounding.
•
Oil mist or cutting liquid should not be directed at the machine.
•
Chemical liquid should not be splashed on it.
•
An impact or vibration should not be transmitted to it.
•
There should not be strong electromagnetic waves,
ultraviolet rays or radiation.
•
The actuator should not be installed where it gets dipped in liquid.
•
The working space required for maintenance or inspection should be secured.
2. Storage and Preservation Environment
•
The storage and preservation environment should comply with the same standards as those for the installation
environment. In particular, when the machine is to be stored and preserved for a long time, pay close attention to
environmental conditions so that no dew condensation forms.
Unless specially specified, moisture absorbency protection is not included in the package when the machine is delivered.
In the case that the machine is to be stored and preserved in an environment where dew condensation is anticipated,
take the condensation preventive measures from outside of the entire package, or directly after opening the package.
•
For storage and preservation temperature, the machine withstands temperatures up to 60°C for a short time, but in the
case of the storage and preservation period of 1 month or more, control the temperature to 50°C or less.
Names of the Parts
1. Slider Type
1.1 RCP2, RCA, RCS2 Standard Type
1.1.1 Motor Straight Type
The Figures above are that of RCP2-SA5C, SA6C and SA7C.
For the other details of appearance, dimensions and outlines for the actuator, refer to the catalog or Instruction Manual (DVD).
1.1.2 Motor Reversing Type
The Figures above are that of RCP2-SA5R and SA6R.
For the other details of appearance, dimensions and outlines for the actuator, refer to the catalog or Instruction Manual (DVD).
1.2 RCP2, RCA, RCS2 Clean-Room Type
The Figures above are that of RCP2CR-SA5C, SA6C and SA7C.
For the other details of appearance, dimensions and outlines for the actuator, refer to the catalog or Instruction Manual (DVD).
1.3 RCS3
Standard
Type
[SA8C]
[SS8C]
1.4 RCS3
Clean-Room
Type
[SA8C] [SS8C]
1.5 RCS3 Motor Reversing Type
[SA8R] [SS8R]
2. Rod Type
2.1 RCP2
2.1.1 Standard Type
[RA2C] There is no brake-equipped type.
[RA3C] There is no brake-equipped type.
[RA4C, 6C]
[RA8C]
[RA10C]
[RA3R]
[RA4R, RA6R]
For the details of dimensions and outlines, refer to the catalog or Instruction Manual (DVD).
Protective
Structure
Model
IP65 RCP2W-RA4C,
RA6C
IP54
RCP2W-RA10C
RCAW-RA3C, RA3D, RA3R
RCAW-RA4C, RA4D, RA4R
RCS2W-RA4C, RA4D, RA4R
Rod
Aluminum Frame
Rod-Tip Adapter
Right
Left
Motor Side
Rod Side
Motor Bracket
Cable
Motor Cover
Grease Supply Port
(Thin Head Screw)
Motor Side
Rod Side
Right
Left
Rod
Rod-Tip Adapter
Aluminum Frame
Motor Bracket
Cable Joint Connector
Motor Housing Motor-End Cap
Range of T-slot
Right
Left
Motor Side
Rod Side
Grease Supply Port
(Thin Head Screw)
Cable Joint Connector
Rod
Rod-Tip Adapter
Aluminum Frame
Motor Bracket
Motor-End Cap
Cable
Motor Housing
Brake Unit
Front Bracket
Cable Cover
Tie Rod
Right
Left
Motor Side
Rod Side
Rod-Tip Bracket
