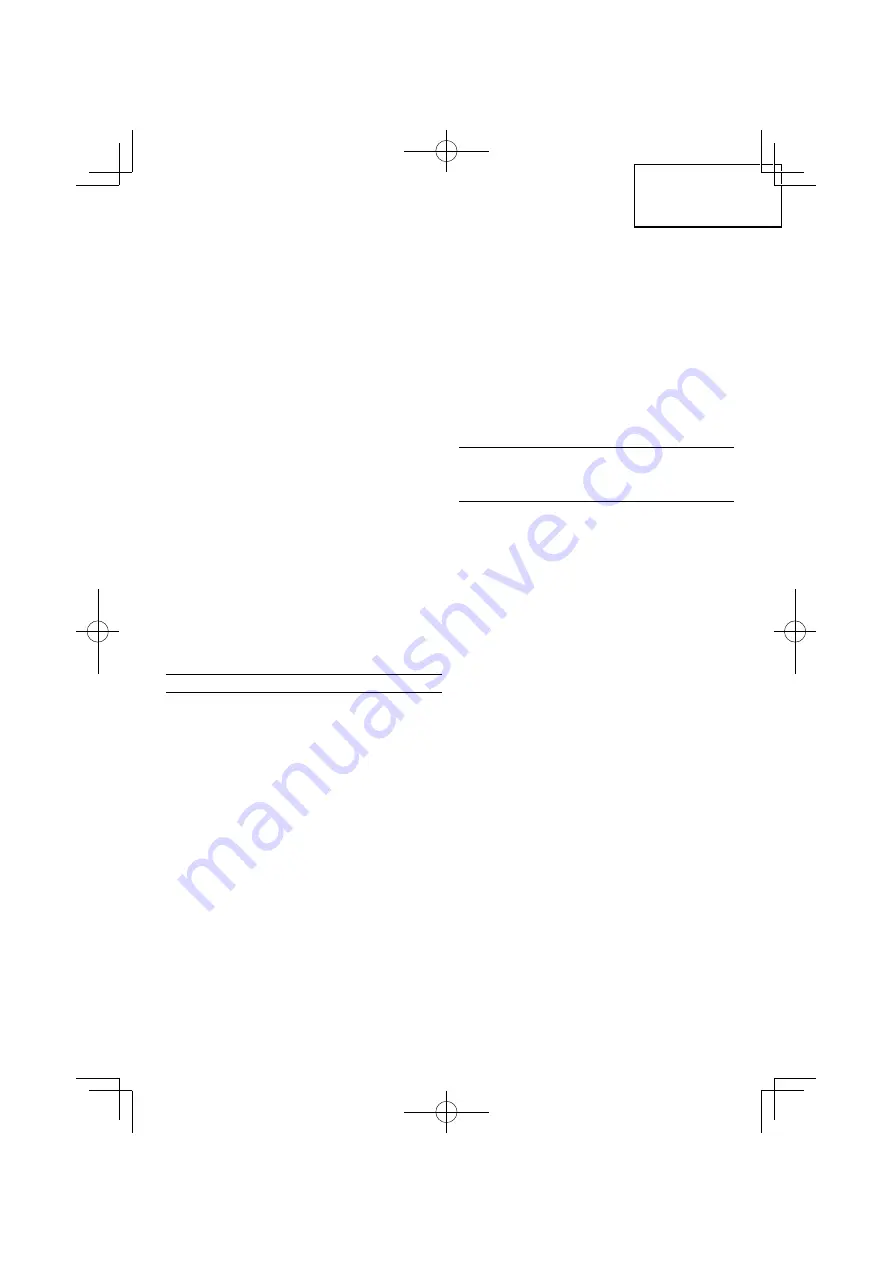
(3)
As
shown
in
Fig.
3
,
push
in
the
lock
pin
to
prevent
rotation
of
the
spindle.
Then,
secure
the
sanding
disc
by
tightening
the
wheel
nut
with
the
wrench.
2.
Mounting
the
Diamond
Wheel
CAUTION
When
utilizing
the
diamond
wheel,
pay
particular
attention
to
the
following
points.
(1)
Utilize
the
correct
size
diamond
wheel.
(external
dia.
105
mm,
internal
dia.
20
mm)
(2)
Do
not
apply
cooling
water
or
grinding
fl
uid
while
utilizing
the
diamond
wheel.
