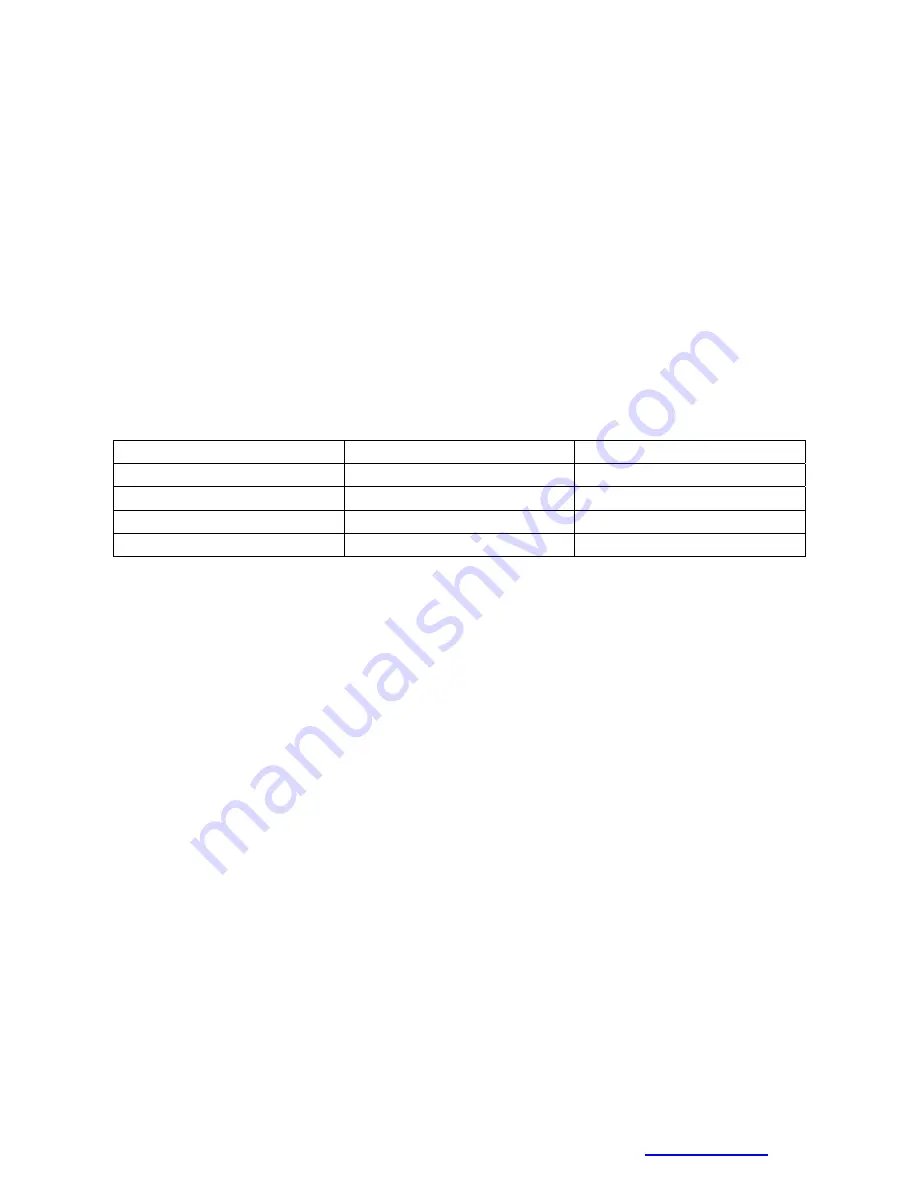
page 13 of 16
ALFA IN a.s. ©
www.alfain.eu
4. Press the torch trigger
5. Adjust the amount of gas on the reduction gas valve (it is not a part of the
welding machine) by the
F7
adjusting screw
6. Release the torch trigger
8. WELDING
8.1 SETTING WELDING CURRENT AND VOLTAGE
When the wire had been installed and gas had been set it is possible to start
welding.
1. The appliance must be plugged into the mains, the ON/OFF switch
4
on
"I".
2. To select the voltage use step switch
2
and
3.
3. To select the current (that is linked to the wire speed) use the
potentiometer
1.
Positions of the switch
Duty cycle
Welding current
MAX-2 10%
120
A
MAX-1
95
A
MIN-2 60%
51
A
MIN-1
35
A
Duty cycle mean percentage of time cycle of 10 minutes , after which the
machine can withstand weld at a given current, without switching off by
means of the thermal protection .
For orientating adjusting of the welding current and voltage you can use
empirical relation U2 = 14+0,05 2. From that you can specify desired voltage.
According to this relation, one can determine the required voltage. When
setting the voltage has to considered the decline in load welding. The voltage
drop is approximately 4.5-5.0 V at 100 A.
Setting the welding current is performed so that the selected welding voltage
settles the desired welding current by increasing or decreasing wire feed
speed until the optimum welding arc is reached .
Please note that the actual settings for optimum arc may vary slightly
depending on the position of the weld material and voltage fluctuations.
To achieve a good quality of the welds and the optimum setting of the
welding current is necessary that the distance of the welding tip from the
material is about 10 times the diameter of the welding wire (Fig. 5)