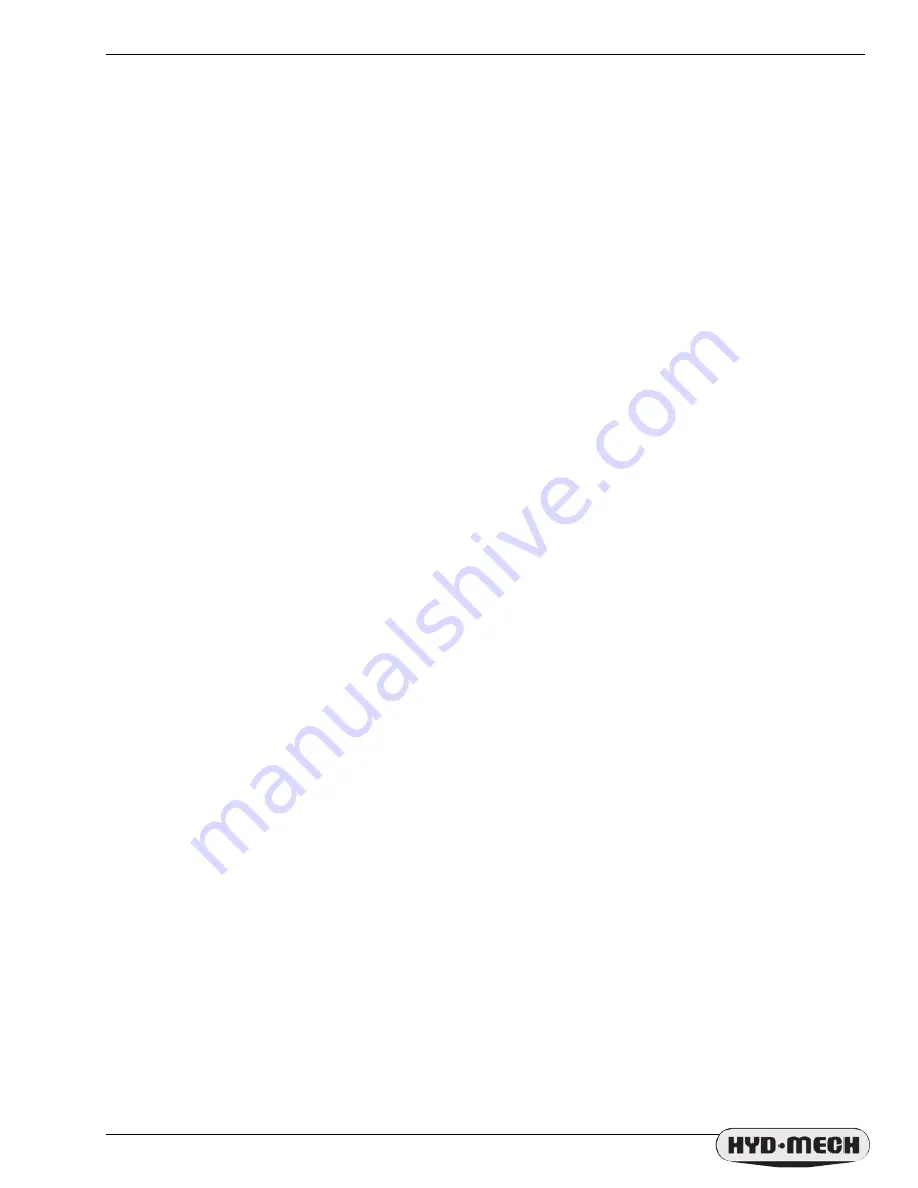
Pg 2.3
H40
CONVEYOR SELECTOR
Three maintained positions : OUTFEED, BOTH, and
SWITCH
INFEED. Selects the conveyor(s) to move when the
CONVEYOR FORWARD or REVERSE PUSH BUTTONS are
used.
CONVEYOR FORWARD
Depressing pushbutton causes selected conveyor's
PUSHBUTTON
rollers to rotate in a direction which would move material forward from
behind the saw head toward the front of the machine. Releasing the
pushbutton deactivates conveyor motor(s) and movement will stop.
CONVEYOR REVERSE
Depressing pushbutton causes selected conveyor's rollers
PUSHBUTTON
to rotate in a direction which would move material toward
the back of the machine. Releasing the pushbutton
deactivates conveyor motor's and movement will stop.
CONVEYOR SPEED
Allows for increase or decrease in speed of selected
RHEOSTAT
conveyor(s) when FORWARD or REVERSE pushbuttons
are depressed.
