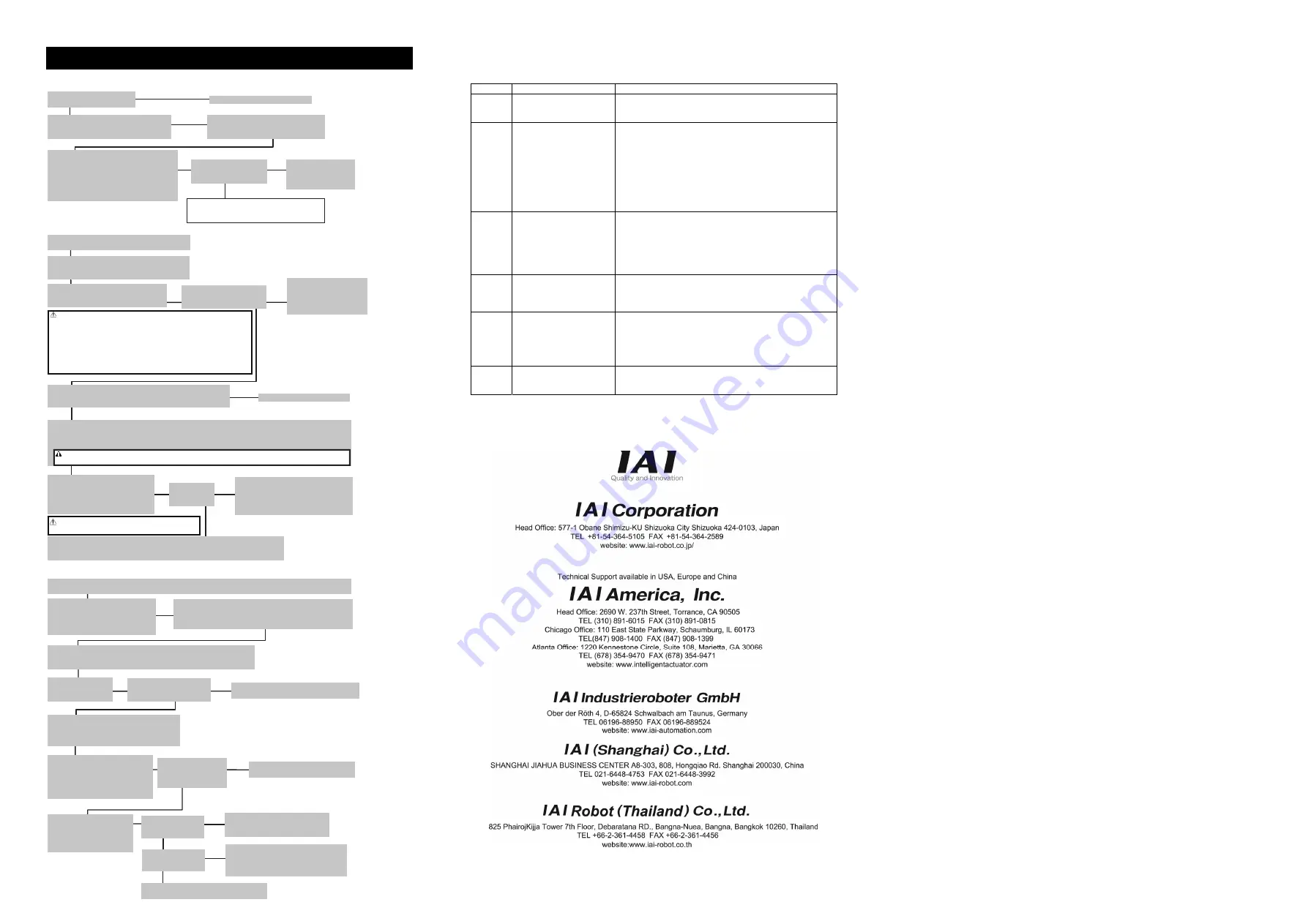
Starting Procedures
When using this product for the first time, make sure to avoid mistakes and incorrect wiring by referring to
the procedure below. “PC” stated in this section means “PC software”.
●
Action to Take When Error Occurred
Shown below are the alarms that you may often see after power up. Have an appropriate treatment following
the instructions below.
Please refer to the Instruction Manual for other alarms.
Error Code
Error Description
Cause and Treatment
069
Real Time Clock
Operation Stop Detection
It indicates the calendar function has stopped and the current
time data has lost.
Have the clock settings again from the teaching tool.
0B8
Excitement Detection Error
The detection of excitation is conducted when the servo is
turned ON for the first time after the power is supplied. The
status is that the detection did not complete even after a certain
time (set in Parameter No.29) was passed.
1) Connection error or wire breakage of motor/encoder cables
2) Brake is not released (when equipped with a brake).
3) Load to the motor is high due to external force.
4) Power was turned on while touching to the mechanical end.
5) The slide resistance of the actuator itself is large.
Those described above can be considered.
0E5 Encoder
Receive
Error
This error code appears when the right signal was not received
from the encoder side to the controller command. Check if any
wire breakage on a connector and the condition of wire
connections. If no error is generated under the condition that the
power to all the peripheral equipment is shut and operate only
this controller and the actuator, noise can be considered as the
cause of the problem.
0E8
A- and B-Phases
Breakage Error
It is the condition that the encoder signal is not properly
detected.
Check if any wire breakage on a connector and the condition of
wire connections.