(3)
Hold
the
tool
fi
rmly
to
control
the
tendency
of
the
tool
to
be
repelled
by
the
material
during
cutting
operation.
(4)
Ensure
that
the
cutting
depth
is
kept
within
2–5
mm
to
prevent
over-heating
damage
to
the
motor.
Use
with
moderate
cutting
speed,
and
do
not
apply
excessive
pressure
on
the
workpiece.
○
Mounting
the
Guide
Base
Assembly.
(Fig.
4)
(1)
Loosen
the
two
small
screws
on
the
wheel
guard.
(2)
Insert
the
guide
piece
between
the
wheel
guard
and
set
plate
(A),
and
tighten
one
of
the
small
screws.
Ensure
that
the
guide
will
not
move.
(3)
Set
the
angle
of
the
wheel
guard
to
a
suitable
position
for
operation,
and
securely
tighten
the
remaining
small
screw
to
fi
x
the
wheel
guard
in
position.
○
Mounting
the
Diamond
Wheel.
(Fig.
5)
NOTE
Mounting
of
the
diamond
wheel
on
the
spindle
is
illustrated
in
Fig.
5
.
Note
that
the
wheel
washer
is
reversed
from
ordinary
usage
with
depressed
center
wheel.
(1)
Mount
the
wheel
washer
and
diamond
wheel
onto
the
spindle.
(2)
Mount
the
concave
side
of
the
wheel
nut
onto
the
diamond
wheel,
and
screw
the
wheel
nut
onto
the
spindle.
(3)
As
shown
in
Fig.
5
push
in
the
lock
pin
to
prevent
rotation
of
the
spindle.
Then,
secure
the
diamond
wheel
by
tightening
the
wheel
nut
with
the
wrench.
MAINTENANCE
AND
INSPECTION
1.
Inspecting
the
depressed
center
wheel
Ensure
that
the
depressed
center
wheel
is
free
of
cracks
and
surface
defects.
Replace
the
depressed
center
wheel
when
it
has
been
worn
out
to
about
60
mm
in
external
diameter.
2.
Inspecting
the
mounting
screws
Regularly
inspect
all
mounting
screws
and
ensure
that
they
are
properly
tightened.
Should
any
of
the
screws
be
loose,
retighten
them
immediately.
Failure
to
do
so
could
result
in
serious
hazard.
3.
Maintenance
of
the
motor
The
motor
unit
winding
is
the
very
“heart”
of
the
power
tool.
Exercise
due
care
to
ensure
the
winding
does
not
become
damaged
and/or
wet
with
oil
or
water.
4.
Inspecting
the
carbon
brushes
(Fig.
8)
The
motor
employs
carbon
brushes
that
are
consumable
parts.
Since
an
excessively
worn
carbon
brush
can
result
in
motor
trouble,
replace
the
carbon
brush
with
a
new
one
having
the
same
carbon
brush
No.
shown
in
the
fi
gure
when
it
becomes
worn
to
or
near
the
“wear
limit”.
In
addition,
always
keep
carbon
brushes
clean
and
ensure
that
they
slide
freely
within
the
brush
holders.
5.
Replacing
carbon
brushes
Disassemble
the
brush
caps
with
a
slotted-head
screwdriver.
The
carbon
brushes
can
then
be
easily
removed.
6.
Service
parts
list
CAUTION
Repair,
modi
fi
cation
and
inspection
of
Hitachi
Power
Tools
must
be
carried
out
by
a
Hitachi
Authorized
Service
Center.
This
Parts
List
will
be
helpful
if
presented
with
the
tool
to
the
Hitachi
Authorized
Service
Center
when
requesting
repair
or
other
maintenance.
In
the
operation
and
maintenance
of
power
tools,
the
safety
regulations
and
standards
prescribed
in
each
country
must
be
observed.
MODIFICATION
Hitachi
Power
Tools
are
constantly
being
improved
and
modi
fi
ed
to
incorporate
the
latest
technological
advancements.
Accordingly,
some
parts
may
be
changed
without
prior
notice.
NOTE
Due
to
HITACHI’s
continuing
program
of
research
and
development,
the
speci
fi
cations
herein
are
subject
to
change
without
prior
notice.
English
6
000Book̲PDA-100D̲Tha.indb 6
000Book̲PDA-100D̲Tha.indb 6
2009/04/10 9:23:33
2009/04/10 9:23:33