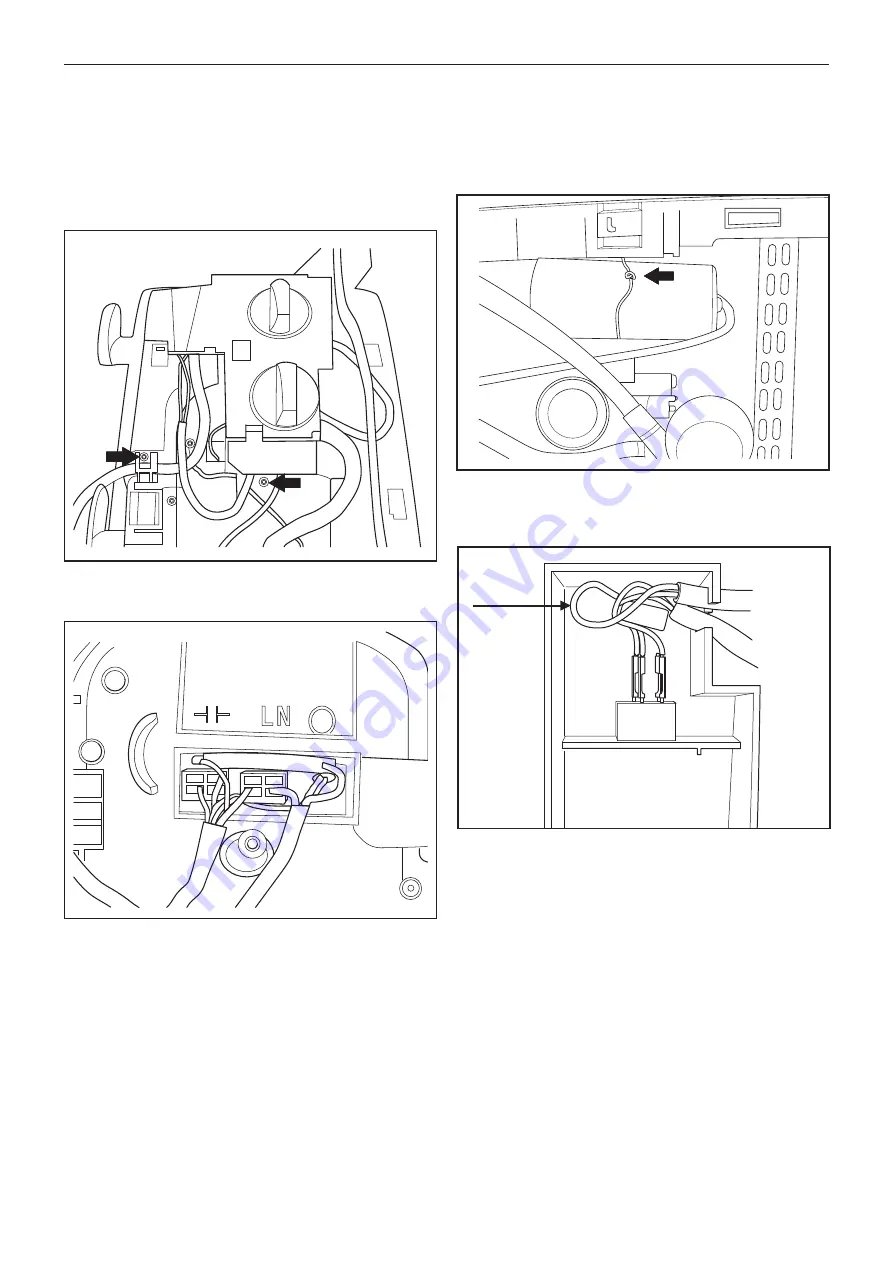
8 – English
2.3 To disassemble/assemble the
switchbox and motor cover
1. Remove the 1 torx TX20 screw from the cable relief
and 1 torx TX20 screw from the electrical box.
2. Remove the motor plug, capacitor plug and ground
cable.
3. Assembly: Fix the capacitor with a cable tie. Make
sure that the marking is visible. Make sure that the cable
tie is placed correctly, see the arrow in the figure below.
4. Install the cables and wires correctly, see the figure
below. Make sure that the ground cable is installed
correctly, placed around the tube. See the figure below.
Repair instructions