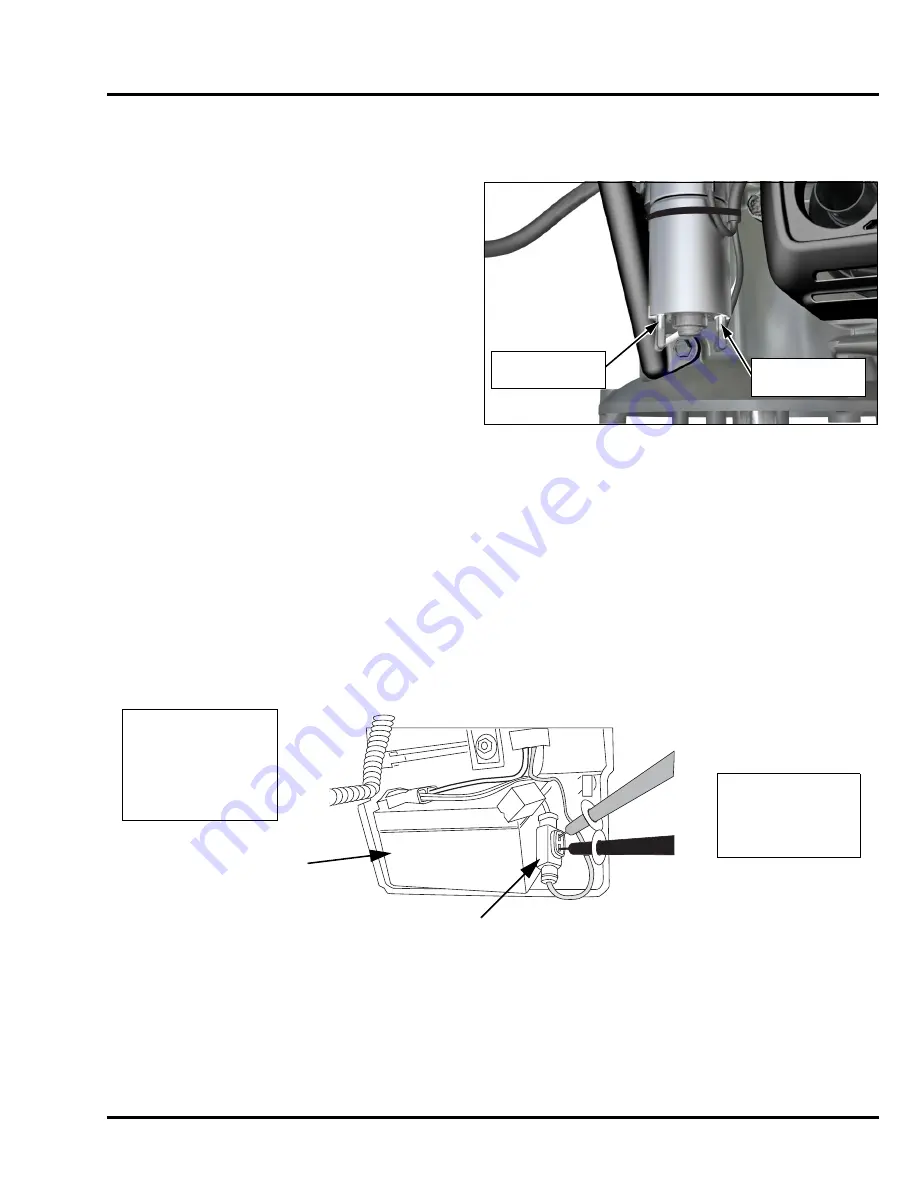
9-11
HRX217HYA • HRX217HZA
FLYWHEEL/IGNITION COIL
4. ELECTRIC STARTER (HZA ONLY)
STARTER MOTOR VOLTAGE INSPECTION
1. Turn the fuel valve OFF and disconnect the spark
plug cap.
2. Slide the covers down from the starter motor
connectors.
3. Set the voltmeter to measure 5 ~ 20 VDC and
carefully connect the alligator clips to the
connectors at the starter motor.
4. Connect the positive alligator clip to the terminal
with the white wire closest to the oil filler, taking
care not to ground (short) the lead. Connect the
negative alligator clip to the black negative lead.
5. Check the cranking voltage at the starter by
turning the key to the start position for 4 seconds
and then releasing for 10 seconds.
Perform this test 1 time and verify that the cranking voltage does not drop below 9.0 VDC.
6. If the cranking voltage drops below 9.0 VDC, charge the battery for 24 hours.
7. After charging the battery, check the cranking voltage again. If the proper cranking voltage still cannot be
obtained, replace the battery.
CHARGE COIL OUTPUT CHECK
The battery must be partially discharged prior to performing this test. If the battery voltage is 12.7 V, disconnect the
spark plug and crank the electric starter several times until the battery voltage has slightly reduced.
Adjust the engine speed to 2,950 ~ 3,100 rpm prior to performing this test. If the charge coil output is below
specifications, check the coil air gap. Fully recharge the battery using an external charger when complete.
Attach positive
lead to white wire.
Attach negative
lead to black wire.
Remove the 3 Amp fuse.
Start the engine and
check DC current across
terminals shown.
Coil Output: > 0.23 A
(–)
(+)
BATTERY
3 AMP FUSE HOLDER
MULTIMETER PROBES
Make sure the probes
are connected correctly
to the multimeter and
that it is set to the
correct range.
Содержание HRX217K6HYA
Страница 3: ...ii NOTES ...
Страница 4: ...1 1 1 SPECIFICATIONS 1 SPECIFICATIONS 1 2 3 WIRING DIAGRAM HZA TYPE 1 4 2 DIMENSIONAL DRAWINGS 1 3 ...
Страница 35: ...2 28 SERVICE INFORMATION HRX217HYA HRX217HZA NOTES ...
Страница 53: ...3 18 MAINTENANCE HRX217HYA HRX217HZA NOTES ...
Страница 54: ...4 1 4 ROTO STOP DRIVE BELT 1 ROTO STOP 4 2 2 DRIVE BELT 4 10 ...
Страница 66: ...6 1 6 MUFFLER 1 REMOVAL INSTALLATION 6 2 6 ...
Страница 75: ...7 8 RECOIL STARTER HRX217HYA HRX217HZA NOTES ...
Страница 91: ...8 16 FUEL SYSTEM HRX217HYA HRX217HZA NOTES ...
Страница 131: ...10 26 CAM PULLEY CRANKSHAFT PISTON CYLINDER HRX217HYA HRX217HZA NOTES ...
Страница 149: ...12 10 VARIABLE MOWING SYSTEM MOWER DECK WHEELS HRX217HYA HRX217HZA NOTES ...
Страница 150: ...13 1 13 TRANSMISSION 1 REMOVAL 13 2 2 INSTALLATION 13 4 ...
Страница 167: ...14 12 OPERATION HRX217HYA HRX217HZA NOTES ...
Страница 169: ...HRX217HYA HRX217HZA V Valve Clearance Adjustment 3 12 Valve Clearance Check Adjustment 3 12 Versamow System 14 1 ...