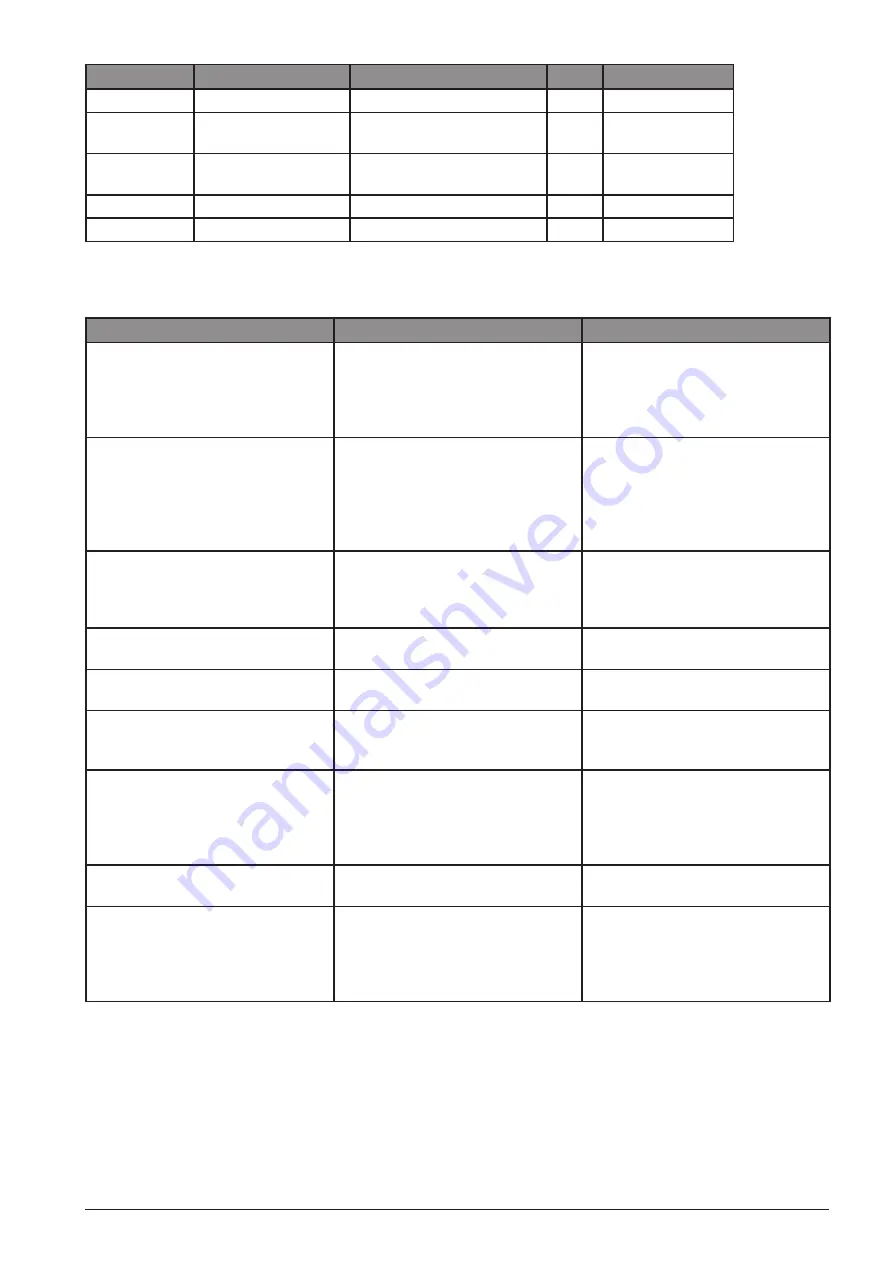
8
CHANGES AND T YPING ERRORS RESERVED
CHANGES AND T YPING ERRORS RESERVED
Indication
Composant/objet
Fabricant
PCS
Motor
Motor
AC250V/1PH/400W
1
SB1
SB2
Magnetic switch
250VAC/16A
1
KJD12
SB3
Push button-
Emergency Stop
250VAC/12A
1
HY57B
SB4
Micro switch
250VAC/16A
1
KW-7-3B
SB5
Micro switch
250VAC/16A
1
KW7
11. T
roUblesHooTinG
Trouble
Probable couse
Remedy
Noisy Operation
1.Incorrect belt tension.
2.Dry Spindle.
3.Loose spindle pulley
4.Loose motor pulley
1.Adjust tension.
2.Lubricate spindle.
3.Checking tightness of retaining nut
on pulley, and tighten if necessary.
4.Tighten setscrews in pulleys.
Drill bit burns
1.Incorrect speed.
2.Chips not coming out of hole.
3.Dull drill bit
4.Feeding too slow
5.Not lubricated
1.Change speed.
2.Retract drill bit frequently to clear
chips.
3.Resharpen drill bit.
4.Faster the speed.
5.Lubricate drill bit.
Drill bit leads off…
hole not round
1.Hard grain in wood or
lengths of cutting lips
and/or angles not equal
2.Bent drill bit
1.Resharpen drill bit correctly.
2.Replace drill bit.
Wood splinters on
underside
1.No “back up material” under
workpiece.
1.Use “back-up material”
Workpiece turn loose from hand
1.Not supported or clamped
properly.
1.Support working or clamp it.
Drill bit binds in
workpiece
1.Workpiece pinching drill bit
or excessive feed pressure.
2.Improper belt tension.
1.Support working or clamp it.
2.Adjust temsion.
Excessive drill bit runout or wobble
1.Bent drill bit
2.Worn spindle bearings.
3.Drill but not properly
installed in chuck
4.chuck not properly installed.
1.Use a straight drill bit.
2.Replace bearings.
3.Install drill bit properly.
4.Install chuck properly.
Quill Returns too
slow or too fast
1.Spring has improper tension.
1.Adjust spring tension.
Chuck will not stay atached to
spindle if falls off when trying to
install it.
1.Dirty,grease,or oil on the tapered
inside surface of chuck or on the
spindles tapered surface.
1.Using a household detergent clean
the tapered surface of the chuck and
spindle to remove all dirt,grease and
oil.
Содержание HU 13-2 N
Страница 1: ...HU 13 2 N D R I L L I N G M A C H I N E ...
Страница 5: ...5 LIST OF LOOSE PARTS IN THE BOX AND BAGS ...
Страница 6: ...6 CHANGES AND TYPING ERRORS RESERVED 6 GETTING TO KNOW YOUR DRILL PRESS ...
Страница 9: ...9 CHANGES AND TYPING ERRORS RESERVED 12 EXPLODED DRAWING AND PARTS LIST ...
Страница 12: ...2017 V1 Copyright Huberts BV All rights reserved ...