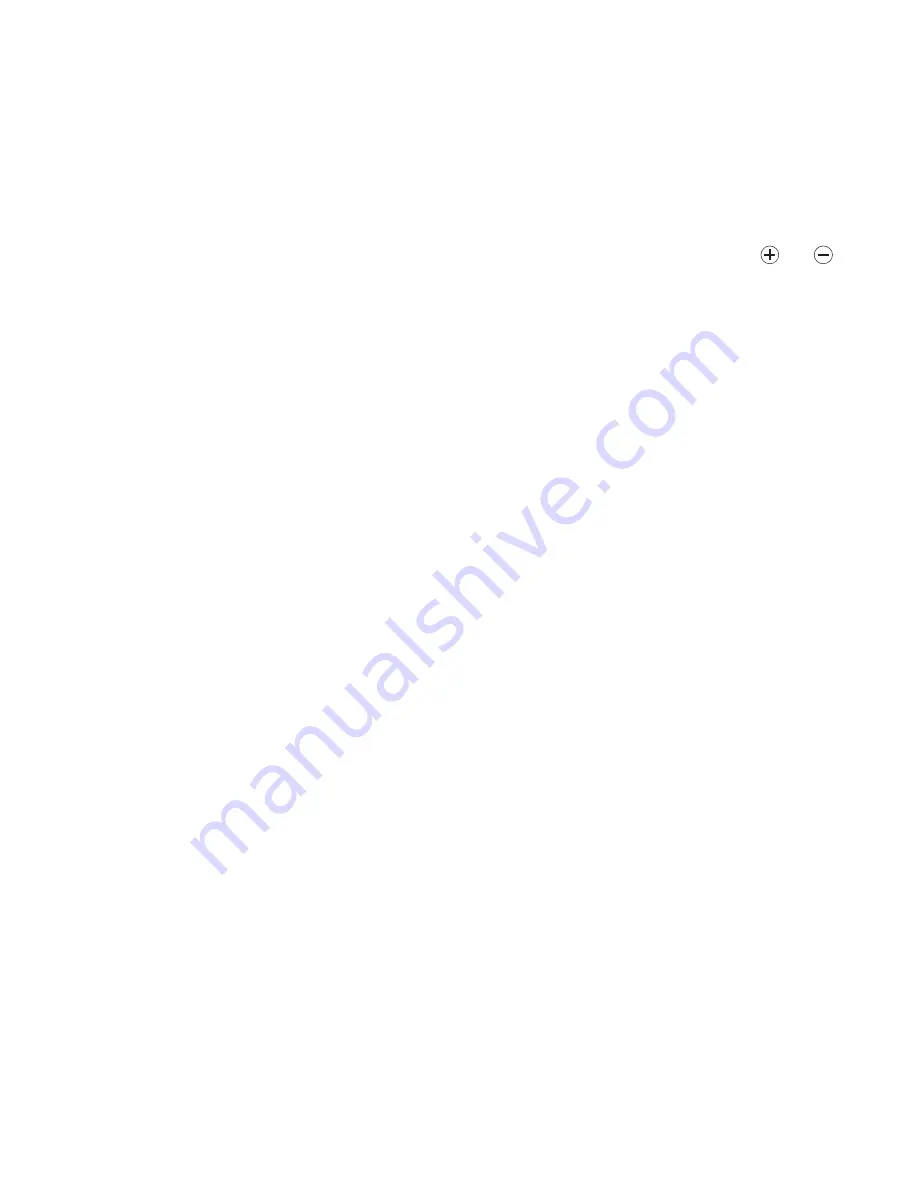
23
C. Explanation of Responses
1.
Zero Calibration:
If the display is not reading 0.0 PPM in air, then adjust the zero calibration.
Refer to Section II.C.5 and Figure 10.
2.
Calibration Cap:
The calibration cap is installed for protection of the sensor during shipping
and storage, but must be removed upon installation. If the sensor cap is not removed, then there
will be no response or a very slow response. Refer to Section I.B.3 and Figure 2.
3.
Span Calibration:
If the span calibration is performed incorrectly (usually accidentally done in
air with zero target gas) then this will cause the readings to be inaccurate. Unless you intend to
perform the span calibration and have a span gas calibration kit, do not touch the
and
keys
if you enter the span calibration screen. See Section II.C.8 and Figures 7 and 8.
4.
Sensor Wiring:
If the display is reading a negative value and giving an “Alarm Status: Error”
message, then the sensor may not be connected to the monitor. Check the wiring from the circuit
board in the monitor to inside the sensor enclosure. See Figures 5 and 6.
5.
Sensor Replacement:
Repeated or excessive exposure to the target gas and/or cross sensitive
gases will eventually cause failure of the sensor. If water is allowed to contact the sensor element
this will also eventually cause failure of the sensor. Under normal circumstances a sensor life is
typically 2 years or more. However, lightning, other power surges, chemical leaks, and contact
with water can all cause sensor failure. Replacement sensors are easily installed with the quick
disconnect fi tting.
6.
Damaged Circuit Board:
The circuit boards can be damaged if high voltage is connected to the
wrong terminals, by lightning, other power surges, or by corrosion. If you believe that the circuit
board is damaged, then contact the factory and your local sales representative. Refer to Figures
3, 4, 5, and 6.
7.
Power Supply:
If the display board has no power, then always check to see if the power supply
board is damaged and replace if necessary.