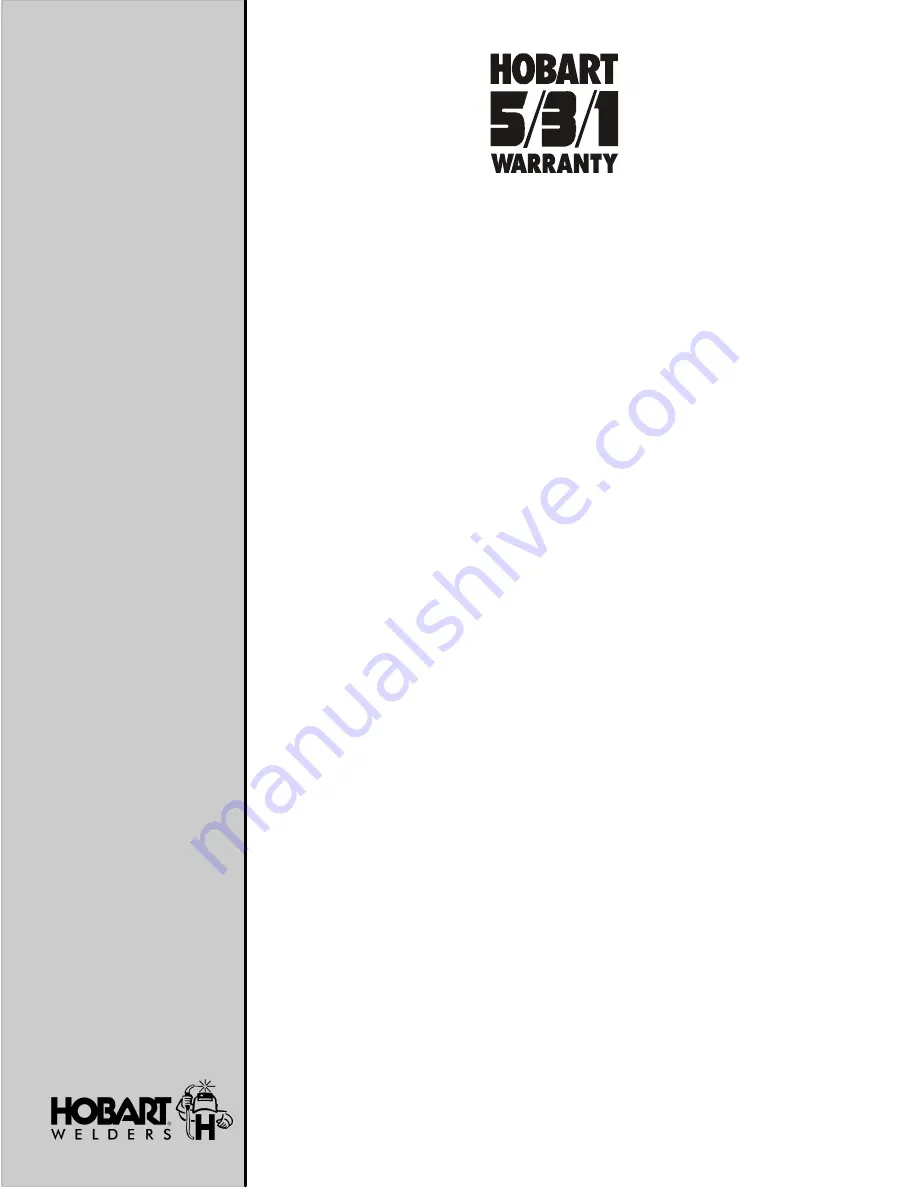
Warranty Questions?
Call
1-877-HOBART1
for your local
Hobart distributor.
hobart retail 8/03
Service
You always get the fast,
reliable response you
need. Most replacement
parts can be in your
hands in 24 hours.
Support
Need fast answers to the
tough welding questions?
Contact your distributor or
call 1-800-332-3281. The
expertise of the distributor
and Hobart is there to
help you, every step of
the way.
Effective January 1, 2003
5/3/1 WARRANTY applies to all Handler 125, 135 and 175 models, Airforce 250, 250A, 375, 400
and 625 models, and Champion 4500 and 10,000 models, Beta-Mig 1800, Champ 1435, 2060, 8500
models, Ironman 210 and 250 models, Stickmate models, Tigmate models, and HSW-15 and
HSW-25 spot welder models effective with Serial No. KK200262 and newer.
This limited warranty supersedes all previous Hobart warranties and is exclusive with
no other guarantees or warranties expressed or implied.
Hobart products are serviced by Hobart or Miller Authorized Service Agencies.
LIMITED WARRANTY
−
Subject to the terms and conditions
below, Hobart/Miller Electric Mfg. Co., Appleton, Wisconsin,
warrants to its original retail purchaser that new Hobart
equipment sold after the effective date of this limited warranty is
free of defects in material and workmanship at the time it is
shipped by Hobart. THIS WARRANTY IS EXPRESSLY IN LIEU
OF ALL OTHER WARRANTIES, EXPRESS OR IMPLIED,
INCLUDING THE WARRANTIES OF MERCHANTABILITY AND
FITNESS.
Within the warranty periods listed below, Hobart/Miller will repair
or replace any warranted parts or components that fail due to
such defects in material or workmanship. Hobart/Miller must be
notified in writing within thirty (30) days of such defect or failure, at
which time Hobart/Miller will provide instructions on the warranty
claim procedures to be followed.
Hobart/Miller shall honor warranty claims on warranted
equipment listed below in the event of such a failure within the
warranty time periods. All warranty time periods start on the date
that the equipment was delivered to the original retail purchaser,
or one year after the equipment is sent to a North American
distributor or eighteen months after the equipment is sent to an
International distributor.
