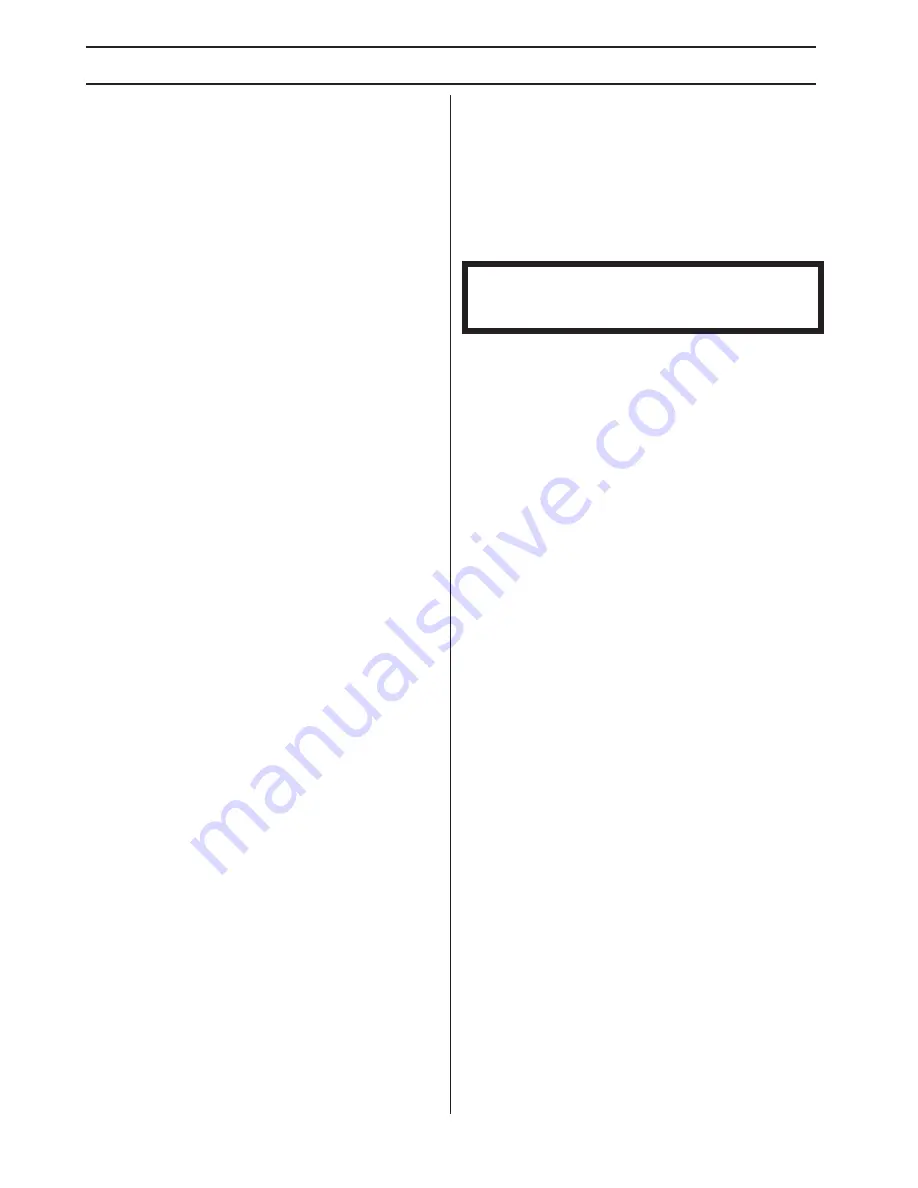
SAFETY INSTRUCTIONS
24 – English
Maintenance and service
Most accidents involving machines occur during trouble
shooting, service and maintenance as staff have to locate
themselves within the machine’s risk area. Prevent
accidents by being alert and by planning and preparing
the work. You can also refer to 'Preparations for
maintenance and service” in the 'Maintenance and
service” section.
•
Never carry out repairs without having the necessary
expertise.
•
The user must only carry out the maintenance and
service work described in this manual. More extensive
work must be carried out by an authorized service
workshop.
