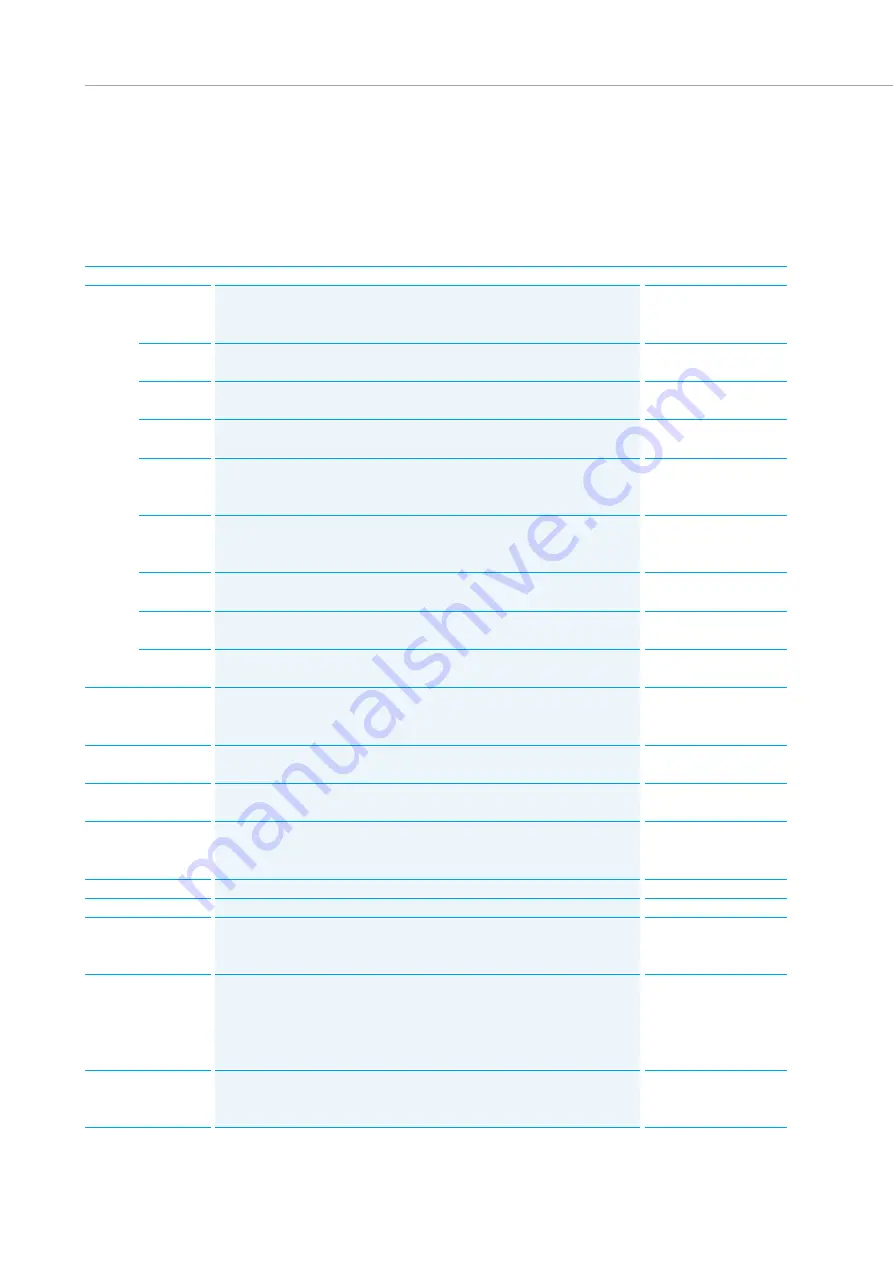
Functions
Function Inventory
Functions
Details
Notes
Protection
Function
Overcurrent
Protection from overload damage based on motor’s thermal characteristics
Trip initiated when current exceeds 112.5 % of set rated current, based on operating time
characteristics (inverse/definite time)
Basic function refer to
cold/hot curve function
Undercurrent
Protection from unloaded operation due to motor load breakdown
Trip initiated according to set undercurrent multiple and runtime
Refer to cold/hot curve
function
Phase Failure
Protection from phase failure due to short or contact failure
Trip initiated at set time if phase difference exceeds 70 %
Selectable function
Phase
Unbalance
Protection from phase unbalance due to insulation failure or incorrect wiring
Trip initiated at set time if phase different exceeds pre-set parameters
Selectable function
Stall
Protection from motor slowdown or lock due to increased load under operation
If overcurrent occurs in definite time, trip initiates when current exceeds a set multiple
after the delay period
Selectable function
Only usable under definite
time setting
Lock
Protection from motor damage due to sudden increase in load or a lock
If overcurrent occurs in definite time, trip initiates when current exceeds set multiple
factor after the delay period
Selectable function
Only usable under definite
time setting
Reverse Phase
Protection from motor reversal due to Incorrect wiring
Detects reversal during startup and trips within 100 msec
Selectable function
Earth Eakage/
Ground Fault
Protection from current leakage due to insulation failure or damage
Trip initiated when current leakage exceeds set parameters
Selectable function
Instantaneous
Protection from shorts of more than two phases due to motor insulation failure or Incorrect
wiring Trips within 50 msec for current in excess of set multiple factor
Selectable function
Dedicated terminal
1)
Overload Warning
Alert activated to prevent a trip from a sudden overcurrent event
Alert switch activates until trip when current exceeds the set activation multiple
Selectable function
Alert terminal removed under
instant-time setting
Cumulative Runtime
Cumulative runtime under minimum of 70 % rated current during relay lifetime
Unit : hours
RESET disabled
Runtime Alert
Runtime management for maintenance, i.e. motor oil replacement
Indicator activates after pre-set runtime is reached
Selectable function
CT Ratio
Increases the number of CT turns for low current; external CT is used for high current.
Actual motor current and current indicated on relay converted to correlate
CT ratio is set to convert rated current parameters and indicated value
(Ex.) For 100: 5 CT, CT ratio set at 20
0.25, 0.5, 1 ~ 200
Delay
Delay time for protection function based on motor startup characteristic
Selectable function
Test
Check relay and sequence status without energizing circuit
Off during operation under
Contact
Output contact activation method selectable 95-96, 97-98: 1a1b, 2a, 2b
Auxiliary contact activation method selectable 07-08 : Dedicated for overcurrent alert,
ground fault or instantaneous
RESET
Select RESET method after trip
Manual (non) / Electrical (Pr) / Automatic (0 ~ 20 min) RESET can be selected :
- Manual reset by pressing the RESET button
- Electrical reset by switching the power off
- Automatic reset by timer (Timer resumes if power is turned off/on before reset)
Manual reset available for
electrical and automatic
settings
Cold/Hot Curve
Overcurrent protection curve based on motor thermal conditions
- Cold : initial period of operation after period of inactivity
- Hot : sufficient heat applied after motor has been in sustained operation
Applicable only for inverse
time overcurrent protection
characteristics
※
1)
Under instantaneous setting, auxiliary terminal 07-08 is automatically set to instantaneous terminal. Refer to information on operational characteristics for details
Technical Data
12
Electronic Motor Protection Relays
Содержание Earth Leakage HGMP N60 Z
Страница 32: ......