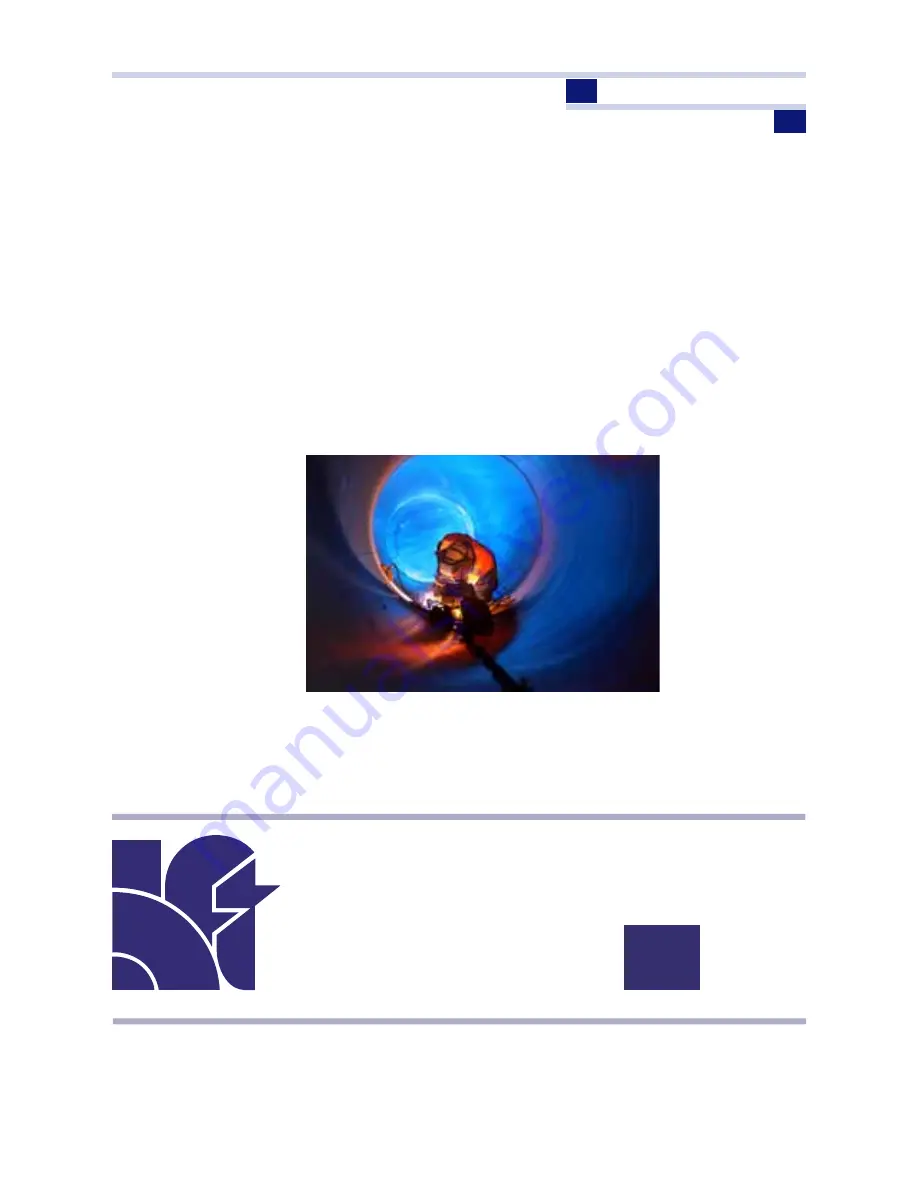
API0100 IP65 UI-91 12-10-2017 ME
© HFT
®
Stukeley Meadow BURRY PORT Carms SA16 OBU United Kingdom (UK)
Tel +44 (0) 1554 836 836 Fax +44 (0) 1554 836 837
www.huntingdonfusion.com Email [email protected]
E&OE Copyright © HFT
®
. All rights reserved.
This publication may not be reproduced by any means without the written permission of Huntingdon Fusion Techniques HFT
®
HUNTINGDON FUSION
TECHNIQUES HFT