1.
5 Years — Parts and Labor
* Original Main Power Rectifiers
* Transformers
* Stabilizers
* Reactors
2.
3 Years — Parts and Labor
* Drive Systems
* PC Boards
* Rotors, Stators and Brushes
* Idle Module
* Solenoid Valves
* Switches and Controls
* Spot Welder Transformer
3.
1 Year — Parts and Labor Unless Specified
(90 days for industrial use)
* Motor-Driven Guns
* MIG Guns/TIG Torches
* Relays
* Contactors
* Regulators
* Water Coolant Systems
* Flowgauge and Flowmeter Regulators (No Labor)
* HF Units
* Running Gear/Trailers
* Plasma Cutting Torches
* Remote Controls
* Replacement Parts (No labor)
* Accessories
* Field Options
(NOTE: Field options are covered
for the remaining
warranty period of the product they are installed in, or
for a minimum of one year — whichever is greater.)
4.
Engines, batteries and tires are warranted separately by the
manufacturer.
Hobart’s 5/3/1 Limited Warranty shall not apply to:
1.
Consumable components such as contact tips, cutting
nozzles, slip rings, drive rolls, gas diffusers, plasma
torch tips and electrodes, weld cables, and tongs and
tips, or parts that fail due to normal wear.
(Exception:
brushes, slip rings, and relays are covered on Hobart
Engine-Driven models.)
2.
Items furnished by Hobart/Miller, but manufactured by
others, such as engines or trade accessories. These items
are covered by the manufacturer’s warranty, if any.
3.
Equipment that has been modified by any party other than
Hobart/Miller, or equipment that has been improperly
installed, improperly operated or misused based upon
industry standards, or equipment which has not had
reasonable and necessary maintenance, or equipment
which has been used for operation outside of the
specifications for the equipment.
HOBART PRODUCTS ARE INTENDED FOR PURCHASE AND
USE BY COMMERCIAL/INDUSTRIAL USERS AND PERSONS
TRAINED AND EXPERIENCED IN THE USE AND
MAINTENANCE OF WELDING EQUIPMENT.
In the event of a warranty claim covered by this warranty, the
exclusive remedies shall be, at Hobart’s/Miller’s option: (1) repair;
or (2) replacement; or, where authorized in writing by
Hobart/Miller in appropriate cases, (3) the reasonable cost of
repair or replacement at an authorized Hobart/Miller service
station; or (4) payment of or credit for the purchase price (less
reasonable depreciation based upon actual use) upon return of
the goods at customer’s risk and expense. Hobart’s/Miller’s
option of repair or replacement will be F.O.B., Factory at
Appleton, Wisconsin, or F.O.B. at a Hobart/Miller authorized
service facility as determined by Hobart/Miller. Therefore no
compensation or reimbursement for transportation costs of any
kind will be allowed.
TO THE EXTENT PERMITTED BY LAW, THE REMEDIES
PROVIDED HEREIN ARE THE SOLE AND EXCLUSIVE
REMEDIES. IN NO EVENT SHALL HOBART/MILLER BE
LIABLE FOR DIRECT, INDIRECT, SPECIAL, INCIDENTAL OR
CONSEQUENTIAL DAMAGES (INCLUDING LOSS OF
PROFIT), WHETHER BASED ON CONTRACT, TORT OR ANY
OTHER LEGAL THEORY.
ANY EXPRESS WARRANTY NOT PROVIDED HEREIN AND
ANY IMPLIED WARRANTY, GUARANTY OR
REPRESENTATION AS TO PERFORMANCE, AND ANY
REMEDY FOR BREACH OF CONTRACT TORT OR ANY
OTHER LEGAL THEORY WHICH, BUT FOR THIS PROVISION,
MIGHT ARISE BY IMPLICATION, OPERATION OF LAW,
CUSTOM OF TRADE OR COURSE OF DEALING, INCLUDING
ANY IMPLIED WARRANTY OF MERCHANTABILITY OR
FITNESS FOR PARTICULAR PURPOSE, WITH RESPECT TO
ANY AND ALL EQUIPMENT FURNISHED BY
HOBART/MILLER IS EXCLUDED AND DISCLAIMED BY
Hobart/Miller.
Some states in the U.S.A. do not allow limitations of how long an
implied warranty lasts, or the exclusion of incidental, indirect,
special or consequential damages, so the above limitation or
exclusion may not apply to you. This warranty provides specific
legal rights, and other rights may be available, but may vary from
state to state.
In Canada, legislation in some provinces provides for certain
additional warranties or remedies other than as stated herein,
and to the extent that they may not be waived, the limitations and
exclusions set out above may not apply. This Limited Warranty
provides specific legal rights, and other rights may be available,
but may vary from province to province.
Содержание H-10 Gun
Страница 24: ...OM 925 Page 20 6 2 Weld Parameter Chart For 115 VAC Model ...
Страница 25: ...OM 925 Page 21 217 618 A ...
Страница 26: ...OM 925 Page 22 6 3 Weld Parameter Chart For 230 VAC Model ...
Страница 27: ...OM 925 Page 23 217 754 B ...
Страница 33: ...OM 925 Page 29 SECTION 8 ELECTRICAL DIAGRAM 217 621 A Figure 8 1 Circuit Diagram For 115 VAC Model ...
Страница 34: ...OM 925 Page 30 217 755 A Figure 8 2 Circuit Diagram For 230 VAC Model ...
Страница 45: ...OM 925 Page 41 Notes ...