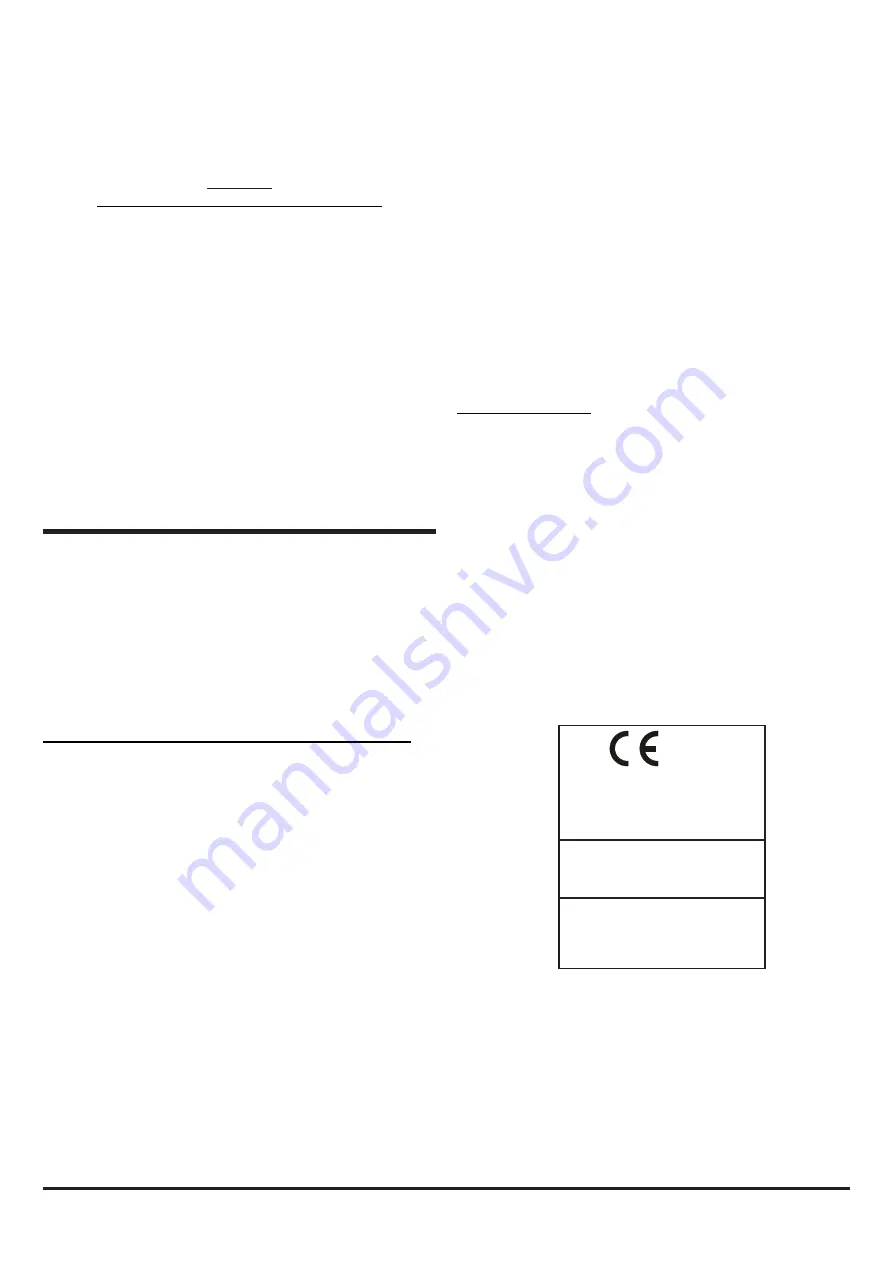
M200-102-01
9
I56-6576-001
Turn the sensor head anti-clockwise to remove from base (and
clockwise to relocate). Do
NOT
interchange the devices and do
NOT
alter the rotary address switch settings on the sensors. If replacing a
sensor, ensure that the address set on the new sensor is the same as
on the sensor being replaced. Use
ONLY
model number
F-SEN-MI
as
a replacement sensor.
WARNING
Using compressed air to clean the pipe system
High pressure air flushed through the system could damage the
fan, ensure that the FAAST LT-200 unit is sealed or detached from
the system before commencing this procedure.
USB Connection
PC connectivity is provided by an on board USB
B
port located centrally
between the filter and the sensor cover (see Figure 9 displayed
earlier in the guide). The USB interface allows access to the PipeIQ
application software running on a PC.
