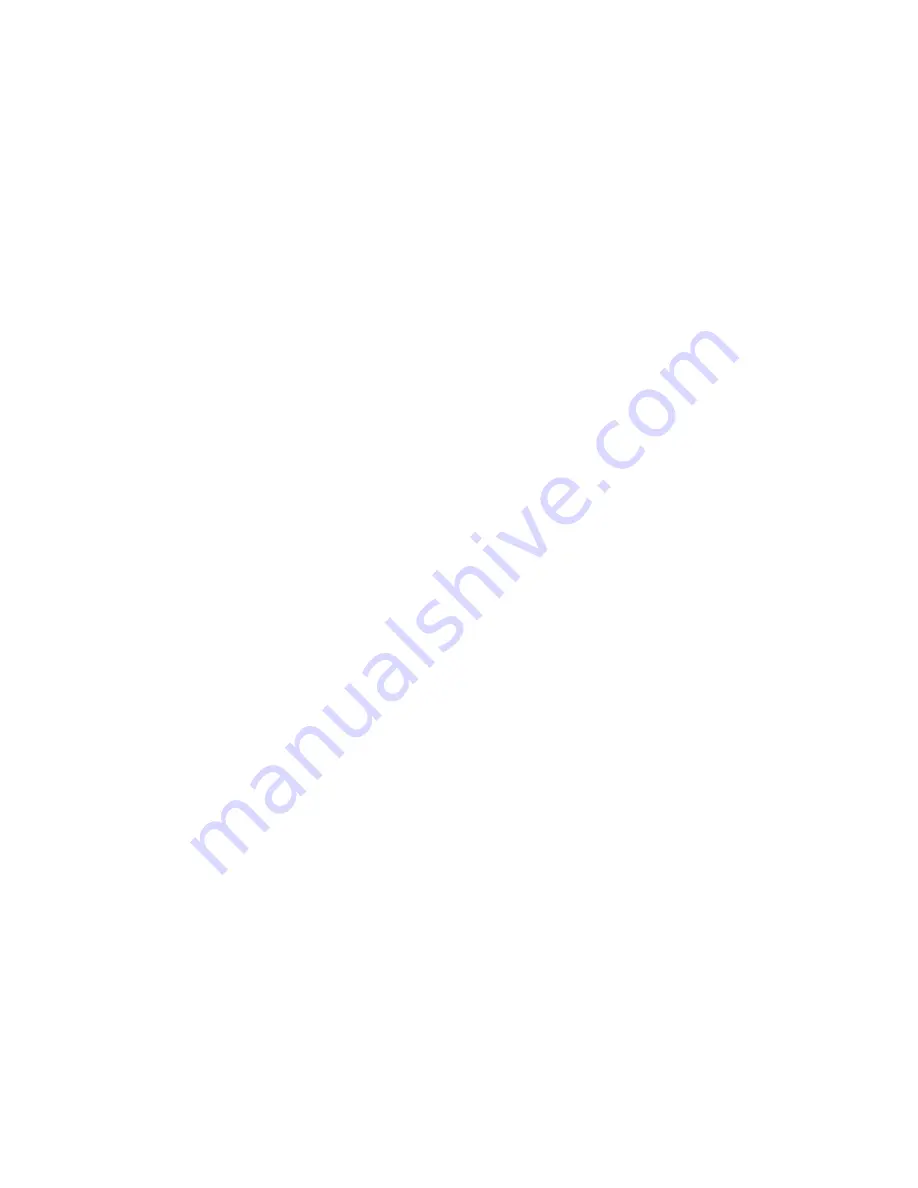
14
LP-542 REV. 6.2.16
Control
– The integrated control system monitors the system and responds to internal and external signals to regulate fan speed and
control boiler output. This allows the boiler to deliver only the amount of heat energy required and nothing more.
The control can be set up to monitor outdoor temperature through an outdoor sensor to regulate boiler set point temperature, increasing
overall system efficiency while providing great comfort. The system can be further enhanced by installing an indirect water heater to
provide domestic hot water.
The control can regulate the output of multiple boilers through its cascade system function by establishing one boiler as the master and
the other connected boilers as followers. The master boiler requires a sensor to provide feedback on set point temperature in order to
adjust heating output from the connected boilers. Through the use of multiple UFT boilers cascaded systems offer greater system
turndown and redundancy.
