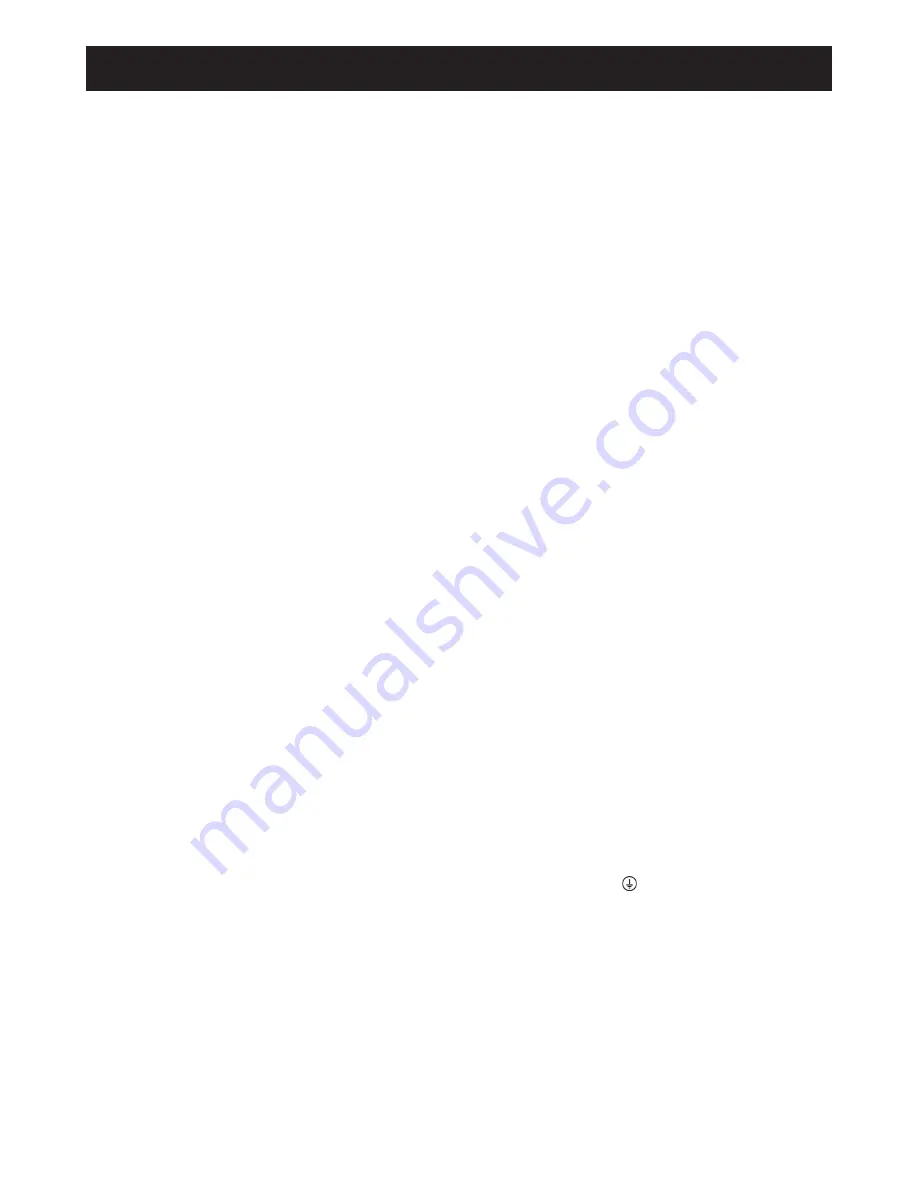
5
INSTRUCTIONS FOR THE INSTALLER
assembly is restrained from accidental contact
with the flue or flue outlet of an underbench oven.
The hose should not be subjected to abrasion,
kinking or permanent deformation and should
be able to be inspected along its entire length.
Unions compatible with the hose fittings must be
used and connections tested for gas leaks. The
supply connection point shall be accessible with
the appliance installed.
Please select the type which is correct for the
supply concerned.
Once the installation is complete, check all
connections for gas leaks with soap and water.
DO NOT use a naked flame for detecting leaks.
Ignite all burners both individually and concurrently
to ensure correct operation of gas valves, burners
and ignition. Turn gas taps to low flame position
and observe stability of the flame for each burner
individually and concurrently. When satisfied with
the hotplate, please instruct the user on the correct
method of operation. In case the appliance fails
to operate correctly after all checks have been
carried out, refer to the authorised service provider
in your area.
Electric connection
The connection to the electric grid must be carried
out by qualified personnel and in conformity with
the regulations in force.
The voltage of the electric system must correspond
to the value indicated in the label under the
appliance. Make sure that the electric system is
provided with an effective ground connection in
compliance with the regulations and provisions of
the law. Grounding is compulsory.
G A S T R A N S F O R M AT I O N S A N D
ADJUSTMENTS
Data Label
A duplicate Data Label is supplied to adhere in an
accessible area next to the appliance.
This appliance is suitable for Natural Gas and Uni-
versal LPG; ensure that the available gas supply
matches the Data Label.
When converting from Natural Gas to Universal
LPG ensure that the NG regulator is removed and
replaced with the Test Point Assembly. An AGA Ap-
proved gas regulator suitable for a supply pressure
of 2.75kPa should be part of the gas tank supply
and the test point pressure should be adjusted to
2.75kPa.
Replacing the nozzles
If the equipment is adjusted for a type of gas that is
different from the one available, it is necessary to
replace the burner nozzles.
The choice of the nozzles to replace must be
made according to the table of the “technical
characteristics” as enclosed.
Act as follows:
remove the racks and burners.
by means of a straight spanner L, unscrew
the nozzle U (fig. 8) and substitute it with the
corresponding one.
tighten the nozzle strongly.
Adjusting the burners
The lowest flame point must always be properly
adjusted and the flame must remain on even if
there is an abrupt shift from the maximum to the
minimum position.
If this is not so, it is necessary to adjust the lowest
flame point as follows:
start the burner up
turn the tap up to the minimum position (small
flame)
remove the knob from the tap rod
introduce a flat-tip screwdriver C in the hole F of
the tap (fig. 9) and turn the by-pass screw up to
a proper adjustment of the lowest flame point.
As regards U-LPG gas burners, the by-pass
screw must be tightened completely.
MAINTENANCE
Maintenance Schedule
No regular maintenance is required for the hotplates
except cleaning.
Replacing the power supply cable
If the power supply cable should be replaced,
it is necessary to use a cable with a section of
3x0.75mm
2
, type H05VV-F or H05RR-F, complying
with the regulations in force.
The connection to the terminal board must be
effected as shown in fig.10 - 10/A:
brown cable L
(phase)
blue cable N
(neutral)
green-yellow cable (ground)
-
-
-
–
–
–
–
Содержание ICD6SG3
Страница 6: ...6 1 2 3 4 5 6A 6 8 7 9 10 10 A V ...
Страница 8: ...8 PRODUCT SERVICE PHONE NUMBER 1800 805 300 ...