BLADE SPEED
Allows for increase or decrease of blade speed while
RHEOSTAT
blade motor is running.
DIGITAL READOUT
Readout displays screens featuring :
i) SFM - blade speed reading in surface feet per minute
FR - head feed rate in inches per minute
ii) HT - height of the head above the table
(lower limit switch)
iii) TIME ELP -
cutting elapsed time
TIME REM -
cut time remaining before reaching
head down limit.
The screens may be scrolled through by using the + or -
cursor key on the face of the display.
Содержание H-40
Страница 1: ...I N B A N D S A W T E C H N O L O G Y OPERATIONS MAINTENANCE M A N UA L ...
Страница 3: ...THIS PAGE INTENTIONALLY LEFT BLANK ...
Страница 6: ...SECTION 1 INSTALLATION SECTION 1 INSTALLATION ...
Страница 7: ...SECTION 1 INSTALLATION ...
Страница 13: ...THIS PAGE INTENTIONALLY LEFT BLANK ...
Страница 14: ...SECTION 2 OPERATING INSTRUCTIONS SECTION 2 OPERATING INSTRUCTIONS ...
Страница 15: ...SECTION 2 OPERATING INSTRUCTIONS ...
Страница 19: ...THIS PAGE INTENTIONALLY LEFT BLANK ...
Страница 25: ...THIS PAGE INTENTIONALLY LEFT BLANK ...
Страница 29: ...THIS PAGE INTENTIONALLY LEFT BLANK ...
Страница 30: ...SECTION 3 MAINTENANCE AND TROUBLE SHOOTING SECTION 3 MAINTENANCE AND TROUBLE SHOOTING ...
Страница 31: ...SECTION 3 MAINTENANCE AND TROUBLE SHOOTING ...
Страница 39: ...Pg 3 8 H40 DATE SERVICED BY COMMENTS SERVICE RECORD NOTES ...
Страница 40: ...SECTION 4 ELECTRICAL SYSTEM SECTION 4 ELECTRICAL SYSTEM ...
Страница 41: ...SECTION 4 ELECTRICAL SYSTEM ...
Страница 47: ...Pg 4 6 H28 32 ...
Страница 48: ...Pg 4 7 H28 32 ...
Страница 49: ...Pg 4 8 H28 32 ...
Страница 50: ...Pg 4 9 H28 32 ...
Страница 51: ...Pg 4 10 H28 32 ...
Страница 52: ...Pg 4 11 H28 32 ...
Страница 53: ...Pg 4 12 H28 32 ...
Страница 54: ...Pg 4 13 H28 32 ...
Страница 55: ...Pg 4 14 H28 32 ...
Страница 56: ...Pg 4 15 H28 32 ...
Страница 57: ...THIS PAGE INTENTIONALLY LEFT BLANK ...
Страница 58: ...SECTION 5 HYDRAULIC SYSTEM SECTION 5 HYDRAULIC SYSTEM ...
Страница 59: ...SECTION 5 HYDRAULIC SYSTEM ...
Страница 62: ...THIS PAGE INTENTIONALLY LEFT BLANK ...
Страница 63: ...Pg 5 4 H28 32 ...
Страница 64: ...Pg 5 5 H28 32 ...
Страница 65: ...Pg 5 6 H28 32 ...
Страница 66: ...Pg 5 7 H28 32 ...
Страница 67: ...THIS PAGE INTENTIONALLY LEFT BLANK ...
Страница 68: ...SECTION 6 MECHANICAL ASSEMBLIES SECTION 6 MECHANICAL ASSEMBLIES ...
Страница 69: ...SECTION 6 MECHANICAL ASSEMBLIES ...
Страница 82: ...THIS PAGE INTENTIONALLY LEFT BLANK ...
Страница 83: ...Pg 6 14 H28 32 ...
Страница 84: ...Pg 6 15 H28 32 ...
Страница 85: ...Pg 6 16 H28 32 ...
Страница 86: ...Pg 6 17 H28 32 ...
Страница 87: ...THIS PAGE INTENTIONALLY LEFT BLANK ...
Страница 88: ...SECTION 8 SPECIFICATIONS SECTION 8 SPECIFICATIONS ...
Страница 89: ...SECTION 8 SPECIFICATIONS ...
Страница 91: ...Pg 8 2 H4040 2000 LAYOUT DRAWING ...
Страница 92: ...SECTION 9 WARRANTY SECTION 9 WARRANTY ...
Страница 93: ...SECTION 9 WARRANTY ...