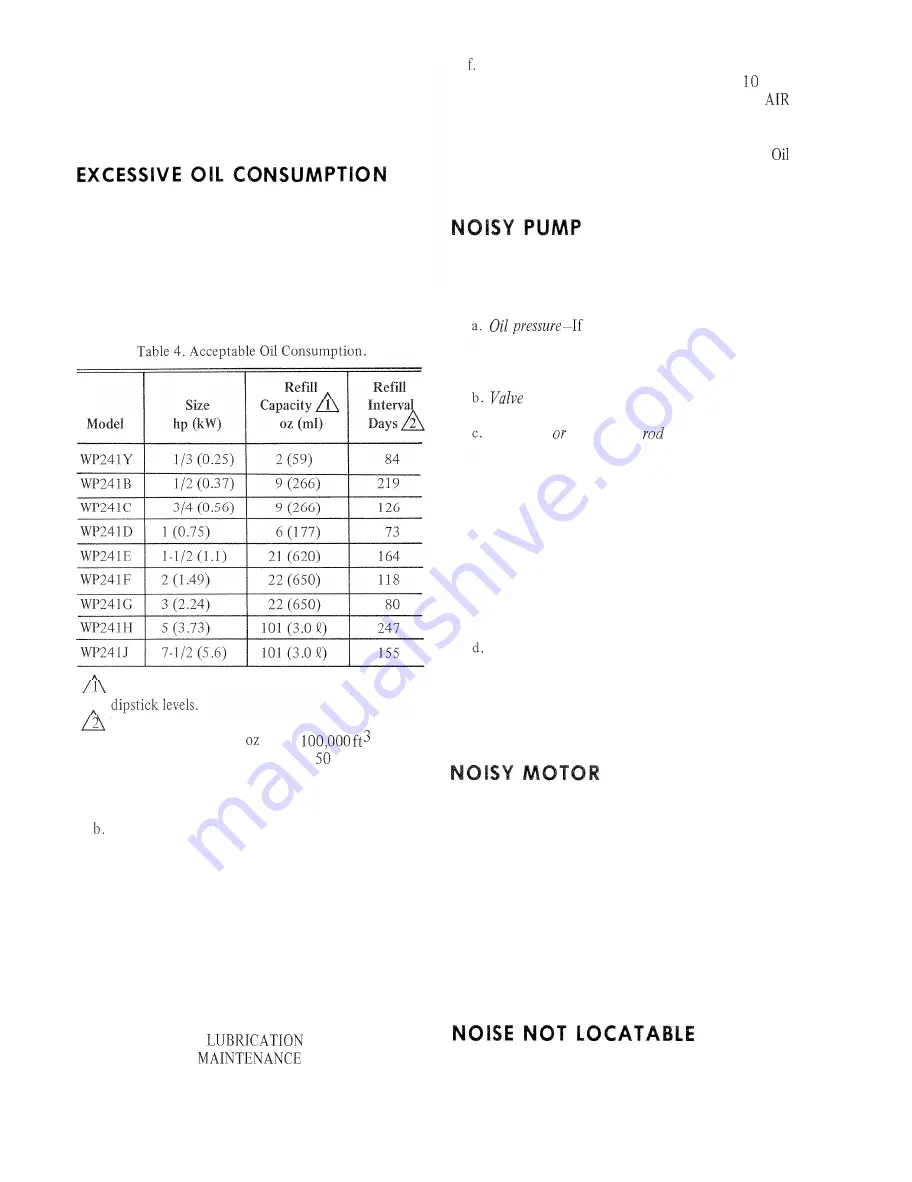
Excessive oil on the after cooler pipe or compressor
head usually indicates air leakage. Locate air leaks with
soap solution while the compressor is operating.
While
the compressor is in the off cycle, check the unloaders
under pressure.
Excessive oil consumption is a difficult problem.
Before repair, take the following steps:
a.
Confirm the
Complaint-Oil at the tank drain does
not necessarily indicate
high oil
consumption.
Table 4 shows acceptable oil consumption in terms
of fill amount and time between refills.
Oil capacity in crankcase between high and low
Days running time between high and low dipstick
levels, based on three oil per
air used
(31
ml
oil per Ml air used) and
percent maxi-
mum duty cycle. Does not allow for spillage or
leakage.
Make certain proper grade of nondetergent oil is
being used (see Table 2) and compressors are not
being overfilled. Overfilling always causes high oil
consumption. Oil level should never be above the
high mark on the dipstick.
c. Check for leaks.
d. Check intake filter/piping and crankcase breather
valve(s) for cleanliness and obstruction.
e. Check for excessive oil pressure or high percent
operation (see
and PRESSURE
paragraphs in
section). If, after
performing the above, a unit is still considered an
oil consumer with no apparent external cause, then:
Check pump-up and cycle pressures against the
values in Table 3. Differences greater than
per-
cent indicate worn parts (see WON’T PUMP
paragraph).
g. Remove valves and examine piston top for oil.
wetting is acceptable, but an accumulation of oil
indicates a defective pump.
The
most common reason for a noisy pump is a loose
flywheel or motor pulley. Check for these first, then
check:
low,
check pump as described in
WRONG
OIL
PRESSURE paragraph.
Lack
of oil
pressure may have caused bearing damage.
assemblies
-Make certain they are tight.
Wrist pin connecting
bearings-Stop
pump
and remove belts. Using the flywheel, rotate pump
back and forth about two inches (5 1 mm). If knock
is heard, a bad wrist pin or connecting rod bushing
probably exists. Inspect the rod bushings by
removing side plate and rod caps or
remove
head
and observe piston while rocking flywheel. Piston
should follow movement without play (except at
top and bottom dead center where piston appears
to hesitate). Inspect cylinder and head for carbon
build-up.
Bad main
bearings-Check for end play by attempt-
ing to move flywheel in different directions. Listen
and feel for any play. End play on the crankshaft
is usually eliminated by removing one of the
shims
beneath the bearing housing adjustment plate. A
slight drag, when turned by hand, is proper,
Check for a loose
motor
pulley. A low-pitch growl is
an indication
of low voltage.
If noise is slight, lubricate motor in accordance with
instructions on nameplate. Noise should disappear so
motor runs properly. Watch for dry bearings, as
these
shorten motor life. To check bearings, stop motor,
remove belt and check for side play in motor shaft. Turn
motor by hand. Any side play or noise is an indication
of bad bearings. If bearings are bad, replace motor. End
play (movement or motor shaft in and out) is common
in this type of motor and is not an indication of wear.
Use a large screwdriver or similar implement. Place
the point end against suspected areas and the other against
the ear. Listen for abnormalities.
75-7268
8