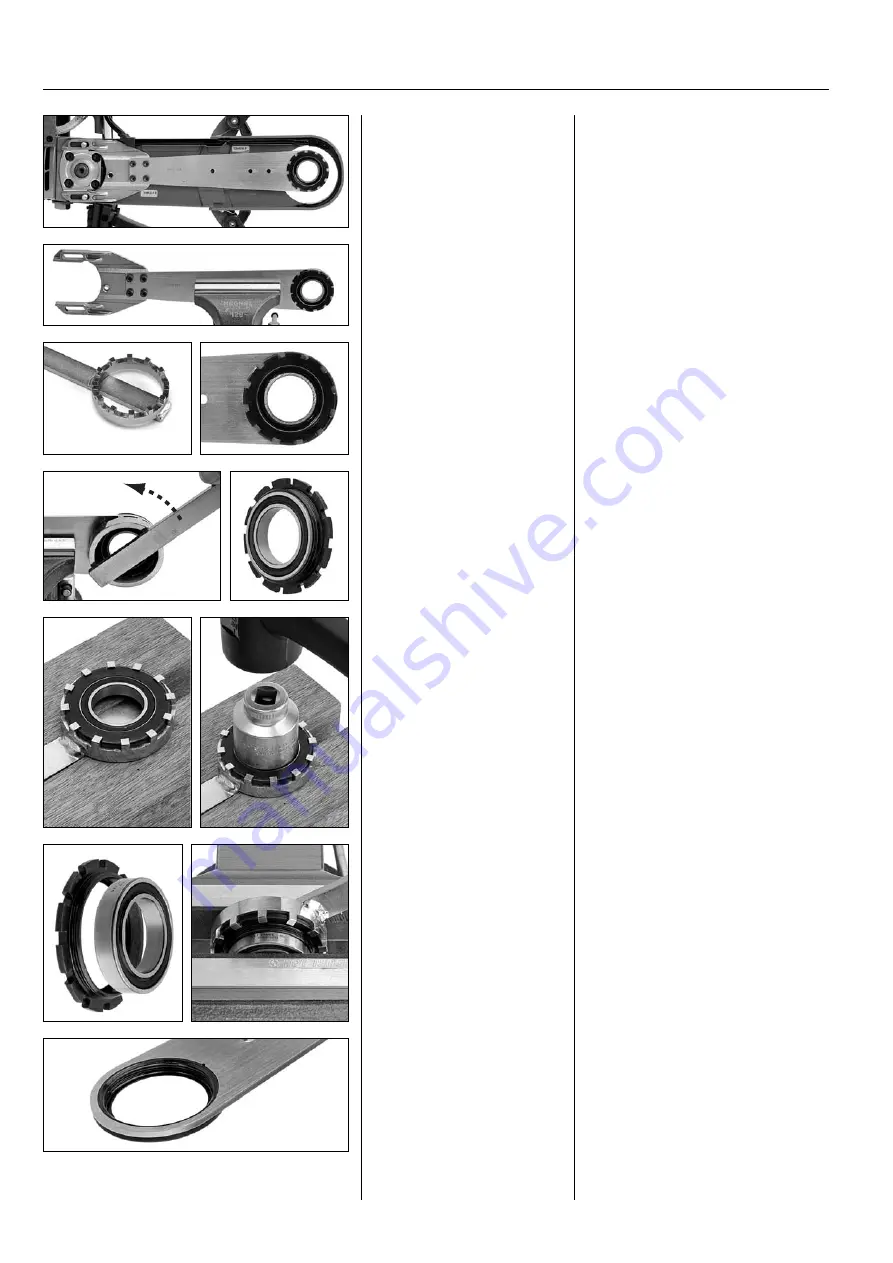
28
CUTTING UNIT – Cut-n-Break
18
Fit the bearing
The bearing is best fitted by pressing.
Apply press force to the bearing's outer
ring.
Alternatively you can fit the bearing
using a vice as shown in the illustration.
Place the bearing holder in the special
tool to give the bearing holder good
support all around.
Fit the bearing
The bearing is best fitted by
pressing.
Alternatively you can fit the
bearing using a vice. Place the
bearing holder in the special
tool.
Tools
The special tool 502 53 15-01 is needed
for removal which is used to remove and
fit the threaded bearing holder.
Attach the cutting arm in a vice.
Attach the cutting arm.
Remove the bearing holder
Remove the bearing holder using tool
502 53 15-01. The bearing holder has a
fine thread.
Remove the bearing
Also use the special tool to press the bea-
ring out of the holder. Support the tool
ring with a pair of wood blocks as shown
in the illustration. Press or knock out the
bearing using a suitable socket.
Tools
The special tool 502 53 15-01 is
needed for removal.
Bearing replacement
The cutting arm, where the bearing is
fitted, is now accessible when the belt
guards are removed. See the “Belt replace-
ment” chapter where this work is
described.
Bearing replacement
Remove the belt guards.
Remove the bearing holder
Remove the bearing holder
using tool 502 53 15-01.
Remove the fixed bearing
holder
The bearing holder in the cutting
arm is positioned with a force
fit.
The following method for
removal works:
Remove the bearing
Support the tool ring as shown
in the illustration. Press or
knock out the bearing using a
suitable socket.
502 53 15-01
Remove the fixed bearing holder
The bearing holder in the cutting arm is
positioned with a force fit. It is difficult
to remove as there is no chance of achie-
ving a good counter hold
The following method works: