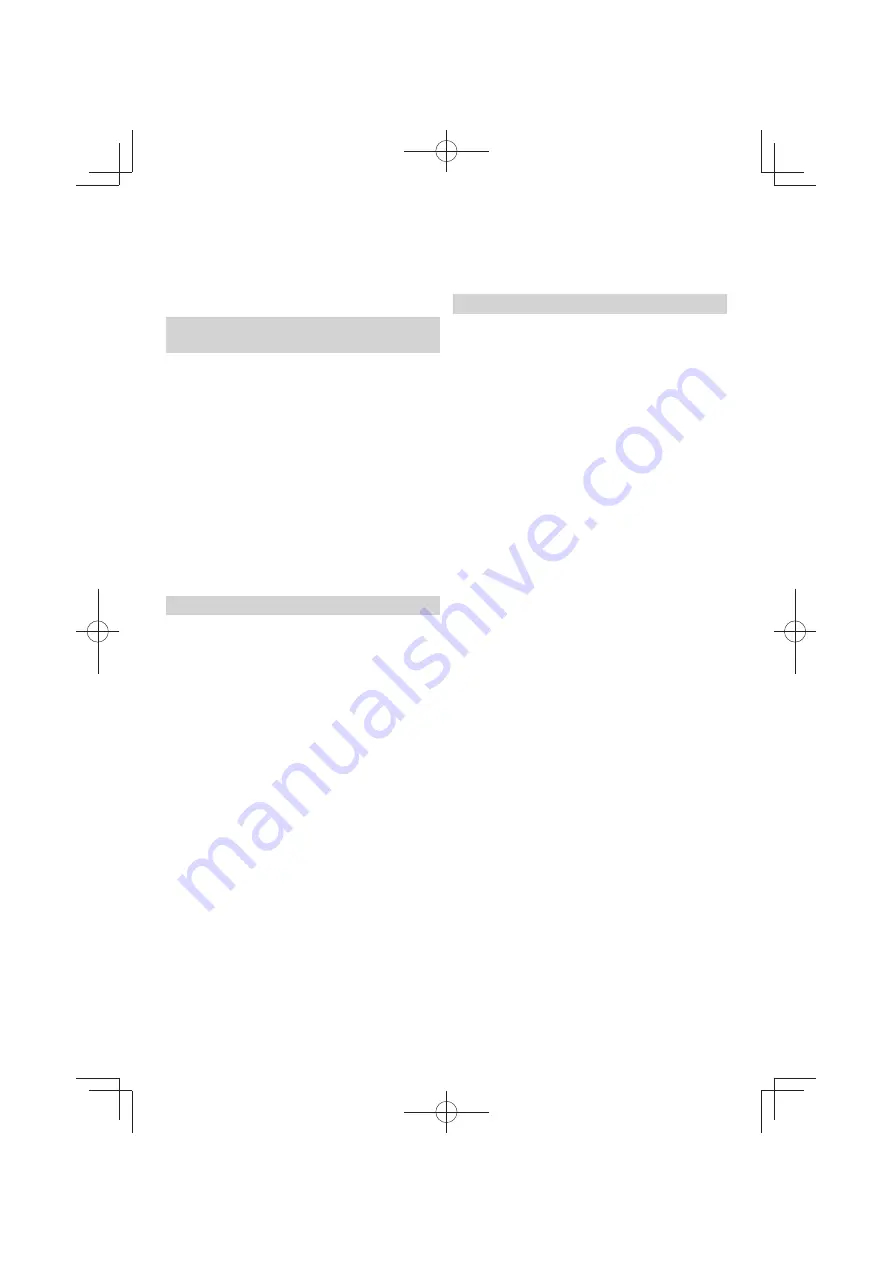
6
English
Do not fail to switch OFF the switch after operation is
completed and pull the plug out.
3. Position of operator
Do not stand in a line with the cutting disc in front of the
machine. Aiways stand aside of the cutting disc.
This measure provides for better protection of your body
against possible splinters in case of cutting disc breakage.
MOUNTING AND DISMOUNTING THE
CUT-OFF WHEEL
1. Dismounting the cut-o
ff
wheel (Fig. 3)
(1) Press the stopper and loosen the bolt with a hex. bar
wrench.
CAUTION
When the mounting shaft for cut-o
ff
wheel cannot be
fi
xed with pressing the stopper, turn the bolt with a hex.
bar wrench while pressing the stopper. The mounting
shaft for cut-o
ff
wheel is
fi
xed when the stopper has been
lowered.
(2) Remove the bolt, washer (A), and the wheel washer and
detach the cut-o
ff
wheel.
2. Mounting the cut-o
ff
wheel
Throughly remove dust from the wheel washers and
bolt then mount the wheel by following the dismounting
procedures in reverse order. Be sure to attach the sub-
cover at the end.
