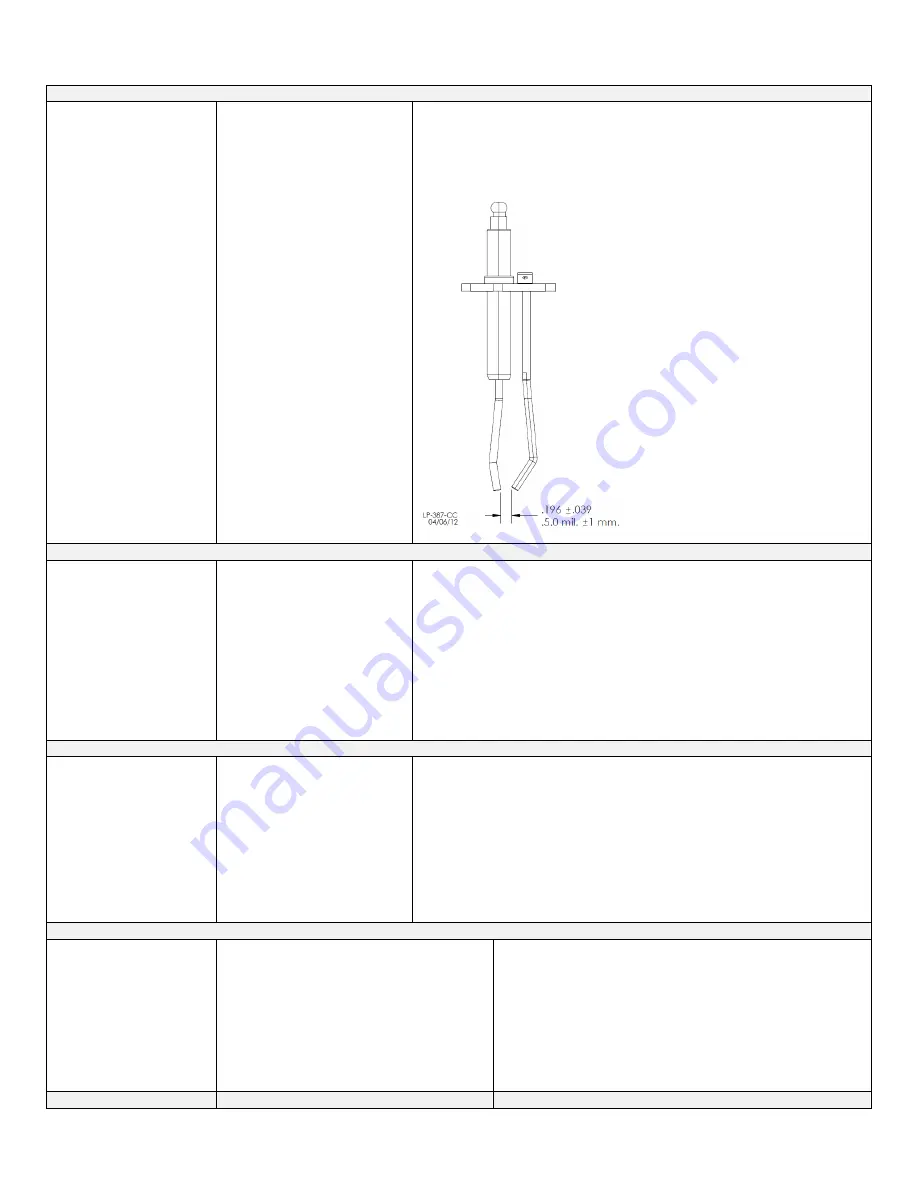
76
LP-387 REV. 12.15.14
Fault Code F09
NO FLAME ON IGN F09
PUMP ON
The boiler tried to ignite four
times during one heat call and
failed. The red FAULT light and
LOCKOUT will flash on the
display. This code indicates a
serious safety issue. The boiler
will not restart until the cause of
ignition failure is repaired by a
technician and he pushes the
RESET button on the display.
During this lockout fault, the
pump will remain on as indicated
on the second line of the display.
1. Watch the igniter through the observation window provided.
2. If there is no spark, check the spark electr
ode for the proper .156” (3.96 mm)
gap (See Figure 34).
