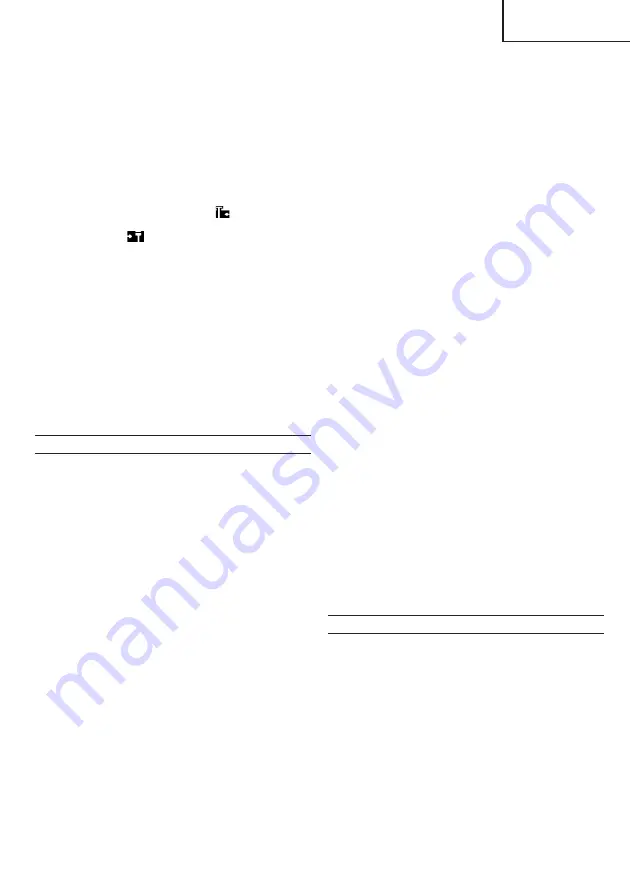
English
34
(2) Safekeeping of nose cap
Put the removed nose cap in a space behind the
magazine for safekeeping. (
Fig.13
)
3. Adjusting the nail-driving depth
CAUTION:
When making adjustments, be sure remove your
finger from the trigger. When making adjustments,
be sure that the nail outlet is not facing downward
and that body parts or other persons are not in the
path of the nail outlet.
䡬
Adjusting the adjuster (
Fig. 14
)
Carry out test driving. If the nails are too deep, turn
the adjuster to the shallow side (
mark).
If the nail depth is too shallow, turn the adjuster to
the deep side (
mark) (see
Fig. 14, 15
).
Depth is changed 1 mm with each rotation of the
adjuster.
NOTES:
䡬
When adjusting the adjuster, it does not rotate more
than 3 mm from the deepest point where a nail goes
down. Do not rotate the adjuster by force beyond that
point.
䡬
The nail-driving depth can also be adjusted by
changing the air pressure used. Carry this out together
with movement of the adjuster. Using a high air
pressure that does not match the nail-driving
resistance will shorten the life of this nailer.
4. Changing the exhaust direction
The direction of the exhaust vent can be changed
within 360° by turning the top cover. (
Fig. 16
)
INSPECTION AND MAINTENANCE
CAUTION:
Be sure to disconnect the hose during cleaning
jams, inspection, maintenance and cleaning.
1. Countermeasure for nail jamming
(1) Remove the nail roll from the magazine, open the nail
guide, insert a rod into the nail outlet and tap the rod
with a hammer. (
Fig. 17
).
(2) Remove the jammed nail with slotted-head
screwdriver. (
Fig. 18
)
(3) Cut off the defective part of the steel wire which links
the nails with cutting nippers, correct the deformation,
then load the nail roll in the magazine.
(4) In case of frequent jam, consult the Authorized Service
Agent from which you bought this machine.
2. Check on mounting screws for each part
At regular intervals check every part for loose
mounting screws and whether or not there are any
air leaks. Retighten any loose screws. Operating the
equipment with loose screws untightened will incur
a hazard.
3. Inspecting the push lever
Check if the push lever can slide smoothly. (
Fig. 19
)
Clean up the sliding area of the push lever and use
the provided oil for lubrication from time to time.
Lubrication enables smooth sliding and
simultaneously serves to prevent the formation of
rust.
4. Inspecting the feeders
(1) Occasionally clean the knob sliding part and then
apply the recommended oil. (See
Fig. 20
)
(2) Open the nail guide and remove dust, etc., as shown
in
Fig. 21
. Apply lubricant to the sliding groove of the
feeder and feeder shaft. Check nail stopper (A) and
nail stopper (B) slide smoothly by pushing them with
your finger.
(3) Also, apply the recommended oil to the feeding
surface of the nose and nail guide after cleaning. This
promotes smooth operation and retards corrosion.
CAUTION:
Check for smooth movement of the feeders and
stoppers before use. If movement is uneven, nails
could be fired at an irregular angle, presenting a
hazard to the operator and others nearby.
5. Inspecting the magazine
Clean the magazine. Remove dust of wooden chips
which may have accumulated in the magazine.
6. Storing
䡬
When not in use for an extended period, apply a thin
coat of the lubricant to the steel parts to avoid rust.
䡬
Do not store the Nailer in a cold weather environment.
Keep the Nailer in a warm area.
䡬
When ot in use, the Nailer should be stored in a warm
and dry place.
Keep out of reach of children.
7. Service parts list
A : Item No.
B : Code No.
C : No. Used
D : Remarks
CAUTION:
Repair, modification and inspection of Hitachi Power
Tools must be carried out by an Hitachi Authorized
Service Center.
This Parts List will be helpful if presented with the
tool to the Hitachi Authorized Service Center when
requesting repair or other maintenance.
In the operation and maintenance of power tools, the
safety regulations and standards prescribed in each
country must be observed.
MODIFICATIONS:
Hitachi Power Tools are constantly being improved
and modified to incorporate the latest technological
advancements.
Accordingly, some parts (i.e. code numbers and/or
design) may be changed without prior notice.
COMPRESSOR
CAUTION:
When the maximum, operating pressure of the air
compressor exceeds 8.3 bar, be sure to provide a
reducing valve between the air compressor and nailer.
Then, adjust the air pressure within the operating
range of 4.9 ~ 8.3 bar. If the air set is installed,
lubrication is also possible, thus providing additional
convenience.