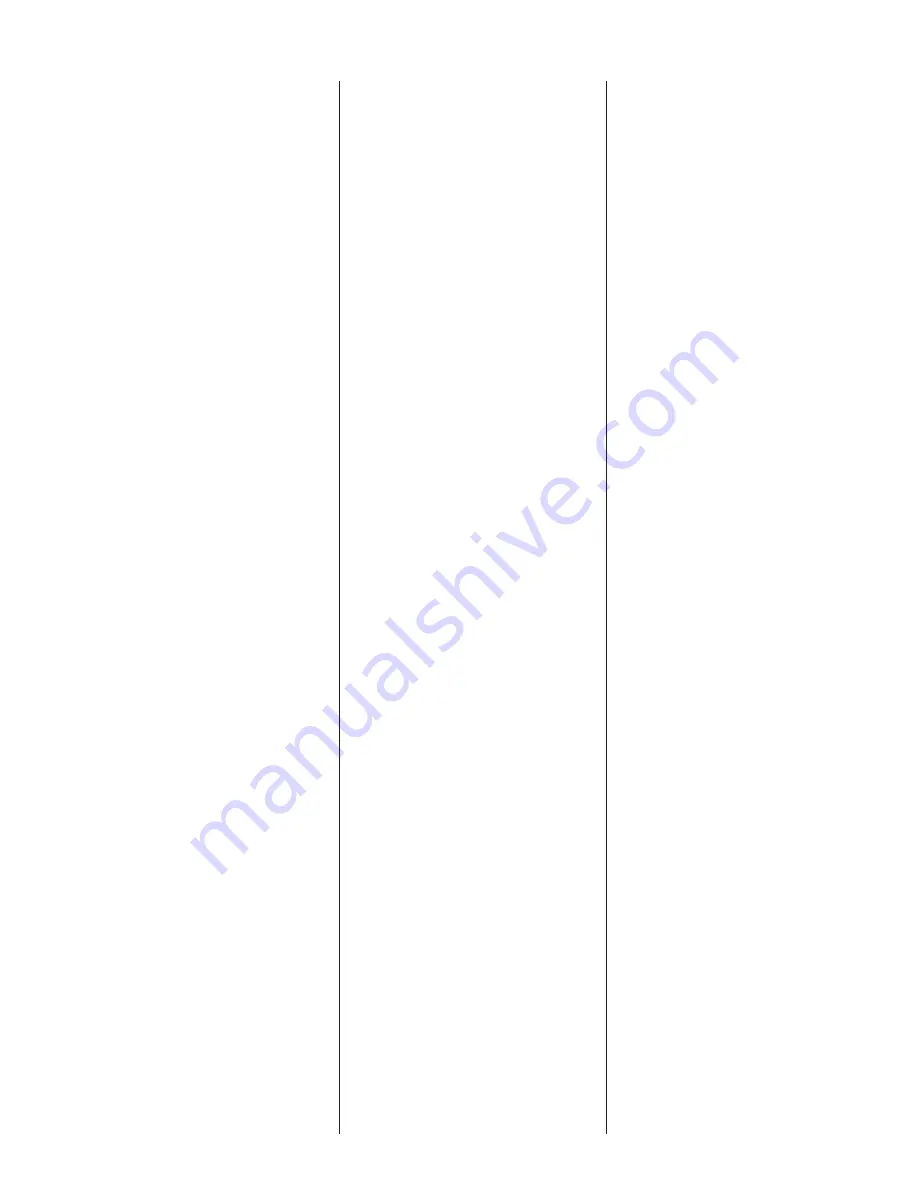
5
Attach one meter lead to the
white cord wire and the other
meter lead to the black cord
wire. See Winding Resistance
Chart for an appropriate
resistance reading. Repeat this
procedure for the black cord
wire and red lead wire. This
reading is the start winding
resistance. Also repeat this
procedure for the white cord
wire and the red cord wire.
This reading is the total motor
winding resistance. If no
resistance is obtainable for
either the start or main
winding, either there is a bad
connection or the winding
is defective.
4. For three phase models, remove
hex head cap screws (8) and lift
off motor dome (25). Prop the
motor dome (25) so as to not
pull and make taut the motor
connection leads. Remove motor
connections (26) from motor
(7) and remove power cord (27)
from pump.
5. Twist the three leads of one
end of the power cord together.
Then at the other end, with an
ohmmeter, check any two
leads. Check the third lead
with either of the first two. If
a zero reading is indicated
for any wire, the wire is
broken and a new power cord
assembly must be ordered.
6. Set ohmmeter scale pointer to
R X 100K scale. Connect one
meter lead to one lead of the
stator and touch the other
meter lead to the motor
housing (25). If the resistance
to the ground is less than
500,000 ohms, there is
moisture in the winding or
leakage through stator
insulation. The stator must be
dried out and then rechecked
on the ohmmeter. If the
resistance is still less than
500,000 ohms after drying, the
stator must be replaced. A zero
reading indicates a direct short,
and the stator will have to
be replaced.
7. If the wiring is grounded,
remove the pipe plug (3) in the
top of the pump and drain the
oil into a glass container. A
milky appearance to the oil
will indicate that water has
entered through and worn or
damaged seals or O-rings. If
this is the case, the mechanical
seals and all O-rings will have
to be replaced. If no apparent
moisture is seen, the stator
must be checked with a high
pot tester. Using a voltage of
1500 volts for 115 volt motors
and 2000 volts for 230 volt
motors, touch one probe to the
white lead and the other probe
to the stator laminations for
only one second. Buzzing will
indicate arcing is occurring at
a breakdown of insulation or
a small amount of moisture
is present. The stator will
then have to be dried out
or replaced.
The high pot test is very
destructive. So, each time the
same stator is checked, the
voltage should be lowered
about 250 volts. If not,
you may cause the stator
to short by breaking down
the insulation.
Caution: Due to the high
voltage, use extreme care when
using the high pot tester. A
dangerous shock can be avoided
with careful handling of the
test probes.
8. Repeat step 3, this time
attaching the meter leads to the
stator wires. If a zero reading is
obtained, the winding is
defective and the stator must
be replaced.
9. Unscrew the hex head cap
screws (11) and remove the
volute (14).
10.On the three phase models first
remove the impeller screw (16)
and impeller washer (17) and
then on all models unscrew the
impeller (15). Hold the
rotor/shaft assembly with a
screwdriver and carefully tap
impeller with a plastic or rubber
hammer.
11.Remove the flat head machine
screw (23) from seal plate (24).
Remove clamp ring (13) and
motor cover assembly (10, 25)
off the seal plate (24).
12.Remove the four hex head
stator bolts and lift the
stator (7) from the seal plate
(24). A
screwdriver can
be inserted under the stator
shell in order to remove the
stator (7).
13. Bump the end of the shaft with
a plastic hammer. This will
push the rotating half of the
mechanical seal (18) from the
shaft and also push the lower
bearing from the seal plate
(24). Now remove the shaft,
rotor and bearing assembly
from the seal plate (24).
14. If water is found in the oil, the
rotating and stationary halves
of the mechanical seal (18,19)
must be replaced. Remove the
stationary seal half by inserting
a screwdriver into seal plate
(24) from the top and tapping
lightly with a hammer.
15. Turn the bearing by hand and
if it feels rough when turned or
looks rusted, it should be
replaced. Obtain a bearing
puller to remove the bearing. If
a puller cannot be placed over
the bearing, remove the outer
face by cracking in a vise. Now
the outer face and balls can be
removed, allowing the inner
face to be pulled.