0EE
Absolute Encoder Error
Detection 2
This error code appears when the absolute encoder PCB cannot
detect the position information properly. The voltage for the
absolute data battery is dropped. Check the battery alarm output
on PIO, and if it is off, replace the battery. Perform Absolute
Reset after the replacement.
Check the encoder cable connection.
20A
Servo OFF While in
Operation
It shows the operation command was generated in the condition
that the servo is OFF.
Resume the operation after turning the servo ON.
Manual No.: ME0288-11A
→
No →
Contact us or our distributor.
↓ Yes
No →
→
↓ Yes
← Yes
→
No →
Check Item
Is the Controller Status Display
LED turned ON in green [SV]?
Check the emergency stop circuit.
→
No →
↓ Yes
↓ Yes
↓
Check if there is any problem with the
installation of the actuator and the condition
of the actuator use exceeds the ranges of the
rated values.
Adjust the servo if necessary.
If an alarm is generated,
connect the PC or teaching
pendant and check the
content of the alarm to have
the right treatment.
Check Item
Any vibration or
abnormal noise?
No →
↓ Yes
Point Check Item
• Is frame ground (FG) connected?
• Has the noise countermeasure been taken?
Check Item
Is the Controller Status
Display LED turned OFF?
Connect the teaching tool
such as PC to confirm the
content of alarm and have
an appropriate treatment.
Have the settings and checks suitable for the used
mode selected from “Positioner Mode” and “Pulse
Train Control Mode” below.
[In the case of Positioner Mode]
Check of Packed Items
Are there all the delivered items?
Installation and Wiring
Perform the installation of and wiring for the
actuator and controller.
Power Supply and Alarm Check
Connect a teaching tool such as PC, turn the
operation mode setting switch to “MANU” side and
turn the power ON for unit.
Select [Teaching Mode 1 Safety Speed Activated /
PIO Operation Invalid] in the teaching tool such as
PC.
PIO Pattern Settings
Set the used PIO pattern to Parameter No.25.
Safety Speed Setting
Set the Parameter No.35 if necessary.
The safety speed is set to 100mm/s at the delivery.
Servo ON
Turn the servo ON with the operation on the
teaching tool such as PC.
Caution
Please perform this process with the actuator away from the mechanical end or
interfering subjects as much as possible.
Put the actuator away if it interferes with surroundings. It may generate an alarm
if the actuator hit the mechanical end or interfering subjects when the servo is
turned ON.
The slider may get slightly dropped by self-weight if servo ON and OFF is
repeatedly performed at the same position. Be careful not to pinch the hand or
damage the work.
Safety Circuit Check
Does the emergency stop circuit (drive cutoff circuit) work properly and
turn the servo OFF?
Target Position Setting
Set the target position in “Position” Box in each position table.
Perform a home-return operation first when Direct Teaching is to be performed. When moving the actuator manually, set
the Brake Release Switch to “BK RLS” side for the brake equipped type. Put the switch back after the setting is complete.
Test Run Adjustment 1
Check the operation without mounting a
work and set the safety speed invalid on
the teaching tool such as PC, and then
check the operation with a work mounted.
Caution To ensure safety, it is recommended that safety
speed be enabled during initial movements.
Test Run Adjustment 2
1) Set the operation mode setting switch to “AUTO”.
2) Output the operation command from PLC to the controller and check the system operation.
Warning Be careful not to pinch fingers or damage the work with the dropped actuator when releasing the brake
in vertical orientation.
→
Check Item
Is the minimum unit of operation set to the value bigger than the
minimum resolution of the encoder?
Is the fraction of the electronic gear ratio reduced to its lowest terms?
← Yes
→
Check Item
Is the Controller Status Display
LED turned ON in green [SV]?
No → Confirm the content of alarm on the teaching
tool such as PC to have an appropriate treatment.
← Yes
↓ Yes
→
No →
No → Check the electronic gear ratio setting.
Confirm the command pulse train input
mode setting.
Confirm that there is no problem in the
actuator installation, the actuator operation
condition demands a voltage more than rated
voltage, and appropriate pulse trains are input.
Check if there is any problem in the way
of actuator mount.
Check Item
Is there any risk of
interfering with peripheral
equipment?
No →
↓ Yes
Can the positioning
operation be performed
normally?
↓ Yes
↓ Yes
Is it in condition without
any vibration and
abnormal noise?
Test Run Adjustment 3
Check the system operation conducted by PLC.
PIO Pattern Settings
Set the used 6 “Pulse train control mode” or 7 “Pulse train control mode for Battery-less Absolute” to Parameter No.25.
Set the Electronic Gear
[Refer to Instruction Manual]
Set the electronic gear ratio based on the
amount of actuator operation per pulse in
Parameters No.65 and 66.
Pulse Train Input Output Mode Setting [Refer to Instruction Manual]
Set the command pulse train input status for the parameter No.63 and No.64.
Put Operation Mode Setting Switch to “AUTO” side when the setting is complete.
Servo ON
Input servo ON signal
from PLC.
Safety Circuit Check
Check that the emergency stop circuit (or motor
drive-power cutoff circuit) operates normally to turn
OFF the servo.
Test Run Adjustment 1
[Operation Mode MANU]
Check with a teaching tool such as the
PC software with no work being loaded,
and check the operation range with JOG
operation with the work being loaded.
Test Run Adjustment 2
[Operation Mode AUTO]
Output the pulse train from PLC
to the controller and check the
system operation.
[In the case of Pulse Train Control Mode (for PLN and PLP types only)]