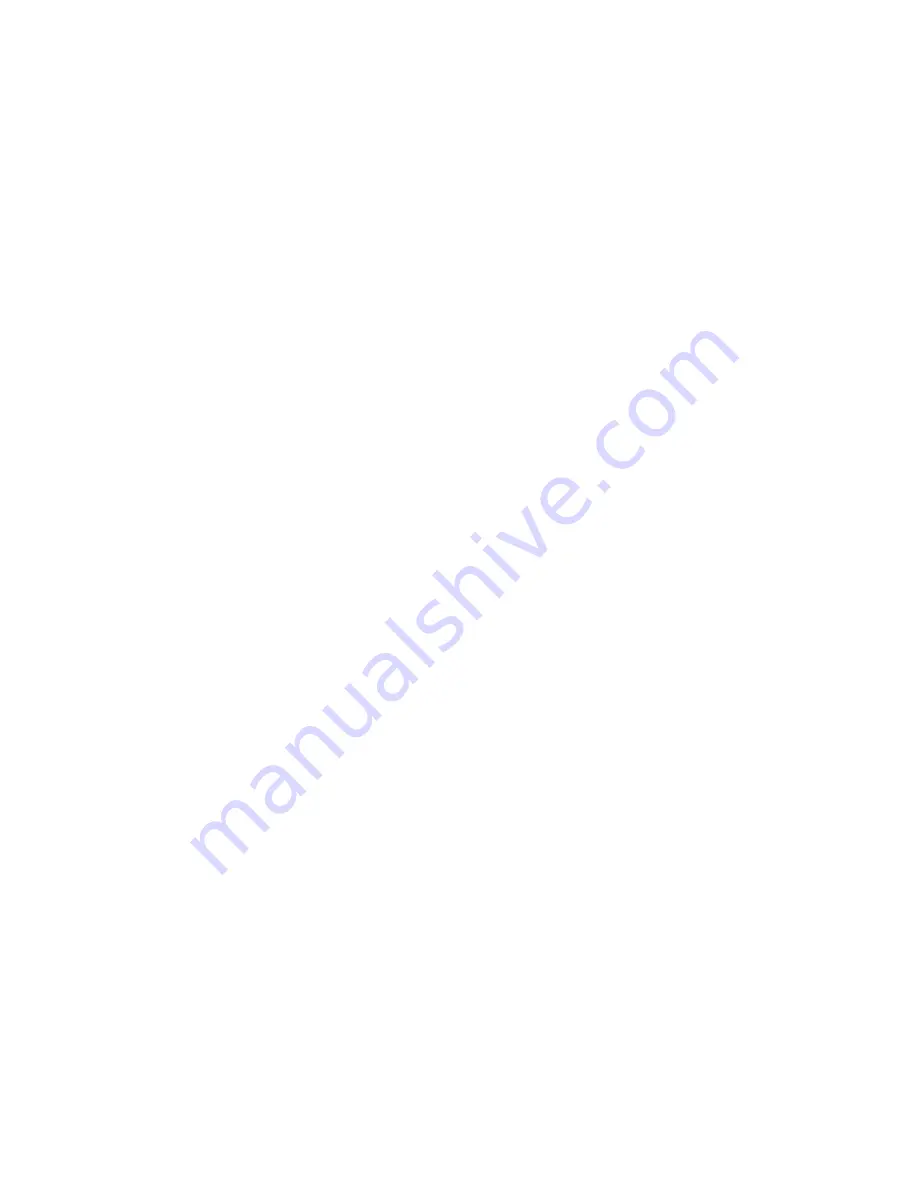
6.
If the Teflon is not replaced when showing signs of wear, the polythene
will stick and seal quality will deteriorate. Also the rubber pressure pad
will start to wear and if this is allowed to continue to the stage where
the surface of the pad is burnt and uneven, the resulting ‘air gap’
between the pad and element will reduce heat transfer and cause
further rapid deterioration of the Teflon. Excessive burning will
eventually result also in the element wire requiring replacement.
7.
To avoid this ‘ vicious circle’ always operate the machine at the
minimum heat setting consistent with satisfactory seal quality. Allow
sufficient cooling time between each successive seal. When sealing
repetitively at high frequency reduce the heating time from its original
setting to compensate for residual heat build up in the element.
8.
The microswitch is set to avoid application of power to the element until
the rubber pad is fully aligned and pressed closely to the Teflon to
allow the necessary heat transfer. The rubber pressure pad is
sufficiently pliable to accommodate several thickness’ of polythene, but
accidental closure onto thicker objects or attempting to seal bubble
pack material and heavy paper laminate gusseted materials will cause
deterioration of the Teflon for the reasons explained previously.
9.
The rubber pressure pad, and element wire strip are easily replaceable,
but care in operating and maintenance of the Teflon barrier tape can
extend the service interval before element reconditioning becomes
necessary.
10.
If the machine fails to seal, but the on-off switch and indicator lights
show that the power and timer circuits are operating correctly, unplug
the element and check the condition of the resistance wire and Teflon.
Simple replacement of these low cost consumable spares will normally
restore the full performance of the equipment.
Содержание HM2500
Страница 2: ......