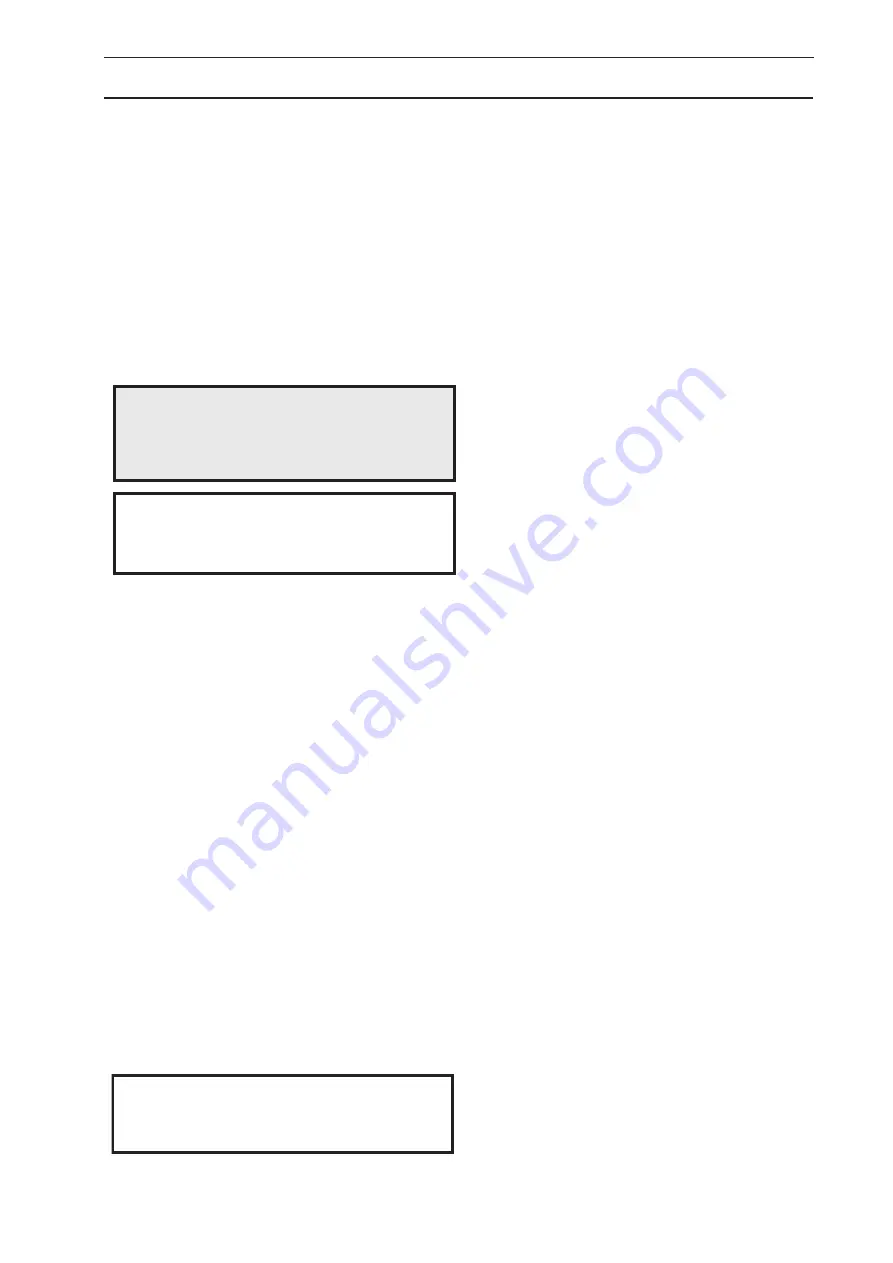
English-
3
SAFETY INSTRUCTIONS
Safety Instructions
General Instructions
This workshop manual is written for personnel with
general knowledge about the repair and service of
riders.
The workshop where the rider is to be repaired
must be equipped with safety equipment in
accordance with local bylaws.
No one may repair the rider unless they have read
and understood the content of this workshop
manual.
The machine is tested and approved only with the
equipment originally provided or recommended by
the manufacturer.
This workshop manual contains the following
boxes in relevant places.
Special Instructions
The fuel used in the rider has the following
hazardous properties:
•
The fluid and its vapour are poisonous.
•
Can cause eye and skin irritation.
•
Can cause breathing problems.
•
Is highly inflammable.
When using compressed air, do not direct the jet
towards the body. Air can penetrate into the blood
circulation system, which entails mortal danger.
Use eye protection when working with tensioned
springs.
Wear protective earplugs or earmuffs when test
running.
After test running, do not touch the muffler until it
has cooled. Risk of burns. This is especially true if
the rider is equipped with a catalytic converter. The
coatings on and in the catalytic converter element
are hazardous to ingest. Use protective gloves
when working with the converter/muffler.
The blades are sharp and can cause cuts and
gashes. Use protective gloves when handling the
blades.
Use eye protection when working with the cutting
unit. The belt tensioning spring can break, fly off,
and could cause personal injury.
Use eye protection when working with the battery
with the plugs removed. Be especially careful
when handling battery acid. Acid on the skin can
cause serious corrosive injuries. In the event of
spillage on the skin wash immediately with water.
Acid in the eyes can cause blindness; contact a
doctor immediately.
Be careful when servicing the battery. Explosive
gases form in the battery. Never perform
maintenance on the battery while smoking or in
the vicinity of open flames or sparks. This can
cause the battery to explode and cause serious
injuries.
WARNING!
The warning box warns of the risk
of personal injury if the
instructions are not followed.
IMPORTANT INFORMATION
This box warns of material damage if the
instructions are not followed.
!
IMPORTANT INFORMATION
Waste oil and old filters shall be handled
as hazardous waste.
Содержание Rider 13 AWD
Страница 1: ...Workshop manual Rider 13 AWD Rider 175 AWD Rider 15V2 AWD English ...
Страница 2: ......
Страница 25: ...English 23 DELIVERY AND DEALER SERVICE ...
Страница 35: ...English 33 DESIGN AND FUNCTION ...
Страница 116: ...English 114 REPAIR INSTRUCTIONS ...
Страница 118: ...English 116 ELECTRICAL SYSTEM 8009 679 Wiring diagram AWD ...
Страница 126: ...English 124 HYDRAULIC SYSTEM ...
Страница 133: ......
Страница 134: ...2008W12 115 03 16 26 ...