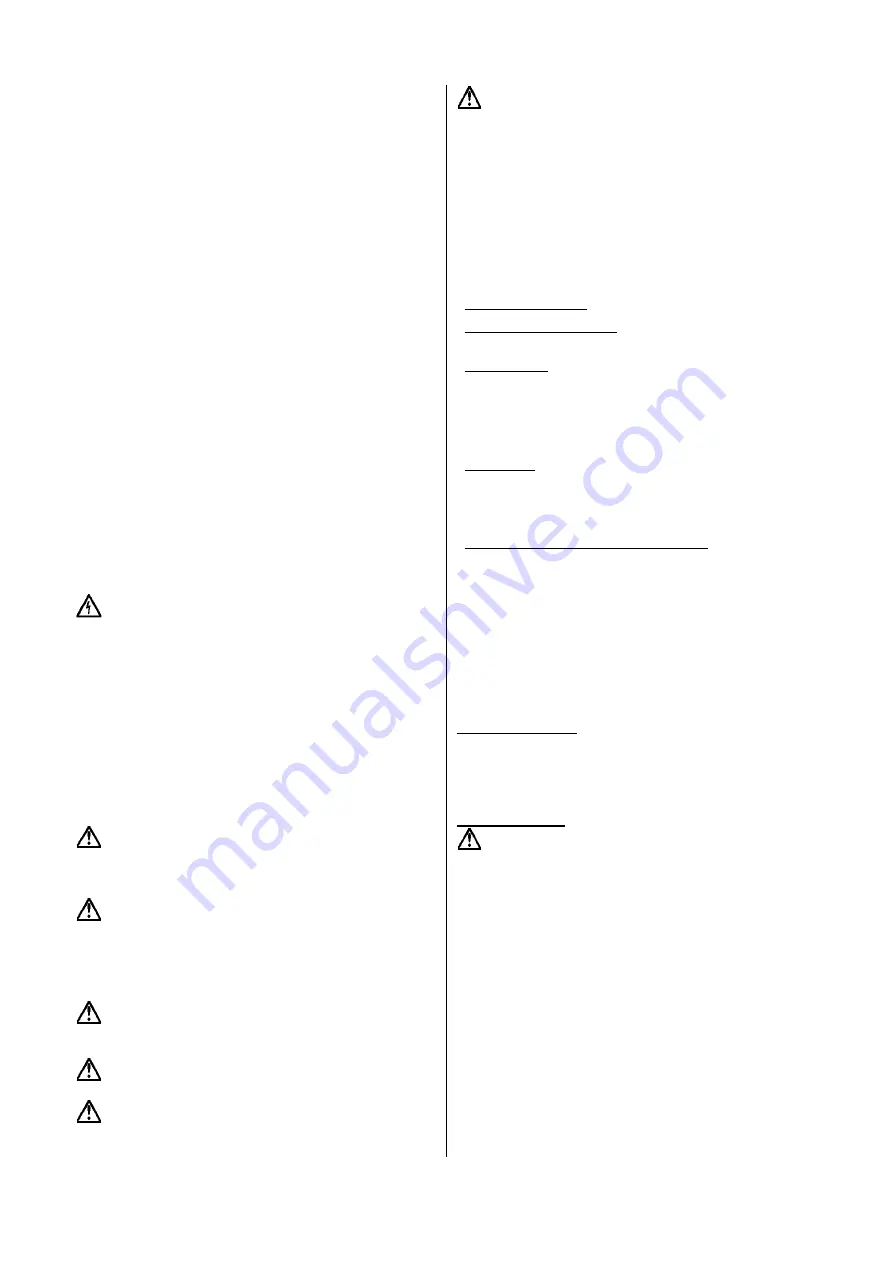
14
•
•
The diameter of the discharge pipe must be DN 80 and
should not installed in close arcs. The discharge pipe
must conduct over the sewer level, that means con-
stantly rising over that niveau and subsequently as a
loop directly to the collecting conduit.
•
To prevent a freezing of the discharge pipe please iso-
late the complete discharge pipe up to the sewer level.
•
Directly above the swing check valve mount a gate
valve into the discharge pipe.
•
For a trouble free operation of the pneumatic level con-
trol it is absolutly necessary that the pressure hose be-
tween tank and control box is installed without loops,
bending and constantly rising.