Rod
Cable
Base
Motor Housing
Motor-End Cap
Motor Bracket
Brake Unit
Stainless
Steel Sheet
Side Cover
Cable Joint Connector
Right
Opposite
Side of the
Motor
Cable
Motor Bracket
Slider
Motor-End Cap
Motor Housing
Base
Front Cover
Brake Unit
Motor Side
Left
Right
Left
Opposite
Side of the
Motor
Motor Side
Stainless
Steel Sheet
Side Cover
Attachment Flange
Pulley Cover
Slider
Motor-End Cap
Motor Housing
Base
Front Cover
Brake Unit
Right
Left
Opposite
Side of the
Motor
Motor Side
Stainless
Steel Sheet
Side Cover
Cable Joint Connector
Cable
Motor Bracket
Slider
Motor-End Cap
Motor Housing
Base
Front Cover
Brake Unit
Suction Joint
Right
Left
Opposide
Side of the
Motor
Motor
Side
Screw Cover
Side Cover
Slider
Front
Bracket
Motor Unit
Cable
Bearing
Housing
Base
Stainless
Steel Sheet
Slider
Front
Bracket
Slider Cover
Cable
Base
Motor Unit
Side Cover
Opposide
Side of the
Motor
Motor
Side
Bearing
Housing
Right
Left
Stainless
Steel Sheet
Slider
Front
Bracket
Slider Cover
Joint
Motor Unit
Cable
Bearing Housing
Base
Side Cover
Opposide
Side of the
Motor
Motor Side
Right
Left
Stainless
Steel Sheet
Side Cover
Slider
Front
Brancket
Slider Cover
Joint
Motor Unit
Cable
Bearing Housing
Base
Opposide
Side of the
Motor
Motor Side
Right
Left
Screw Sheet
Reversing
Bracket
Side Cover
Slider
Front
Bracket
Motor Unit
Cable
Base
Right
Left
Opposide
Side of the
Motor
Motor Side
Stainless
Steel Sheet
Reversing
Bracket
Slider
Front
Brancket
Slider Cover
Motor Unit
Cable
Base
Opposide
Side of the
Motor
Motor Side
Side Cover
Right
Left
Grease Supply Port
(Thin Head Screw)
Aluminum Frame
Rod
Rod-Tip Adapter
Motor Cover
Wire Cover
Cable
Motor-End Cover
Right
Left
Reversing Bracket
End Plate
Cable Joint
Connector
Motor Side
Rod Side
Grease Supply Port
(Thin Head Screw)
Cable
Wire Cover
Right
Left
Motor Cover
Motor-End Cover
Rod-Tip Adapter
Aluminum Frame
Rod
Range of T-slot
Motor Side
Rod Side
Grease Supply Port
(Thin Head Screw)
Right
Left
Cable Joint
Connector
Wire Cover
Motor Cover
Motor-End Cover
Rod-Tip Adapter
Aluminum Frame
Rod
Reversing Bracket
End Plate
R C A - A 3 R - I - 2 0 - 1 0 - 5 0 - A 1 - P - B - * *
<Series Name>
RCA
RCS2
<Type>
Arm
Type
A4R
A5R
A6R
<Encoder Type>
I :
Incremental
A
:
Absolute
<Motor Type>
20 :
20W
30 :
30W
<Lead>
5
: 5mm
6
: 6mm
10 : 10mm
12 : 12mm
<Stroke>
Identification for IAI use only
*1
<Option>
B :
Brake
LA : Power Saving Type
NM :
Reversed-Home
Type
MB : Motor Reversing from Lower Side
MR : Motor Reversing from Right Side
ML : Motor Reversing from Left Side
<Cable Length>
N : None
P : 1m
S : 3m
M : 5m
X
□□
: Specified Length
R
□□
: Robot Cable
<Controller>
A1: ASEL
ACON-C/CG
ACON-CY
ACON-SE
ACON-PL/PO
A3: ASEP
R C S 2 - F 5 D - I - 6 0 - 1 6 - 5 0 - T 1 - P - B - * *
<Series Name>
<Type>
<Encoder Type>
I :
Incremental
A
:
Absolute
<Motor Type>
60 : 60W
100 : 100W
<Lead>
4
: 4mm
8
: 8mm
16 : 16mm
<Stroke>
Identification for IAI use only
*1
<Option>
B :
Brake
NM :
Reversed-Home
Type
CE :
CE
Marking
<Cable Length>
N : None
P : 1m
S : 3m
M : 5m
X
□□
: Specified Length
R
□□
: Robot Cable
<Controller>
T1: XSEL-J/K
T2: SCON
SSEL
XSEL-P/Q