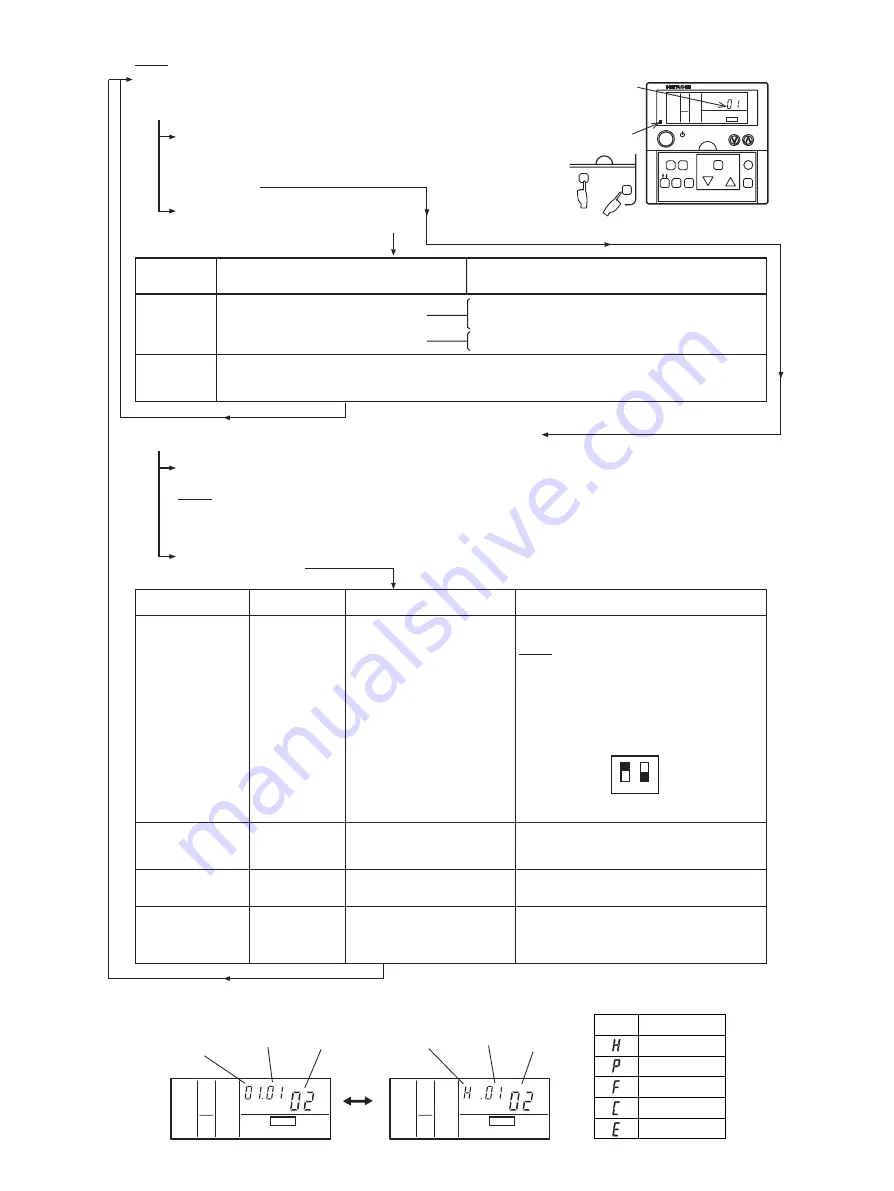
Table 7.2 Checking of Wire Connection by Test Run
COOL
MED
A/C
ADDS. RN
ALARM
COOL
MED
A/C
ADDS. RN
ALARM
Indicated
for a second
alternately
Abnormal Indoor
Unit No.
Abnormal Ref.
Cycle No.
Alarm Code
Alarm Code
Model Code
Connected No.
of Indoor Units
Model Code
Indication
Model
Inverter
Multi
Heat-pump
Cooling Only
Others
(1) Turn ON the power source of the units.
(2) Procedure for "TEST RUN" mode of remote control switch.
Depress the "MODE" and the "CHECK" switches together
for more than 3 seconds.