CAUTION
Con
fi
rm that the stopper which was used for installation
and removal of the cut-o
ff
wheel has returned to the
retract position.
HOW TO OPERATE
1. Procedure for
fi
xing the cutting material (Fig. 4 and
5)
Place the workpiece material between vise (A) and vise
(B), raise the clutch and push the screw handle to bring
vise (A) lightly into contact with the workpiece material,
as shown in
Fig. 4
.
Then, turn the clutch down, and securely
fi
x the
workpiece material in position by turning the screw
handle. When the cutting job is completed, turn the
screw handle 2 or 3 times to loosen the vise, and remove
the workpiece material, as shown in
Fig. 5
.
CAUTION
The wheel continues to rotate after the machine is
switched o
ff
.
Never remove or install a workpiece material while the
cut-o
ff
wheel is rotating, to avoid personal injury.
Long workpieces must be supported by blocks
non
fl
ammable material on either side so that it be level
with the base top.
2. Cutting at angles (Fig. 6 and 7)
(1) The machine permits cutting at angles of 45° or 60°.
(2) Loosen the two M10 hexagon socket head bolts on the
vice (B), then set the working surface on the vice-jaw at
any angles of 0°, 30°, or 45° as shown in
Fig. 7
. Upon
completion of setting, securely tighten the two 10 mm
bolts.
(3) When wide material is cut with angle, it will be
fi
rmly
camped by
fi
xing a steel board like
Fig. 8
to the vise (B).
3. Moving the stationary vise-jaw (Fig. 9)
The vise opening is set at the maximum of 170 mm when
shipped from the factory. In case an opening of more
than 170 mm is required, move the vise to the position
shown by the chain line after unscrewing the two bolts.
The maximum opening can be set in two steps 205 mm
and 240 mm. When the cutting material is excessively
wide, the vise can be e
ff
ectively used by repositioning
the stationary side of the vise-jaws.
4. How to use metallic block (Fig. 10)
When the cut-o
ff
wheel has a reduced outer diameter,
insert between the vise (A) and (B) a metallic block
slightly smaller than the dimension of workpiece being
cut to use the cut-o
ff
wheel economically.
MAINTENANCE AND INSPECTION
CAUTION
Before further use of tool, it should be carefully checked
to determine that it will operate properly and perform its
intended function.
Have maintenance and repair work performed only by
quali
fi
ed repair persons.
In this manner, it can be ensured that the safety of the power
tool is maintained.
Be sure to switch o
ff
and pull o
ff
the plug from the power
outlet before inspection and maintenance.
1. A damaged guard or other parts
Damaged parts should be properly repaired or replaced
by a Hitachi Authorized Service Center unless otherwise
indicated in this instruction manual.
2. Defective switches
Have defective switches replaced by a Hitachi
Authorized Service Center.
3. Replacing a cut-o
ff
wheel
When the cut-o
ff
wheel has already become dull while
continually using, the unnecessary load is got from the
motor. Consequently, redress or replace a dull cut-o
ff
wheel to ensure grinding e
ffi
ciency.
4. Inspecting the carbon brushes (Fig. 11)
The Motor employs carbon brushes which are
consumable parts. When they become worn to or near
the “wear limit”, it results in motor trouble.
When an auto-stop carbon brush is equipped, the motor
will stop automatically. At that time, replace both carbon
brushes with new ones which have the same carbon
brush Numbers shown in the
Fig. 11
. In addition, always
keep carbon brushes clean and ensure that they slide
freely within the brush holders.
5. Replacing the carbon brushes
Disassemble the brush caps with a slotted-head
screwdriver. The carbon brushes can then be easily
removed.
6. Check the cable regularly
Have a damaged cable repaired only through a Hitachi
Authorized Service Center.
Replace damaged extension cables. This will ensure
that the safety of the power tool is maintained.
7. Inspecting the mounting screws
Regularly inspect all mounting screws and ensure that
they are properly tightened. Should any of the screws be
loose, retighten them immediately. Failure to do so could
result in serious hazard.
8. Lubrication
Supply oil in the following oil supply points once a month
so as to keep the machine workable for a long time (See
Fig. 1
).
Oil supply points
○
Rotary part of shaft
○
Rotary part of vise
○
Slide way of vise (A)
9. Cleaning
Wipe
o
ff
chip and waste adhered to the machine with a
cloth or the like time to time. Be careful not to make the
motor portion wet with oil or water.
10.
Faults in the machine, including guards or cutter blades,
should be reported as soon as they are discovered.
0000Book̲CC14SF.indb 6
0000Book̲CC14SF.indb 6
2015/01/06 11:10:51
2015/01/06 11:10:51