Note: The USB connecting cable should be removed during
normal operation
.
Changing Default Settings / Verifying a Pipe Layout Design
To change any of the default options, or to use the pipe layout design
function, it will be necessary to connect the detector to a PC/laptop
with the PipeIQ software installed (version 2.9.1 or higher). For more
complex designs using increased functionality (experienced users
only) see the
FAAST LT-200 Advanced Setup and Control Guide
for
further information.
P
ipe
IQ
™
SOFTWARE
The PipeIQ software is supplied on a USB pen stick with the device,
or can be downloaded from www.faast-detection.com.
For the FAAST
LT-200, it is necessary to use PipeIQ version 2.9.1 or higher.
Note 1:
It is strongly recommended that some form of training is
taken before using any version of PipeIQ (contact your distributor
for information on this)
. The information provided here is only a brief
introduction.
Note 2:
To connect a FAAST LT-200 to a PC using the USB port, the
PipeIQ software must be running on the PC and the device must be in
Maintenance
mode (See
Password Sequence to Enter Maintenance
Mode
section previously).
Connecting a PC to a FAAST LT-200 Device for the First Time
Minimum System Requirements
Microsoft Windows Vista, 7, 8 or 10, XP - SP3 (not recommended).
1 GB of RAM.
Graphics hardware with 128 MB of memory and support for OpenGL
2.0 or later.
5 GB of free hard disc space
When the PipeIQ installation is complete:
1) With PipeIQ open on the PC and the device in
Maintenance
mode,
open the device front door by releasing the two Phillips screws.
2) Connect a USB cable from the internal port in the centre of the
device to a spare USB port on the PC (make sure that the USB
connector is pushed fully into the FAAST LT-200 port until it clicks).
The device will now be in
Remote Maintenance
mode.
The USB connection must be made within 5 minutes of entering
the
Maintenance
mode password.
The first time a PC running PipeIQ is connected to a FAAST LT-200
device, the USB port drivers will be installed.
3) In PipeIQ, open the project file (.mdf file) that is associated with
the FAAST LT-200 device being used. If no project file has been
created yet, click on
New
and create a new project. Accept the
PipeIQ disclaimer, select the measurement units, device type and
number of channels.
Make sure that the device type selected
matches the type of FAAST LT-200 device being used
. The
project will assume the factory default configuration for a device.
4) In the Left Hand pane of PipeIQ, left click on the FAAST LT-200
device in the system tree to highlight it. Right click on the FAAST
LT-200 icon in the left hand pane to reveal the menu. Click on
Connect Device
.
Note that to use the full range of connection options, a user must
be connected to the FAAST LT-200 device as an
Administrator
.
Tick the
Admin
box and enter the
Administrator
password to
access these extra commands. The
Administrator
password is the
same as the
Remote Maintenance
password (the default is 3111).
5) Click on
Connect
.
The detector is connected when a small green
tick is indicated on the device icon.
FAAST LT-200 Connected
is
shown at the bottom left corner of the screen.
6) Depending on what operations are required, select the
Configuration
,
Design
or
Monitoring
tab at the bottom of the screen
as necessary.
For greater detail on using PipeIQ with the FAAST LT-200 see the
FAAST LT-200 Setup and Troubleshooting Guide
. For information on
using the
Configuration
,
Design
and
Monitoring
tabs in PipeIQ, see the
FAAST LT-200 Advanced Setup and Control Guide.
Setting the Fan Speed
A default air velocity reference value is set into each FAAST LT-200
unit before leaving the factory. This equates to an optimum air flow of
approximately 45 l/min. Default high/low flow limit thresholds are set to
guarantee a flow fault when the air flow is ±20% of the reference flow.
The FAAST LT-200 fan speed in each channel can be set to
Auto
or
Manual
control. Use Auto mode in normal operation.
EN54-20 : 2006
Class A B & C
Aspirating Smoke Detectors
0832 18
MI-FL2011EI-HS: DOP-ASP031
MI-FL2012EI-HS: DOP-ASP032
MI-FL2022EI-HS: DOP-ASP033
Honeywell Morley-IAS
140 Waterside Road
Hamilton Industrial Estate
Leicester, LE5 1TN, UK
DoP Ref:
Honeywell Morley-IAS
140 Waterside Road
Hamilton Industrial Estate
Leicester.
LE5 1TN
UK