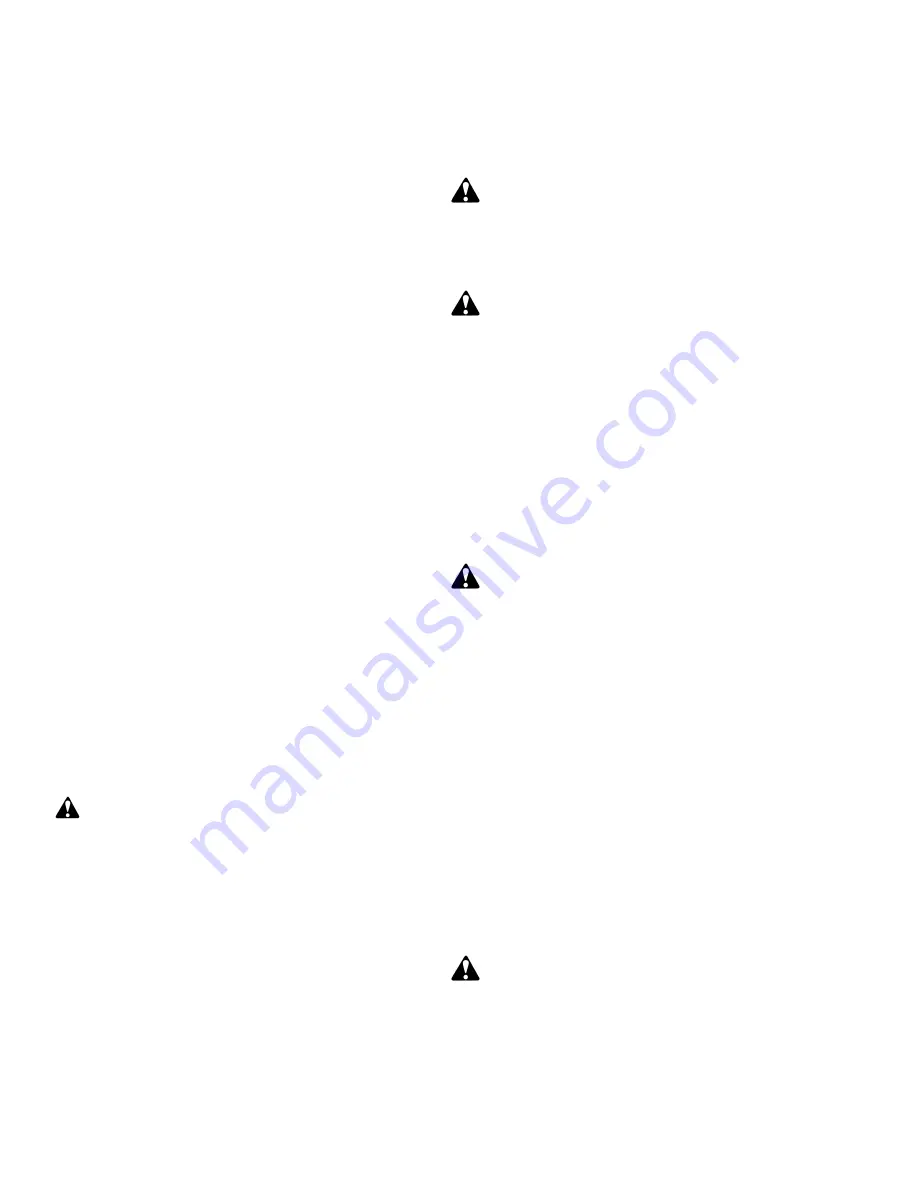
10
truck is not put in a harsh cycle until a few hours of light
duty operation has been accumulated. Avoid ramps and
high speed plugging if possible (DO NOT REDUCE
PLUGGING DISTANCE ADJUSTMENT). Stalling
the motor is very detrimental during the break–in
period.
Little can be done during hoist motor break–in to reduce
in–rush currents, but the frequency of starts can be
reduced. A common practice called jogging can be very
detrimental to the brushes during break–in. Jogging is
commonly done to fine position a load. Rather than
throttle the lift speed with the valve spool, drivers often
rapidly turn the hoist motor on and off in steps to
position the load. This practice has the effect of
destroying the newly developed film on the commutator
that smooths commutation. If jogging is not abused
during the break–in period, an adequate film can be
established. It is critical to curtail jogging for the first 40
to 100 hours of operation. The jogging practice will
reduce brush life and contactor life any time it is done.
Encourage operators to lift the load high enough the first
time to allow positioning the load by careful lowering.
The “stoning” procedure will significantly improve the
brush life of motors which must be put into heavy duty
service immediately (Refer to Page 18).
CLEANING
Periodic cleaning of the motor is essential to prevent
overheating and/or electrical grounds.
Motor Exterior. The exterior should be wiped with a
solvent–moistened cloth to remove any dirt or grease
deposits.
WARNING
Many solvents are highly inflammable and toxic. Be
sure the area is well ventilated and free of flame or
sparks.
Carbon Dust. Remove brush inspection cover. Using
clean, dry compressed air [less than 3.52 kg/cm
2
(50
psi)], blow dust from motor housing, brush holders and
commutator area.
Disassembled Motor Interior. The interior should
preferably be cleaned by suction first to avoid blowing
dirt or metal particles into the insulation. Dust should
then be brushed out of the windings and blown clear
using clean, dry, compressed air. Any grease or oil
present, especially on the commutator, should be
removed by wiping with a clean cloth dampened
slightly with Perchloroethylene.
CAUTION
The cloth should not be wet because liquid solvent
may carry electrical conducting dirt deep into
cracks and voids in the insulation system.
CAUTION
Sealed bearings should never be submerged in
solvent because internal lubricant will deteriorate.
BASIC REPAIR GUIDELINES
The following is a guide to observe when disassembling
a typical motor. (Refer to the electric motor repair
section for specific detail).
1. Match mark the motor fleld case and the two end
housings before separating the components to aid in
reassembly.
CAUTION
Before lifting off the brush–end housing, make sure
that all tension is removed from the brushes
(disengage the brush springs). Keep the brushes
clear of the commutator during installation to
prevent damage to these parts.
2. Carefully lift out or install the armature assembly
with the drive–end (DE) frame attached. Do not lose the
wave washer behind the commutator–end (CE) bearing
on some motors.
3. Do not remove the field windings unless replacement
is necessary. Be sure they are securely mounted to the
frame.
4. The brush holder assembly must be match marked if
removed from end housing. Align marks during
reassembly.
CAUTION
The following Prestolite motors have a maximum
torque value of 3.4 to 4.0 N.m (30 to 35 lb in) for the
terminal nuts and bolts that fasten the end frames.
Prestolite P/N letter codes: MDV, MFD, MMW,
MUD, and MHG.
Содержание A1.00XL
Страница 1: ...Hyster C203 A1 00XL A1 25XL A1 50XL Europe...