If "TEST RUN" and the counting number of the
connected units with the remote control switch
(for example "05") are indicated on the remote
control switch, the connection of remote control
cable is correct.
If no indication appears or the number of the units
indicated is smaller than the actual number of
the units, some abnormalities exist.
(3)
Back to (1) after checking
Back to (1) after checking
(4) Select TEST RUNNING MODE by depressing "MODE" switch. (COOL or HEAT)
(5) Depress "RUN/STOP" switch.
The "TEST RUN" operation will be started. (The 2 hours OFF-TIMER will be set and the "TEST RUN" operation
will be finished after 2 hours unit operation or by depressing the "RUN/STOP" switch again.)
NOTE:
The "TEST RUN" operation ignores the temperature limitation and ambient temperature during heating
operation to have a continuous operation, but the protections are alive.
Therefore, the protection may activate when the heating "TEST RUN" operation is performed in high ambient temperature.
If the units do not start or the operation lamp on the remote control switch is flashed,
some abnormalities exist.
(6)
Remote
Control Switch
Indication
No Indication
* The power source of outdoor unit is not turned ON.
* The connection of the remote control cable
is incorrect.
* The connecting wires of power supply line
are incorrect or loosed.
1. Connecting Points of Remote Control Cable Terminal
Board of Remote Control Switch and Indoor Unit
2. Contact of Terminals of Remote Control Cable
3. Connecting Order of each Terminal Boards
4. Screw Fastening of each Terminal Boards
* The power source of outdoor unit is not turned ON.
* The operating line wiring between indoor unit and
outdoor unit is not connected.
Counting
number of
connected units
is incorrect.
Inspection Points after the Power Source OFF
NOTE: "TEST RUN" shall be performed with each refrigerant cycle (each outdoor unit).
Remote Control
Switch Indication
The operation lamp
flashes. (1 time/1 sec.)
And the Unit No. and
Alarm Code "03" flash.
The unit does not
start.
The power source of outdoor unit
is not turned ON.
The connecting wires of operating
line are incorrect or loosed.
The unit does not
start.
Remote control cable is broken.
Contact of connectors is not good.
The connection of remote control
cable is incorrect.
This is the same as items (3)-1 and 2.
The unit does not
start, or starts once
and then stops.
The connection of the thermistors
or other connectors are incorrect.
Tripping of protector exists, or elses.
Check by the abnormality mode table 7.3 and
(Do it by service people.)
1. Connecting Order of each Terminal Boards
2. Screw Fastening of each Terminal Boards
NOTE:
Recovering method of FUSE for operating circuit.
There is a fuse ("FUSE4" on Indoor Unit PCB1, "EF1"
on Outdoor Unit PCB1) to protect operating circuit
on the PCB, when the power lines are connected to
operating lines.
If fuse is melted, operating circuit can be recovered
once by setting the dip switch on the PCB, as below.
The operation lamp
flashes. (1 time/2 sec.)
Indication or flash
except above.
The unit does not
start.
The connection of the remote
control cable between indoor units
is incorrect.
The operation lamp
flashes. (1 time/1 sec.)
And the Unit No.
00
.
Alarm Code
dd
and
Unit Code
E.00
flash.
Unit Condition
Wrong Portions
Wrong Portions
Inspection Points after the Power Source OFF
* Set the switch #1 to ON position to recover the
operation circuit.
ON
OFF
Indoor Unit PCB1
DSW7
1 2
TEMP.
RUN / STOP
MODE FAN SPEED
VENTI
RESET
CHECK
LOUVER
ON/OFF TIMER
TIME
COOL
HIGH
A/C
SET TEMP.
CHECK
UNIT
CHECK
MODE
Setting Temperature
Operation Lamp
Remote Control Switch
Alarm Code Indication of Remote Control Switch
24
table 7.4.
Check by the abnormality mode table 7.3 and
(Do it by service people.)
table 7.4.
Содержание 3HRNM1Q
Страница 2: ......
Страница 3: ...23WB 43 DB 30 DB 17 WB 15WB 5 DB 15 DB 20 WB ...
Страница 8: ...RAS 3HRNM1Q 1 Safety Summary 2 Structure Electronic Four way ...
Страница 35: ......
Страница 36: ...P00691Q 2013 11 V00 ...