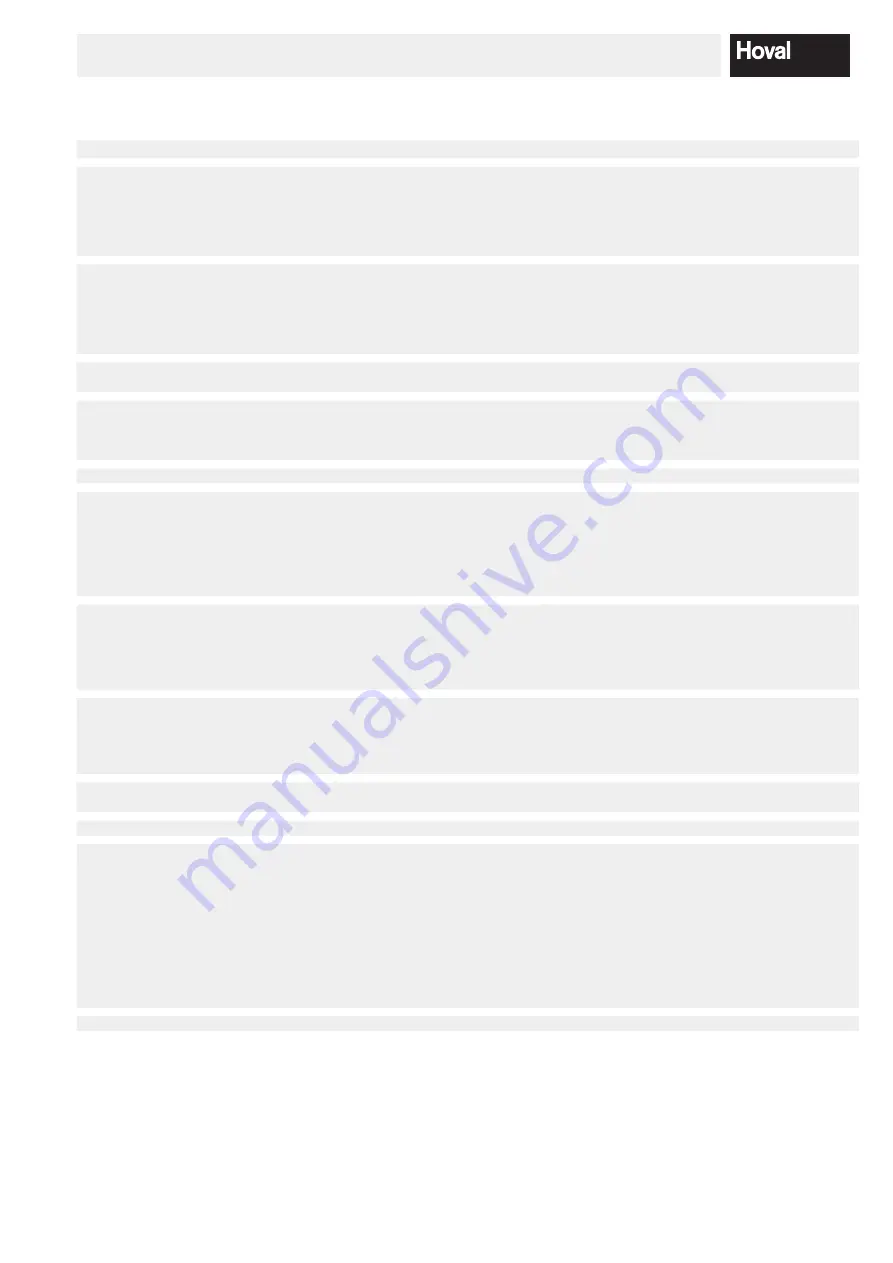
17
4 217 901 / 02
TECHNICAl INFORMATION
3.3
UltraGas
®
(1550) technical data
Type
(1550)
• Nominal heat output at 80/60°C, natural gas
kW
298-1472
• Nominal heat output at 40/30°C, natural gas
kW
328-1550
• Nominal heat output 80/60 °C, propane
2)
kW
-
• Nominal heat output 40/30 °C, propane
2)
kW
-
• Nominal heat input with natural gas
1)
kW
303-1518
• Nominal heat input with propane
2)
kW
-
•
Operating pressure heating min./max. (PMS)
bar
1/6
•
Max. operating temperature (T
max
)
°C
90
• Boiler water content (V
(H20)
)
l
966
• Flow resistance boiler
See diagram
•
Minimum circulation water quantity
l/h
-
• Boiler weight (without water capacity, incl. casing)
kg
2300
•
Boiler efficiency at full load at 80/60 °C (NCV / GCV)
%
97.2/87.7
•
Boiler efficiency at 30% partial load operation (EN 15502) (NCV / GCV)
%
107.9/97.4
• NOx class (EN 15502)
6
• Nitrogen oxide emissions (EN 15502) (GCV)
NOx
mg/kWh
31
• CO
2
content in exhaust gas at min./max. output
%
8.6/8.8
• Heat loss in standby mode
Watts
1600
• Dimensions
See dimensional drawing
•
Gas flow pressure min./max.
Natural gas E/LL
mbar
17.4-80
Liquefied gas
mbar
-
• Gas connection values at 15 °C/1013 mbar:
Natural gas E - (Wo = 15.0 kWh/m
3
) NCV = 9.97 kWh/m
3
m
3
/h
30.4-152.3
Natural gas LL- (Wo = 12,4 kWh/m
3
) NCV = 8.57 kWh/m
3
m
3
/h
35.4-177.1
Propane (NCV = 25.9 kWh/m
3
)
m
3
/h
-
• Operating voltage
V / Hz
1x230/50
3x400/50
• Electrical power consumption min./max.
Watts
271/4111
• Standby
Watts
9
• Type of protection
IP
20
• Permitted ambient temperature during operation
°C
5-40
• Sound power level
Heating noise (EN 15036 Part 1) (room air dependent)
dB (A)
86
Exhaust gas noise radiated from the mouth
(DIN 45635 Part 47) (room air dependent/room air independent)
dB (A)
-
Sound pressure level (depending on installation conditions)
3)
-
• Condensate quantity (natural gas) at 40 / 30°C
l/h
138
• pH value of the condensate
approx.
4.2
• Design
B23P, C53, C63
• Exhaust gas system
Temperature class
T120
Exhaust gas mass flow at nominal heat input (dry)
kg/h
2300
Exhaust gas mass flow at lowest heat input (dry)
kg/h
456
Exhaust gas temperature at nominal output and operation at 80/ 60 °C
°C
69
Exhaust gas temperature at nominal output and operation at 40/30 °C
°C
48
Exhaust gas temperature at lowest nominal heat load and operation 40/30 °C °C
32
Maximum permitted temperature of the combustion air
°C
50
Volume flow of combustion air
Nm
3
/h
1885
Maximum supply pressure for supply air and exhaust gas line
Pa
130
Maximum draught/underpressure at exhaust gas outlet
Pa
-50
• Heat loss in standby mode
%
0.11
1)
Figures relate to NCV. The boiler series is tested for EE/H setting. With a factory setting to a Wobbe value
of 15.0 kWh/m
3
, operation in the Wobbe value range from 12.0 to 15.7 kWh/m
3
is possible without resetting.
2)
Figures relate to NCV
.
3)
Compare notes for planning.
Содержание UltraGas 1550
Страница 47: ...47 4 217 901 02...