3. Remove any corrosion from the spark electrode and flame rectifier probe.
4. If there is a spark but no flame, check the gas supply to the boiler.
5. If there is a flame, check the flame sensor.
6. Check any flue blockage or condensate blocks.
Figure 34
– Proper Electrode Spacing
Fault Code F10
FLAME LOSS F10
The flame was lost while the
boiler was firing 3 times during 1
demand call. The red light will
display and the word LOCKOUT
will flash. This code indicates a
serious safety issue. The boiler
will not restart until the cause of
flame loss is determined by a
technician and he pushes the
RESET button on the display.
During this lockout fault, the
pump will be on as indicated on
the second line of the display.
1. Monitor the gas pressure to the boiler while in operation.
2. Assure that the flame is stable when lit.
3. Check to see if the dis
play readout changes from “GAS VALVE ON” to “RUN”
within a few seconds after the boiler ignites.
4. Check the FLAME signal on the status display. It should be above 1.0 when the
boiler is firing.
5. If the signal reads less than 1 microampere, clean the flame rectifier and spark
probe.
6. If the problem persists and the ‘FLAME” signal is still less than 1.0, replace the
flame probe and spark igniter probe.
7. The flame signal should be steady after the boiler has been firing for 1 minute
and is normally at 5.0 to 9.0. If the flame signal is not steady, disassemble the
burner door and check the burner and its sealing gaskets.
Fault Code F11
FALSE FLAME SIG F11
PUMP ON
There is flame when the control is
not telling the boiler to run. The
red light will display and the word
LOCKOUT will flash. This code
indicates a serious safety issue.
The boiler will not restart until the
cause is determined by a
technician and he pushes the
RESET button on the display.
During this lockout fault, the
pump will be on as indicated on
the second line of the display.
1. Look into window. If there is flame, turn the gas off to the boiler at the service
valve and replace the gas valve.
2. If the flame signal on the status menu is greater than 1.0 when the burner is not
lit, replace the spark igniter and the flame rectification probe.
3. If the flame return sensor is not present after turning off the gas supply, check
the gas valve electrical connection.
4. Repair condensate system as necessary. If condensate has backed up and
partially filled the combustion chamber, the refractory wall may be damaged and
should be replaced.
5. Turn the gas on at the service valve after corrective action is taken.
6. If the refractory wall falls against the rectifier probe, it may conduct the signal to
ground, giving a false reading.
Fault Code F13
FAN SPEED ERROR
F13
PUMP ON
The fan is not running at the speed that the con-
trol has commanded it to run at. The fan speed
had been more than 30% faster or slower than
the commanded speed for more than 10 sec-
onds. The red light will display and the word
LOCKOUT will flash. This code indicates a
serious safety issue and the boiler will not restart
until the cause is determined by a technician and
he pushes the RESET button on the display.
During this lockout fault, the pump will be on as
indicated on the second line.
1. Check the combustion air fan wiring.
2. Measure the DC voltage from the red fan wire to ground while it
is connected to the fan. It should be between 24 to 40 volts. If it is
lower than 24 volts, check for excessive external loads connected to
the boiler sensor terminals. Disconnect the 5 pin plug from the fan
and check the voltage on the red wire again. If it is now between 24-
40 volts, replace the fan. If it is still below 24 volts replace the boiler
control board.
Содержание EFT-110
Страница 14: ...14 LP 387 REV 12 15 14 SPECIFICATIONS AND DIMENSIONS Figure 2 LP 387 K ...
Страница 24: ...24 LP 387 REV 12 15 14 Figure 8 Piping Symbol Legend ...
Страница 58: ...58 LP 387 REV 12 15 14 Figure 32 Cascade Master and Follower Wiring ...
Страница 59: ...59 LP 387 REV 12 15 14 Figure 33 Internal Connection Diagram LP 293 J ...
Страница 82: ...82 LP 387 REV 12 15 14 EFT 55 80 110 PARTS BREAKDOWN Figure 36 Replacement Parts LP 387 J ...
Страница 84: ...84 LP 387 REV 12 15 14 EFT 155 199 285 399 PARTS BREAKDOWN Figure 38 Replacement Parts LP 387 KK ...
Страница 88: ...88 LP 387 REV 12 15 14 ...
Страница 89: ...89 LP 387 REV 12 15 14 ...
Страница 90: ...90 LP 387 REV 12 15 14 MAINTENANCE NOTES ...