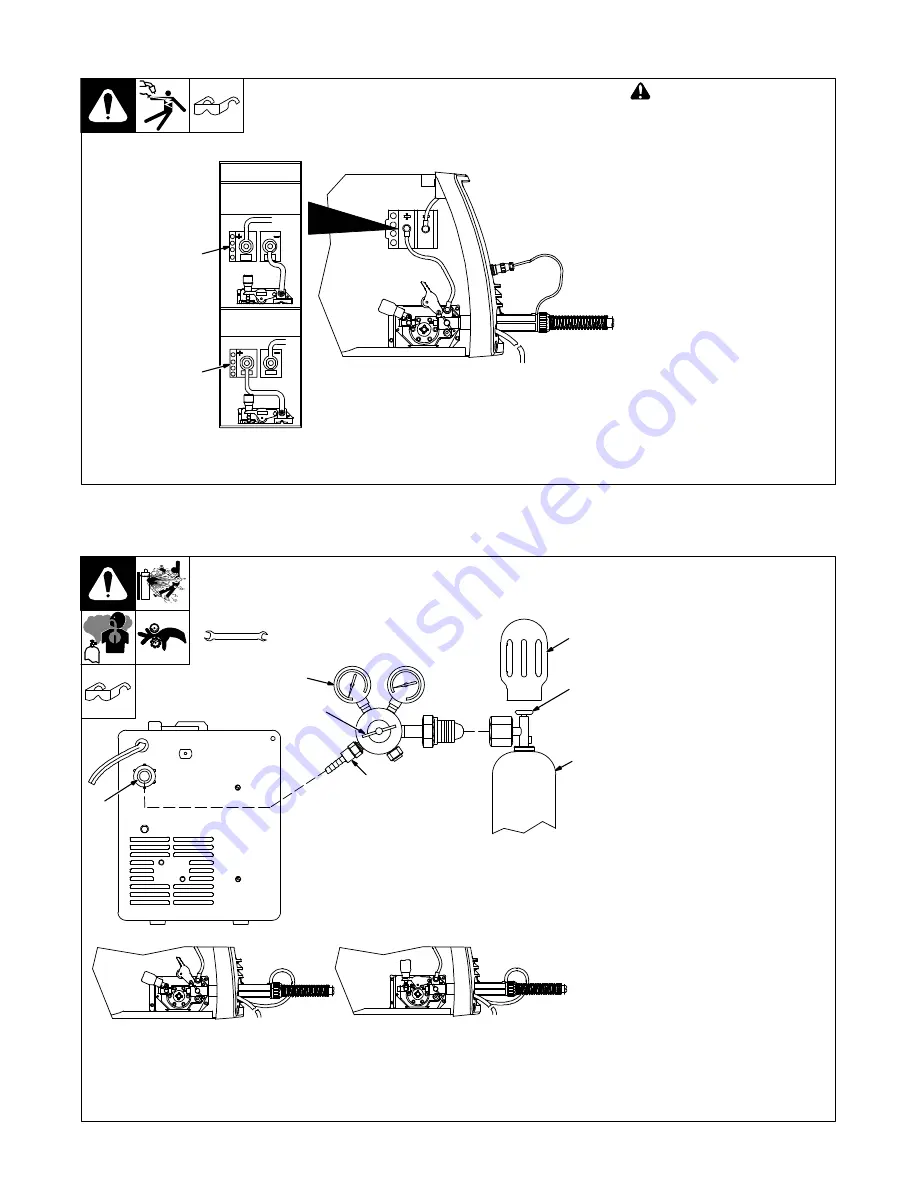
.
A complete Parts List is available at www.HobartWelders.com
OM-260273 Page 13
5-6. Changing Polarity
!
Turn off welding power
source.
1
Lead Connections For Direct
Current Electrode Negative
(DCEN)
2
Lead Connections For Direct
Current Electrode Positive
(DCEP)
Always read and follow wire
manufacturer’s recommended
polarity, and see Section 5-5.
Close door.
260 459-A
1
CHANGING
POLARITY
DCEN
Electrode negative
for flux cored wire
DCEP
Electrode positive
for solid wire
2
5-7. Installing Gas Supply
Obtain gas cylinder and chain to
running gear, wall, or other
stationary support so cylinder
cannot fall and break off valve.
1
Cap
2
Cylinder Valve
Remove cap, stand to side of valve,
and open valve slightly. Gas flow
blows dust and dirt from valve.
Close valve.
3
Cylinder
4
Regulator/Flowmeter
Install so face is vertical.
5
Regulator/Flowmeter Gas
Hose Connection
6
Welding Power Source Gas
Hose Connection
Connect supplied gas hose
between regulator/flowmeter gas
hose connection, and fitting on rear
of welding power source.
7
Flow Adjust
Flow rate should be set when gas is
flowing through welding power
source and welding gun. Open
pressure assembly so that wire will
not feed. Press gun trigger to start
gas flow.
Typical flow rate is 20 cfh (cubic
feet per hour). Check wire
manufacturer’s recommended
flow rate.
After flow is set, close pressure
assembly.
260 460-B
.
DO NOT use Argon/Mixed gas regulator/flowmeter with CO
2
shielding gas.
See Accessories/Consumables for optional CO
2
gas regulator/flowmeter.
Pressure
Assembly Open
Pressure
Assembly Closed
Argon Gas Or
Mixed Gas
1
2
3
4
5
7
6
Tools Needed:
5/8 or 11/16, 1-1/8 in.
Содержание Handler 190
Страница 26: ...OM 260273 Page 24 SECTION 8 ELECTRICAL DIAGRAMS 248830 B Figure 8 1 Circuit Diagram ...
Страница 36: ...OM 260273 Page 34 Notes ...
Страница 37: ...OM 260273 Page 35 Notes ...
Страница 38: ...Notes ...