•
Cut off the blanked off end of the air vent and connect
a DN 70 vent pipe to the tank by means of the flexible
connection supplied. The vent pipe should be led out
into the open air in accordance with local regulations.
•
Mount the supplied pump controller flood protected on
the wall in accordance with local regulations.
•
A manual diaphragm pump is available as an accesso-
ry. The pump is connected to the 1“ tank port.
The manual diaphragm pump is used for draining the
tank in the event of pump failure. Above the diaphragm
pump
must
be fitted with a non-return valve on the
discharge side. To facilitate service of the diaphragm
pump, it is advisable to fit a 1“ isolating valve to the
tank port. The pipe must conduct over the sewer level,
that means constantly rising over that niveau and sub-
sequently as a loop directly to the collecting conduit.
8. Start-Up
Never let the pump run dry for a long time of period, as
it will destroy the pump (danger of overheating).
Before starting the disposal unit make sure that all isolating
valves are open and check that the unit runs satisfactorily.
Make sure that the correct phase sequence was proofed at
the 3-ph models (see 6.3.).
Turn the operation switch into the position "Auto".
In combination with the pneumatic level control the pump
starts and stops according to the liquid level in the tank.
9. Maintenance and Repair
In case of a defect of the pump, a repair shall be car-
ried out only by the manufacturer or through an authorized
workshop. Modifications of the pump must be confirmed by
the manufacturer. Only HOMA spare parts shall be used.
In accordance with the product liability law we point out
that we shall not be liable for damages caused by our
product due to unauthorized repair by persons other than
the manufacturer or an authorized workshop or due to the
use of spare parts other than original HOMA parts. The
same product liability limitations are valid for accessories.
Before maintenance or repair disconnect the pump
from the power supply to avoid accidental starting of the
pump!
Before maintenance or repair make sure that all rotat-
ing parts stand still!
Before carrying out maintenance and service, the pump
must be thoroughly flushed with clean water. Rinse the
pump parts in clean water after dismanteling.
At pump types with oil chamber an overpressure can
escape with loosening of the oil chamber control screw.
Screw only when pressure balance took place.
Pumps running under normal operation conditions should
be inspected at least once a year. If the pumped liquid is
very muddy or sandy or if the pump is operating continu-
ously, the pump should be inspected every 1.000 operating
hours.
For long and trouble-free operation of the pump, following
points should be checked regularly:
- Nominal current (A): Check with amp-meter.
- Pump parts and impeller: Check for possible wear.
Replace defective parts.
- Ball bearings: Check the shaft for noisy or heavy opera-
tion (turn the shaft by hand). Replace defective ball bear-
ings. A general overhaul of the pump is usally required in
case of defective ball bearings or poor motor function. This
work must be carried out by an authorized
service workshop.
- Cable entry: Make sure that the cable entry is watertight
and that the cables are not bent sharply and/or pinched.
Additionally at pump types with oil chamber:
- Oil level and oil condition in oil chamber:
Put the pump in horizontal position, so that the screw of the
oil chamber is above (at larger pumps: one of both screws).
Remove the screw and infer a small quantity of oil. The oil
becomes greyish white like milk if it contains water. This
may be the result of defective shaft seal.
In this case leave the condition of the shaft seals by a
HOMA Service to examine.
The oil should be replaced after 3000 operating hours.
Oil type: degradable HOMA-Atox (available on request).
Used oil is to be disposed accordingly.
Servicing Contract
For a regular expert execution of all necessary mainte-
nance and inspection we recommend the conclusion of a
servicing contract by our HOMA Service. Please contact
our HOMA customer service.
Return of pumps
If a pump has been used for a liquid which is injurious
to health or toxic, the pump will be classified as contami-
nated.
If HOMA is requested to service the pump, HOMA must be
contacted with details about the pumped liquid, etc. before
the pump is returned for service. Otherwise HOMA can re-
fuse to accept the pump for service (see attachment).
Possible costs of returning the pump are paid by the cus-
tomer. However, any application for service (no matter to
whom it may be made) must include details about the
pumped liquid if the pump has been used for liquids which
are injurious to health or toxic.
Содержание Sanistar C Series
Страница 19: ...19 14 2 Ersatzteilzeichnung Spare part drawing...
Страница 23: ...21...
Страница 24: ...22...