Electronic LCD Display
– The high resolution display allows the user to monitor boiler functions. The display also provides the means
to program the system parameters to maximize the efficiency of the system design.
Combustion System
(Blower
– Gas Valve – Mixer – Burner – Spark Ignition) – The highly efficient spark ignition combustion system
uses a variable speed blower to adjust combustion as the system requires more or less energy. The negative regulated gas valve
provides only the amount of fuel required to ensure clean combustion. The mixer accurately regulates the combination of gas and air
throughout the modulating range to ensure high reliability. The burner is constructed of durable ceramic metal fiber for long service life.
Boiler Sensors
(Return
– Supply – Flue - Outdoor) - Sensors provide highly accurate temperature monitoring to assure accurate
system control. These sensor inputs can be monitored through the boiler control system and display.
Pressure Gauge
– Allows the user to monitor system pressure.
System Safeties
– The boiler is provided with many safety features to ensure reliable and safe operation. Each safety is connected to
the boiler control. The boiler will alert the user if an unsafe condition occurs and needs to be addressed. The following are provided
safeties: Flue Pressure Switch (monitors flue pressure), Burner High Limit (monitors burner plate temperature), High Limit Water Switch
(monitors boiler water temperature), Low Water Sensor (monitors water level in the heat exchanger), optic flame sensor (monitors flame
quality), Flue Sensor (monitors flue temperature), Condensate Pressure Switch (monitors pressure to ensure condensation does not
back up into boiler).
Manual Air Vent
– Each boiler is equipped with an air vent to discharge air from the system during start–up.
Intake and Exhaust Adapters
– The boiler is equipped with adapters to ease connection to the vent system. The adapters are
provided with clamps and seals to secure field supplied piping, and test ports to ease monitoring of the combustion system. Each boiler
is supplied with a 6 inch piece of CPVC that must be connected into the exhaust vent adapter.
Boiler 1 ¼” Inlet and 1 ¼” Outlet Connection
– Boilers are equipped with both top and bottom piping connections for greater
installation flexibility.
Gas Connection
– The boiler is equipped with a ¾” gas connection to connect the incoming gas supply.
Field Wiring and Power Switch
– Each boiler is supplied with a power switch to cut off power. The boiler is also equipped with two
front mounted terminal strips. These terminal strips are separated into low and line voltage to ease system wiring.
Condensate Trap and Hose Assembly
– Each boiler has a built-in condensate trap to control the discharge of condensate produced
by the boiler during normal operation. A corrugated condensate hose is also provided to ensure proper drainage of condensate into the
pump or drain.
Low Water Cut Off Probe
– LWCO is provide with each boiler to assure the boiler has adequate water level to eliminate overheating
and even damaging the boiler heat exchanger .
Pump Service Mode
– Allows manual operation of pumps to commission system and check pump operation.
DHW Priority
– The boiler control allows connection of a DHW temperature sensor / aquastat to the low voltage terminal strip. When
the aquastat calls for heat, the module activates the DHW pump, shuts down the boiler and CH pumps, and immediately sets the target
outlet water temperature to 180
o
F (factory default). This provides automatic priority heat allocation to the indirect water heater for
maximum response and recovery. The DHW pump continues for 1 minute (factory default) after the heating cycle to deliver the most
possible heat.
DHW / Central Heating (CH) Rotation
– If a DHW call for heat is received while a central heating call is in progress, the control will
start the DHW pump and shut the boiler and CH pumps off. If the central heating call is still active while the DHW call is in operation,
the control will wait for 30 minutes (time adjustable by the installer) then switch back to the central heating demand. The control will
switch back and forth until one of the heat demands ends.
Содержание UFT-100W
Страница 47: ...47 LP 542 REV 6 2 16 Figure 38 Electrical Wiring Diagram ...
Страница 48: ...48 LP 542 REV 6 2 16 Figure 39 Ladder Diagram ...
Страница 87: ...87 LP 542 REV 6 2 16 ...
Страница 88: ...88 LP 542 REV 6 2 16 ...
Страница 89: ...89 LP 542 REV 6 2 16 MAINTENANCE NOTES ...