•
Use personal protective equipment as well as
equipment to mechanically secure machine
components during maintenance and service.
•
Only trained service personnel are permitted to
intervene in the electrical or hydraulic systems.
•
Set out clear signs to inform persons in the vicinity that
maintenance work is in progress.
•
If service operations or trouble shooting does not
require the machine to be switched on, the power
cable must be removed and positioned so that it
cannot be connected by mistake.
•
Ensure there is no current to the machine by removing
the power cable before opening or removing the
electric cabinet or any other component that contains
electrical current.
•
Pipe and hose couplings can remain pressurized
despite the motor being switched off and the power
cable disconnected. It must always be assumed that
hydraulic hoses are pressurized and they must be
opened with great care. Relieve the pressure on the
arm system by resting it on the ground and turn off the
electric motor before undoing the hoses.
•
Never try to stop hydraulic oil leaking from a broken
hose by hand. Finely dispersed hydraulic oil at high
pressure can permeate under the skin and cause very
severe injuries.
•
When dismantling machine parts, heavy components
can start moving or fall down. Secure moving parts
mechanically before loosening screw joints or
hydraulic hoses.
•
Use an approved lifting device to secure and lift heavy
machine parts.
•
Several components heat up during use of the
machine. Do not commence any servicing or
maintenance tasks until the machine has cooled.
•
Keep work area clean and well lit.
Cluttered or dark
areas invite accidents.
•
The machine’s movements can be defective if a
terminal, cable or hose is incorrectly assembled.
Exercise caution during test runs and be prepared to
turn off the machine immediately in the event of a
fault.
External environmental factors
Temperature
The ambient temperature, both heat and cold, affects the
machine’s operational reliability. Temperature variations
also have an impact as they produce an increased risk of
condensation forming in the machine’s tank.
Heat
The maximum working temperature for hydraulic oil is
90
°
C (194
°
F). Overheating results in deposits forming in
the oil, leading to increased wear, damaged seals and
leakage. Overheated hydraulic oil provides poor
lubrication, resulting in inferior performance.
To avoid overheating:
•
Keep the machine clean, in particular its cooler.
•
Ensure that there is good ventilation when working
indoors.
•
Radiant heat can cause local heating that damages
parts of the machine. Screen off vulnerable
components.
•
Additional cooling is required if the ambient
temperatures is over 40
°
C (104
°
F). Supply the
machine with forced cooling using compressed air.
To avoid damage to the machine:
•
Change hydraulic fluid and filters more frequently.
•
Check the machine’s seals to prevent dirt in the
hydraulic system due to broken seals.
•
Rubber caterpillar tracks must not be exposed to
temperatures of over 70
°
C (158
°
F). In hotter
environments steel tracks have to be used.
Cold
Do not use maximum pump pressure if the hydraulic fluid
is less than 10
°
C (50
°
F). Allow the machine to warm up
slowly. Warm up the lower section by running the
caterpillar tracks, first slowly and then more quickly with
the outriggers extended. Move the upper section back
and forth and operate all cylinders in the arm system
without load. The machine is ready for use when its
temperature (hydraulic fluid) has risen to around 40
°
C
(104
°
F).
Moisture
When working in damp environments the operator should
ensure that electrical components, connectors for
example, are not submerged in water.
The machine must never be driven to such a depth in
water that it reaches up to the machine’s equipment. The
equipment can be damaged and the machine can be live,
resulting in personal injuries.
NOTICE! There is an increased risk of overheating in
warm environments. Both the machine’s hydraulic
system and electronic components can be damaged.
Содержание DXR-310
Страница 75: ...English 75 TECHNICAL DATA Range and transport diagram DXR250 4483 176 5 2020 79 5 4815 189 5 ...
Страница 77: ...English 77 TECHNICAL DATA DXR270 4483 176 1986 78 4849 191 1435 56 ...
Страница 79: ...English 79 TECHNICAL DATA DXR300 4868 192 2368 93 5231 206 1818 72 ...
Страница 81: ...English 81 TECHNICAL DATA DXR310 5182 204 2129 84 2678 105 5549 218 ...
Страница 84: ...1158619 27 z Z 78 z Z 78 2016 12 19 US Original instructions ...