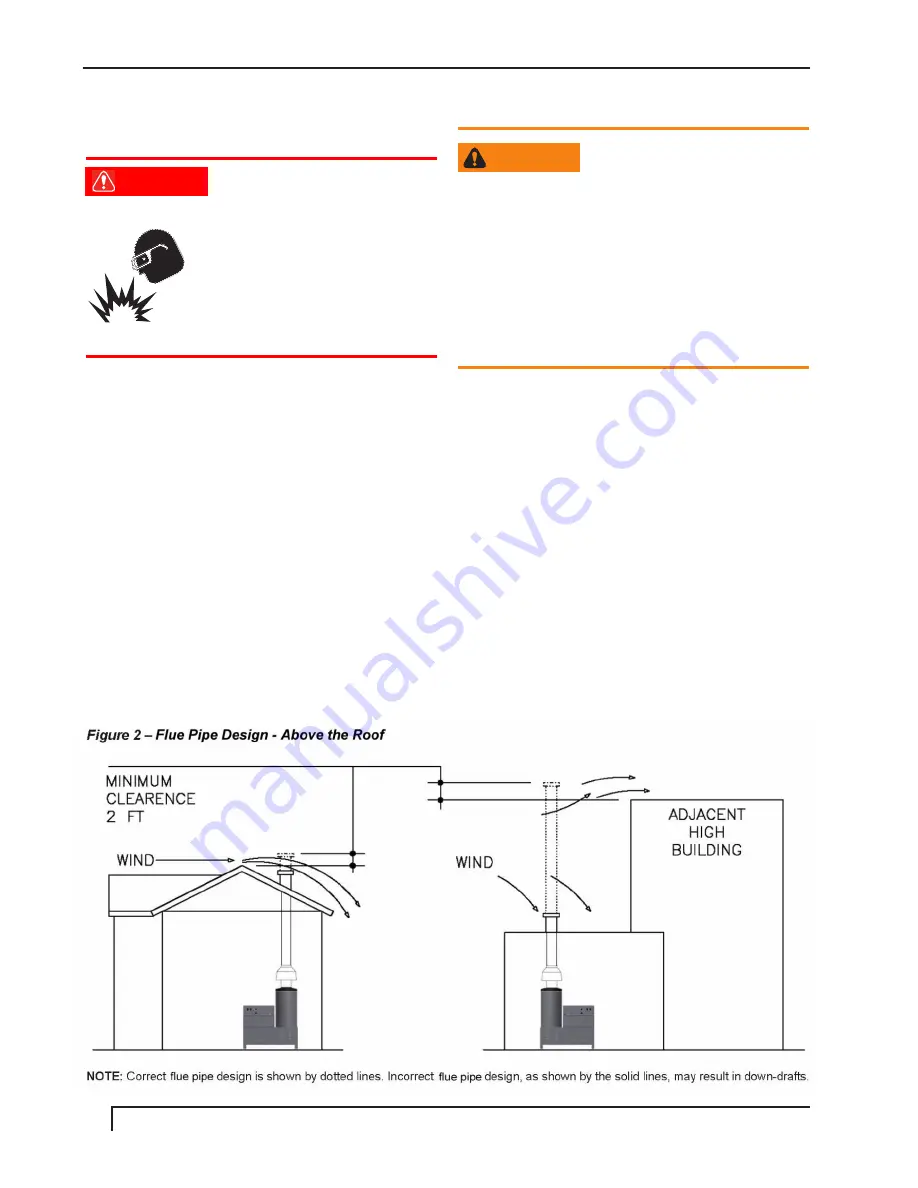
6
KNA Burner Manual 9.801-300.0 rev. 8/13
Inspect/Prepare
Equipment Site Location
DANGER
Professional Service
Required
Incorrect installation, adjust-
ment and use of this burner
could result in severe personal
injury, death or substantial
property damage from fire,
carbon monoxide poisoning,
soot or explosion.
Please read and understand the manual supplied with
this equipment. This equipment must be installed,
adjusted and put into operation only by a qualified
individual or service agency that is:
•
Licensed or certified to install and provide techni-
cal service to oil heating equipment.
•
Experienced with all applicable codes, standards
and ordinances.
•
Responsible for the correct installation and com-
mission of this equipment.
•
Skilled in the adjustment of oil burners using
combustion test instruments.
Section: Inspect/Prepare Installation Site
Inspect Flue Pipe
WARNING
Fire, Smoke &
Asphyxiation Hazard
•
Carefully inspect the exhaust vent system
•
Make sure it is properly sized and in good working
condition
•
Follow the instructions supplied by the equipment
manufacturer.
•
Regulation by these authorities take precedence
over the general instructions provided in this instal-
lation manual.
Starting with minimum gph firing rate, the minimum
size recommended is 8" flue pipe with 8" x 8" inside
chimney, unless specified otherwise by the equipment
manufacturer.
1. A flue pipe shall extend at least 3 feet above the
highest point at which the flue pipe comes in con-
tact with the roof and not less than 2 feet above
the highest roof surface or structure within 10 feet
horizontally of the flue pipe. Refer to Figure 2.
2. Any accumulation of soot or debris in the flue piping
offsets should be removed.
3. Any obstruction, such as a protruding joint in the
flue pipe, should be removed.