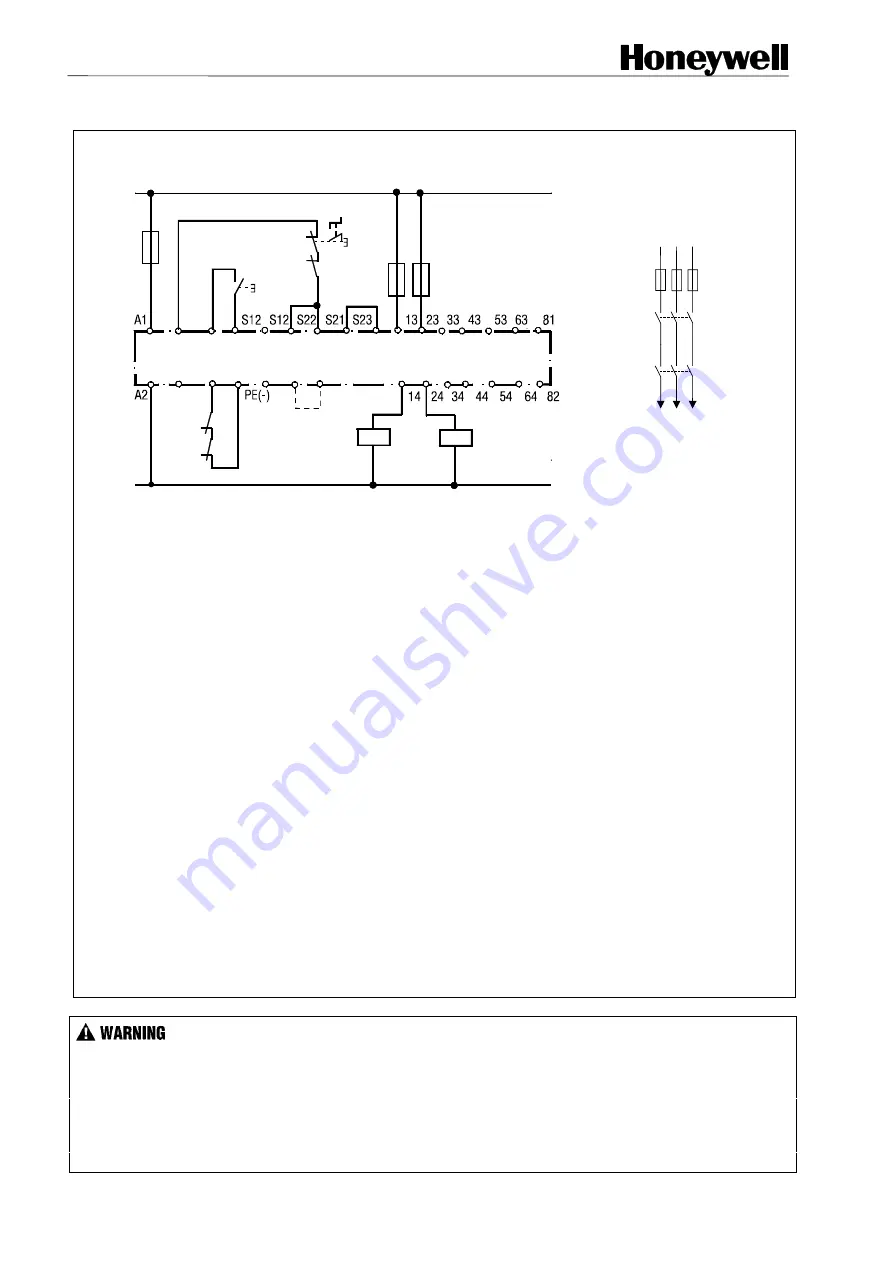
8
107018-04 EN FR26 GLO 1198 Printed in Germany
APPLICATION EXAMPLES (continued)
FIG 11. SINGLE CHANNEL EMERGENCY STOP CIRCUITRY (WITH EXTERNAL CONTACTORS)
K4
K5
Start
L1
Honeywell
FF-SRS 5988
Emer-
gency
stop
(A)
N
Y1 Y2
X1 X2
S33
S11
A3
(+)
S34
(B)
K4
K5
Machine Control
K4
K5
Fuses
L2 L3
L1
A4
(-)
(C)
Fuse
Fuses
This circuit has no redundancy in the emergency-stop control circuit and therefore offers a minor
safety level only.
CONTACT REINFORCEMENT VIA EXTERNAL CONTACTORS:
With switching current >10 A, the output contacts should be reinforced by external contactors (K4 and K5)
with positive-guided contacts. (see
note (B)
)
1. After activation of the E-stop push button, the two K2 and K3 LED’s will turn OFF, indicating that the two
internal safety relays K2 and K3 are de-energized. The normally open safety outputs 13/14..63/64 will
open and de-energize the external contactors K4 and K5. The normally closed monitoring output will
also close.
2. After removing the stop condition, press and release the START push button to restart the safety control
module. If the two contactors K4 and K5 are working properly, the K2 and K3 LED’s will turn ON
indicating that the safety relays K2 and K3 are energized. The six normally open safety contacts will
close and the normally closed monitoring contacts will open allowing the machine to operate.
APPLICATION NOTES:
Note (A):
SINGLE CHANNEL SAFETY DEVICES:
This may be a single output safety device such as a safety limit or interlock switch (for example: CLS, GK
and GSS).
Note (B):
EXTERNAL CONTACTORS:
If contact reinforcement via external safety relays is necessary, the output contacts should be reinforced by
external safety relays. The proper operation of the external contactors must be monitored by looping the
NC contacts into the Final Switching Device (FSD) monitoring loop between terminals Y1/Y2.
Note (C):
START MODE:
Manual start mode: Insert start push-button between S33/S34; no jumper must be set between X1/X2
Automatic start mode: Insert jumper between X1/X2
CONTACT MULTIPLICATION VIA EXTERNAL RELAYS
•
If contact multiplication via external safety relays (or the FF-SRE3081 Extension module) is necessary,
connect one normally closed contact of each relay (or 81/82) in series into the Final Switching Device
monitoring loop (terminals Y1/Y2).
•
Use two independent stop circuit safety relays with mechanically linked contacts to reliably detect a welded
contact.
Failure to comply with these instructions could result in death or serious injury.